Flowserve BP User Manual
Page 17
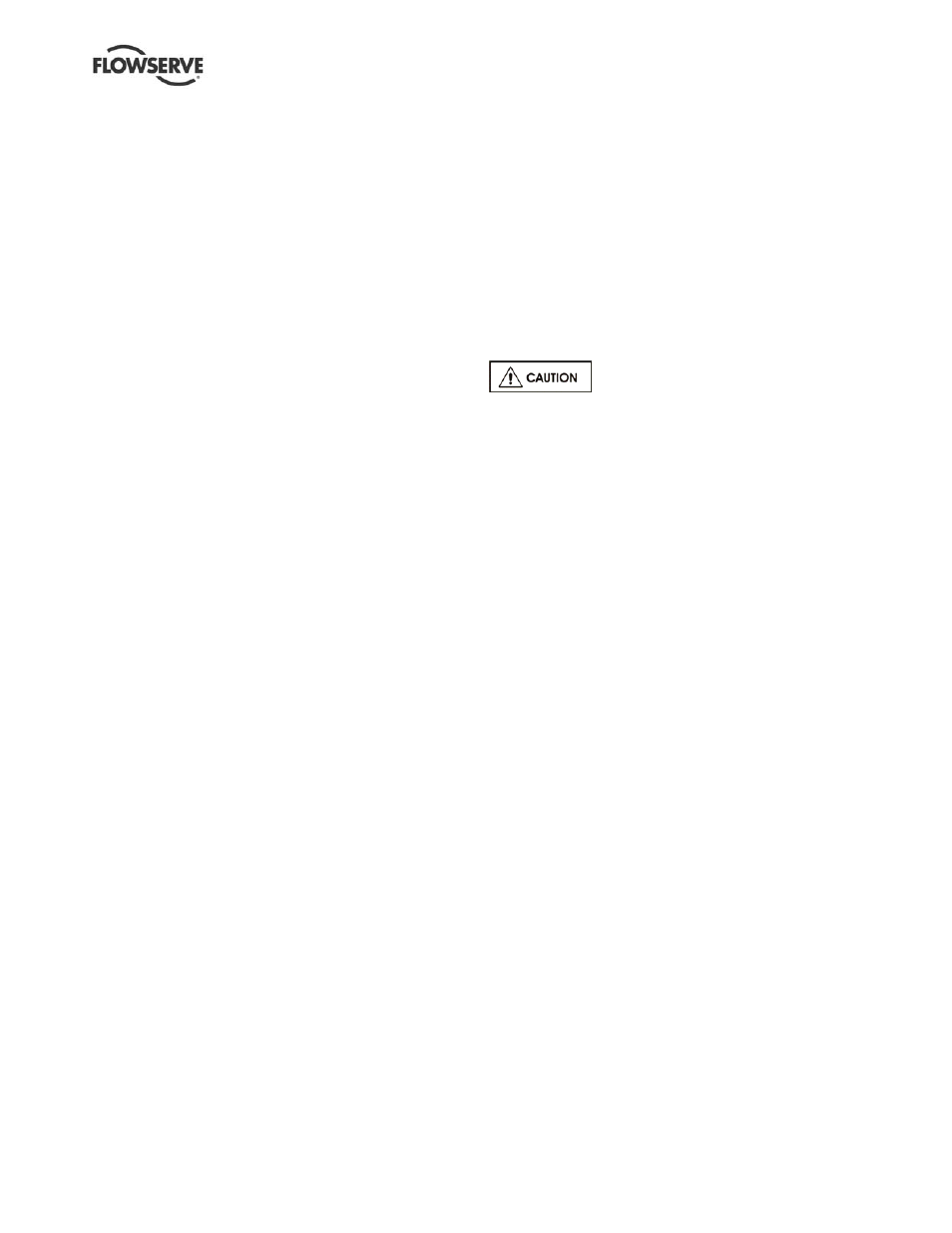
BP USER INSTRUCTIONS ENGLISH 85392725 10-09 (E)
Page 17 of 44
flowserve.com
4.6.2 Suction
piping
a) The inlet pipe should be one or two sizes larger
than the pump inlet bore and pipe bends should
be as large a radius as possible.
