Flowserve BP User Manual
Page 33
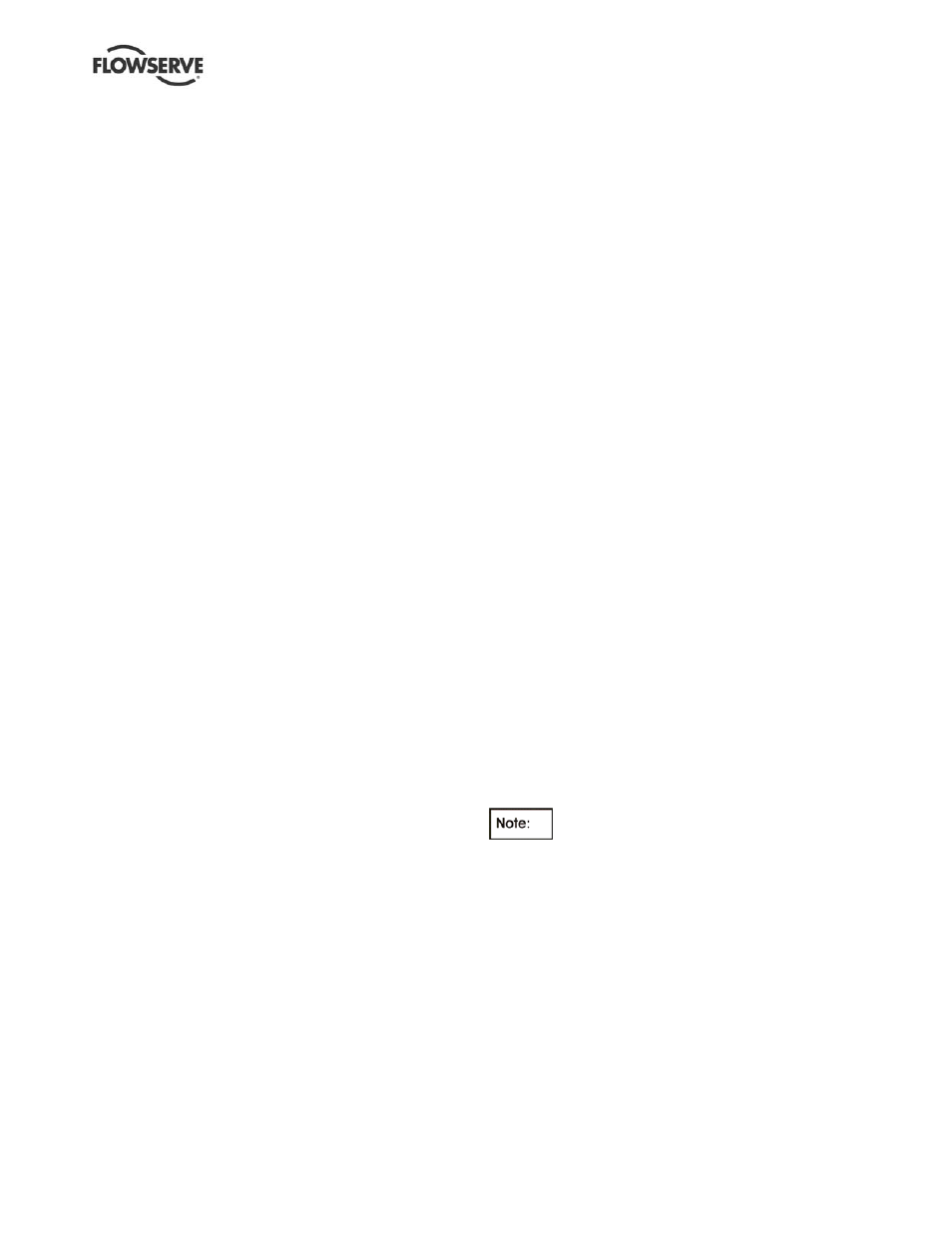
BP USER INSTRUCTIONS ENGLISH 85392725 10-09 (E)
Page 33 of 44
flowserve.com
element into the fits of the casing barrel by using
the center bolts & nuts and the plate (Tool List
No.17 & No.18).
h) If the stage piece [1460] has inserted into the fits
of the casing barrel and held in place, remove all
the tools (the extension sleeve, shaft lug, plate,
center bolts and nuts) attached to the inner
element. At this point in time, support the
coupling end of the shaft on the wooden stands
and reassemble all the parts on the discharge
(thrust) end as follows.
