Flowserve LPNV Worthington User Manual
Page 20
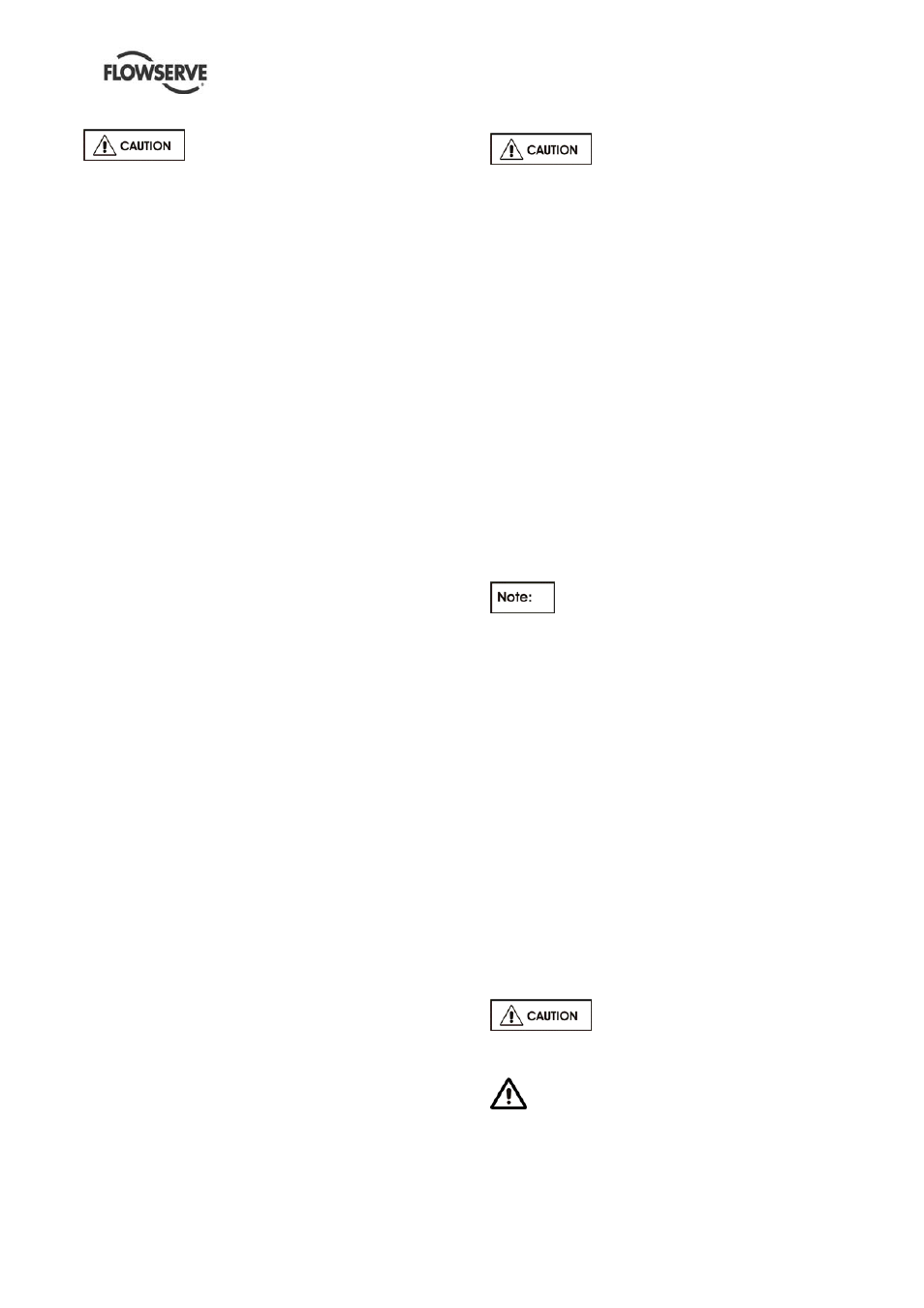
LPNV USER INSTRUCTIONS ENGLISH 87900031 – 06/14
Page 20 of 48
4.3.7 Hot alignment check
As both pump and driver may
rise when they reach operating temperature, it
is necessary to allow for this expansion when
aligning the shafts. Refer to elevation drawing
for approximate rise of pump and driver.
Consult driver manufacturer’s instructions. A
final alignment check (hot check) must be
made as soon as possible after both driver and
pump are heated to their normal operating
temperatures.
A hot check can only be made after the unit has
been in operation a sufficient length of time to
assume its normal operating temperature and
conditions. If the unit has been correctly cold set,
the parallel misalignment will be
within the limits
stated on par 4.3.3
when in operation. If not make
adjustments.
4.4
Piping
Never use the pump as a support
for piping.
4.4.1 General
These units are furnished for a particular service
condition. Changes in the hydraulic system may
affect performance adversely. This is especially
true if the changes reduce the pressure at the
suction or if the liquid temperature is increased. In
case of doubt contact FLOWSERVE.
Suction and discharge piping should be of ample
size, be installed in direct runs, and have a
minimum of bends. Double bends must be avoided
in suction line and a straight run of pipe, equal 8 to
10 times the pipe diameter is desired directly
upstream of the suction nozzle.
In order to minimize friction losses and hydraulic
noise in the pipework it is good practice to choose
pipework that is one or two sizes larger than the
pump suction and discharge. Typically main
pipework velocities should not exceed 2 m/s (6
ft/sec) suction and 3 m/s (9 ft/sec) on the
discharge.
Provision must be made to support
piping external to the pump to prevent excessive
nozzle loads, maintain pump/driver alignment and
avoid pipe induced vibrations.
Take into account the available NPSH which must
be higher than the required NPSH of the pump.
Maximum forces and moments allowed on the
pump flanges vary with the pump size and type. To
minimize these forces and moments that may, if
excessive, cause misalignment, hot bearings, worn
couplings, vibration and the possible failure of the
pump casing, the following points should be strictly
followed:
Prevent excessive external pipe load.
Never draw piping into place by applying force
to pump flange connections.
Do not mount expansion joints so that their
force, due to internal pressure, acts on the
pump flange.
Ensure piping and fittings are
flushed before use.
Ensure piping for hazardous liquids is
arranged to allow pump flushing before
removal of the pump.