b) On suction lift the piping should be inclined up
towards the pump inlet with eccentric reducers
incorporated to prevent air locks.
c) On positive suction, the inlet piping must have a
constant fall towards the pump.
d) The pipe next to the pump should be the same
diameter as the pump suction and have a minimum
of two pipe diameters of straight section between
the elbow and the pump inlet flange. Where the
NPSH margin is not large, it is recommended that
the pipe straight is 5 to 10 pipe diameter. (See
section 10.3, Reference 1.) Inlet strainers, when
used, should have a net 'free area' of at least three
times the inlet pipe area.
e) Fitting isolation and non-return valves will allow
easier maintenance.
f) Never throttle pump on suction side and never
place a valve directly on the pump inlet nozzle.
4.6.3 Suction
strainer
a) It is recommended that a temporary strainer be
installed in the suction pipe near the pump to
prevent lodging of foreign material in the impeller.
Provide with pressure gauges before and behind
strainer in order to check the pressure drop at the
strainer.
b) The net area of the strainer should be three or
four times the area of the suction pipes.
c) The temporary strainer may be removed, when it
has become not to be clogged any more after
repeating check and clean
4.6.4 Discharge
piping
a) Install the check valve between the pump and the
discharge valve to protect the pump from any
possible excessive back pressure or from reverse
rotation caused by liquid running back through
the casing during driver or power failure.
b) Satisfactory operation cannot be maintained
when excessive forces and moments from piping
imposes on the pump. If excessive, they will
become a common cause of misalignment, hot
bearings, worn couplings and vibration. Design
and install the pipings so as not to impose
excessive forces and moments from piping on
the pump.
c) Suction and discharge pipes and associated
equipment should be supported and anchored
near but independent of the pump.
d) Design and install the pipings and supports so as
to be allowed for movement of piping due to
expansion or contraction.
e) Before connecting the flanges between pump
and piping, confirm to be able to insert smoothly
the bolts into the bolt holes of flanges, and that
parallel between both flange faces is within 0.5
mm (0.020 in) by thickness gauge. Check and
see four point (every 90°).
f) If error of more than 0.15 mm (0.006 in) in the
centring of coupling occurs by connecting the
pipings to the pump, disconnect and adjust the
pipings and supports again.
g) The piping should be flushed and cleaned
thoroughly before connecting it to the pump.
4.6.5 Auxiliary
piping
The connections that are to be piped
up will have been fitted with protective metal or
plastic plugs which will need to be removed.
Piping needed for each pump for auxiliary piping is
shown below. Install the piping in accordance with
piping drawings supplied.
a) Drain and vent piping
b) Cooling
piping
c) External sealing piping or self flushing piping
d) Quenching
piping
e) Steam
piping
f) Others
4.6.6 By-pass piping (minimum flow piping)
If the capacity sent from the pump to the system is
less than the minimum flow rate of the pump, the
pump should operate at more rate than minimum flow
rate and the remainder capacity should be returned to
the suction tank or others through the by-pass piping,
in order to operate safely the pump at reduced
capacity. Install a by-pass piping in above case.
4.6.7 Warming
piping
It is recommended to perform warming prior to
operation for the pump handling liquids over of 100℃.
Warming is performed by pouring liquid back from the
discharge side. Better result will be achieved for
pumps with 200 mm (8 in) or over discharge nozzles,
if the liquid is poured from both drain port and
discharge side of the pump.
4.6.8 Allowable Nozzle loads
The values permitted are listed below and are twice
the value of API 610. Values are presented in
compliance with the ISO 1503 sign convention.
All individual values which are greater than the
following values must be referred to Flowserve for
approval.