Flowserve BP User Manual
Page 22
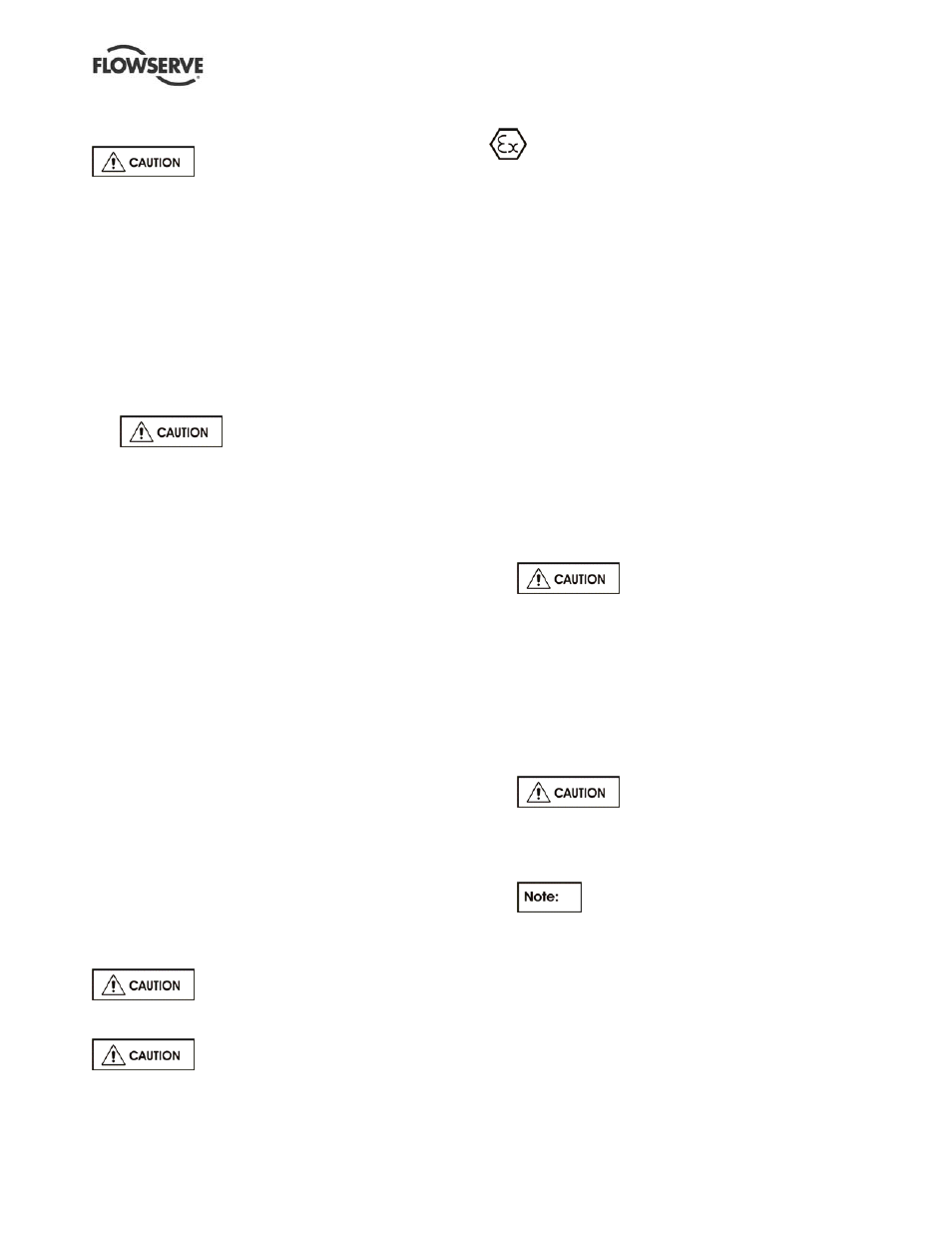
BP USER INSTRUCTIONS ENGLISH 85392725 10-09 (E)
Page 22 of 44
flowserve.com
5.6.3 Auxiliary
supplies
Ensure all electrical, hydraulic,
pneumatic, sealant and lubrication systems (as
applicable) are connected and operational.
Check the open or close condition of valves installed
in auxiliary piping lines.
Casing drain and vent valves: Closed
Valves for cooling: Open
Valves for flushing line of mechanical seal: Open
Valves for Sealing line of gland packing: Open
Preheat oil unit with steam heater 30 minutes before
pump start.
5.7 Starting the pump
a)
Ensure flushing and/or cooling/
heating liquid supplies are turned ON, before
starting pump.
b) Confirm that the suction valve is opened fully and
the discharge valve is closed completely. Open
minimum flow line, if installed.
c) Start the driver, according to driver
manufacturer’s instructions.
d) Check the discharge pressure and slowly open
the discharge valve as soon as the pump attains
full speed, and maintain pump capacity at the
rated or near the rated flow.
e) If the discharge pressure gauge does not indicate
the specific pressure when the rotor is revolving
at or near rated speed, immediately shut down
and make a careful check of the suction line.
f) Do not operate with discharge valve closed for
more than a few minutes, as pump will overheat
and may seize.
g) Do not operate pump at less than minimum flow.
h) Check and record periodically the running
conditions during operation.
i) Refer to section 7, Faults; causes and remedies
for fault diagnosis.
5.8 Running the pump
5.8.1 Pumps fitted with mechanical seal
Mechanical seals require no adjustment. Any slight
initial leakage will stop when the seal is run in.
External flush or quench should be
started before the pump is run and allowed to flow for a
period after the pump has stopped.
Never run a mechanical seal dry,
even for a short time.
5.8.2 Bearings
If the pumps are working in a potentially
explosive atmosphere temperature or vibration
monitoring at the bearings is recommended.
If bearing temperatures are to be monitored it is
essential that a benchmark temperature is recorded
at the commissioning stage and after the bearing
temperature has stabilized.
Record the bearing temperature (t) and the
ambient temperature (ta)
Estimate the likely maximum ambient
temperature (tb)
Set the alarm at (t+tb-ta+5) ºC (t+tb-ta+10) ºF
and the trip at 100 ºC (212 ºF) for oil lubrication
It is important to keep a check on bearing
temperatures. After start up the temperature rise
should be gradual, reaching a maximum after
approximately 1.5 to 2 hours.
This temperature rise should then remain constant or
marginally reduce with time. Refer to section 6.2.3
Re-lubrication for further information.
5.9 Stopping and shutdown
a)
Close the discharge valve
gradually and stop the driver.
b) When a by-pass line for minimum flow is
provided, close the discharge valve completely,
making sure the valve on the by-pass line is fully
open.
c) Once the pump has stopped close the discharge
and suction and by-pass valves.
d) Close all valves in the auxiliary piping as required
after the pump has stopped completely.
e) Stop the auxiliary oil pump.
f)
For prolonged shut-downs and
especially when ambient temperatures are likely
to drop below freezing point, the pump and any
cooling and flushing arrangements must be
drained or otherwise protected.
g)
In case of handling a liquid liable to
solidify during shut-down, clean the pump interior
well and replace with any other liquid (for
example, water), after stopping the pump.
5.9.1 Stand-by
operation
Perform the following for stand-by operation so that
the pump can be started at any time.
a) Open the suction valve fully.
b) Vent air and gas from the pump and fill the pump
with liquid.