Flowserve BP User Manual
Page 27
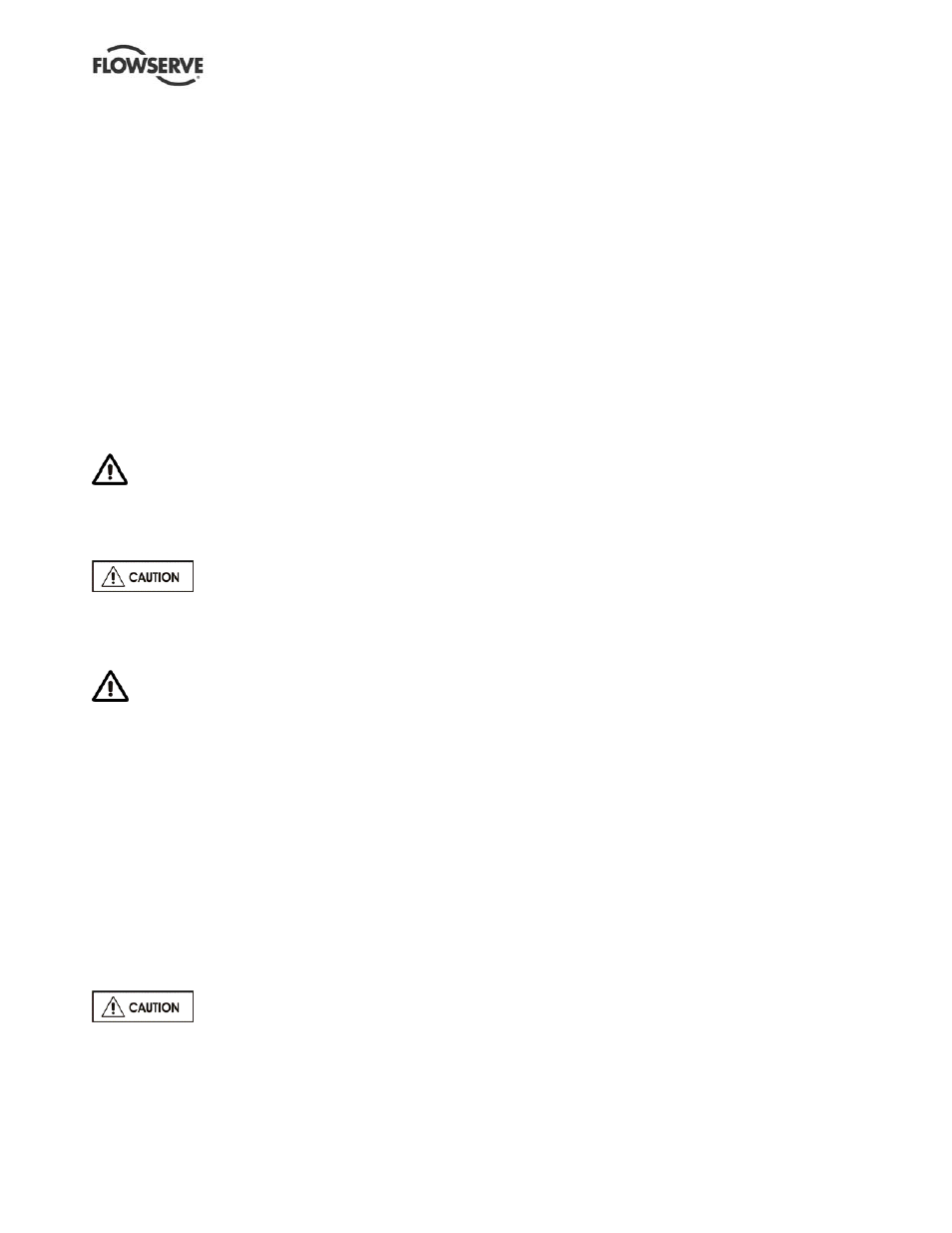
BP USER INSTRUCTIONS ENGLISH 85392725 10-09 (E)
Page 27 of 44
flowserve.com
N.B.