6.10.4 Assembling Discharge End
a) Insert the dowel pin into the reamed hole in the
last stage diffuser [1413].
b) Again inspect the high-pressure joint faces on the
barrel and discharge head to make sure they are
smooth and free from nicks or scratches which
extend across the face and therefore might cause
leakage. Also check the “spiral wound gasket”
seat face in the barrel.
c) Insert the spiral wound gasket [4590] on the seat
face in the casing barrel.
d) Insert the element spring [4260] into the last
stage diffuser [1413], using a little grease or three
bond to hold it in place.
e) Make certain that the dowel pin is fixed to the last
stage diffuser [1413].
f) Install the discharge head [1221] with the
balancing ring [1600] in place. Bring the
discharge head into position, then move forward
with extreme caution using some casing studs
[6572], nuts and washers and readjusting hoist or
crane if necessary, until the discharge head
enters smoothly into its fit in last stage diffuser,
and the discharge head pressure face is against
the mating face in the casing barrel. Secure the
discharge head to the barrel by tightening several
of the nuts before releasing the hoist or crane.
Tightening instructions for discharge head [1221]
g) Apply a suitable lubricant to the thread. Run the
nut back and forth on the stud to insure even
distribution of lubricant. Avoid lubricant build-up
between faces of nut and washer and/or
discharge head.
h) Tighten the nut and washer against the discharge
head with a hand wrench.
i) Tighten firmly the nuts with a torque wrench or
hydraulic wrench. Tightening torque refer to
recommended torque. See “Recommended
torque Table” in section 10.4 Technical Data
Sheet.
j) Nuts should be tighten in logical order, i.e. each
nut to be tightened should be nearly diametrically
opposite from the previously tightened.
k) At this point, check the total movement of the
rotor by moving the shaft toward inboard and
outboard.
For the value of movement, see “Rotor movement
(axial total end play)” in section 10.4 Technical Data
Sheet.
l) Insert the spiral wound gasket [4590] on the
gasket seat face in the discharge head [1221].
m) Install the stuffing box [4112] with the throat
bushing [4132] into the discharge head [1221].
n) Install carefully the mechanical seal with the shaft
sleeve into the stuffing box [4112] according to
the instruction manual for mechanical seal. At
this stage, mechanical seal must not be secured
on the shaft by set screws nor secured in the
stuffing box by tightening the nuts for gland
studs.
o) Insert and slide the deflector [2540] on the shaft
until they get closer to the mechanical seal.
6.10.5 Assemble Thrust Bearing
a) Stuffing box and the thrust bearing housing
[3230] with the same thickness recorded at
disassembly, install horizontal and vertical
adjusting screws in the stuffing box mounting
flange.
b) Install lower half of thrust bearing housing [3230]
to the stuffing box [4112] with taper pins and the
studs, nuts for studs have to be temporarily
fastened.
c) Wipe a film of oil on journal area of shaft. Place
lower half of journal bearing [3020] on shaft.
Wipe a film of oil on lower half of journal bearing.
Roll lower half of journal bearing into lower half of
bearing housing [3230]. Now the bearing
housing is temporarily positioned to the stuffing
box.
d) Pour a small amount of oil on journal bearing and
journal area of shaft.
Bearing housings position is pre-determined
at the factory and secured by taper pins, but the
positioning of the bearing housings by these pins has
to be confined only at the repair of mechanical seals.
At the complete overhaul of the pump, positioning of
the bearing housings has to be conducted without
these pins, but by positioning of pump rotor by the
manner described on section 6.9.7. Horizontal /
Vertical Shaft Alignment.
e) Rough assembly is now completed, but the final
adjustment has to be conducted after the
temporarily positioning of the radial bearing
housing.