*1 When axial probes & key phaser are required
*2 When return channel vane of intermediate diffuser
is even number
*3 When return channel vane of intermediate diffuser
is odd number
*4 When impeller is clearance fit on shaft
6.6 Fastener
torques
Torque values will appear in the section of
“Assembling Procedure”. They are selected to
achieve the correct amount of pre-stress in the
threaded fastener. Maintenance personnel must
ensure that threads are in good condition (free of
burrs, galling, dirt etc. ) and that commercial thread
lubricant is used. Torque should be periodically
checked to assure that it is at the recommended
value.
When reassembling the pump, all fasteners
must be tightened to the correct torque value. Failure
to observe this warning could result in injury to
operating personnel
Non-metallic gaskets incur creep
relaxation - before commissioning the pump check
and retighten fasteners to tightening torques stated.
6.7 Disassembly
Refer to Safety section before dismantling the
pump.
Dismantle the pump carefully not to damage internal
parts of the pump. Arrange dismantled parts in order
so as to facilitate reassembling.
Protect metal contact surfaces against corrosion.
Close the suction and discharge valves and open the
casing drain valve to remove liquid from the casing.
Remove the pump casing drain pipings as well as
flushing pipings.
In dismantling the pump, it is desirable to record
clearances and important dimensions prior to
disassembly, because they are convenient checks on
the correctness of the rebuilding process.
Before dismantling the pump for
overhaul, ensure genuine Flowserve replacement
parts are available.
Refer to section drawing and parts list for location of
parts. The numbers in parentheses are part numbers
in the section drawing of the pump. See section 8,
Parts lists and drawings.
6.7.1 Drive End Bearing (Radial or Line Bearing)
Removal
a) Isolate power supply to motor.
b) Close suction and discharge valves. Drain casing
by removing drain plug [Item 602]
c) Disconnect all auxiliary pipes and tubes where
applicable.
d) Remove coupling guard and disconnect coupling.
e) Disconnect lube oil supply and drain piping. Drain the
oil from the bearing housing.
f) Remove the coupling nut [7411] and coupling
hub on the pump shaft. In removing coupling
nuts, use a face spanner wrench (Tool List No.5).
g) If fitted, loosen the set screws in the deflector
[2540] and remove it from end of shaft.
h) Do the same for the deflector located on the
other side of the bearing housing and slide it
back on the shaft towards the mechanical seal.
i) Loosen and remove nuts holding the upper half
of the radial bearing housing [3200] (bearing cap)
to the suction head [1222]. Remove cap screws
and dowel pins furnished between upper and
lower half of bearing housing. Rig eye bolt in
bearing cap to an overhead hoist and lift it from
lower half of bearing housing and place on
blocking on floor.
j) Remove cap screws and dowel pins from journal
bearing.
k) Remove upper half of journal bearing. Using a
bar and a block of wood under the pump shaft,
raise shaft slightly and roll out the lower half of
journal bearing.
l) Install two eye bolts on the lower half of bearing
housing [3200] and rig to an overhead hoist.
Loosen and remove nuts holding bearing housing
[3200] to the suction head [1222]. Using the
overhead hoist, lower and remove bearing
housing away from the casing and place on
blocking on the floor.
m) Remove deflector [2540] located at the
mechanical seal side.
6.7.2 Thrust Bearing Removal
a) Remove bolts from bearing end cover [3266] and
remove the cover. Remove shim pack and
spacers [6196/3645].
If oil pump is mounted on thrust end of shaft
a) Remove bolts from oil pump on bearing end
cover [3266]. Remove gasket for oil pump.
b) Remove Lovejoy coupling and key from thrust
end of shaft.
c) Remove bolts from bearing end cover [3266] and
remove the cover with seal ring [4305].
d) Remove shim pack [6196/3645].