Function, Installation, Installation of the measuring electrode – Flowserve LRGT16-1 Spector compact Conductivity Transmitter System User Manual
Page 5
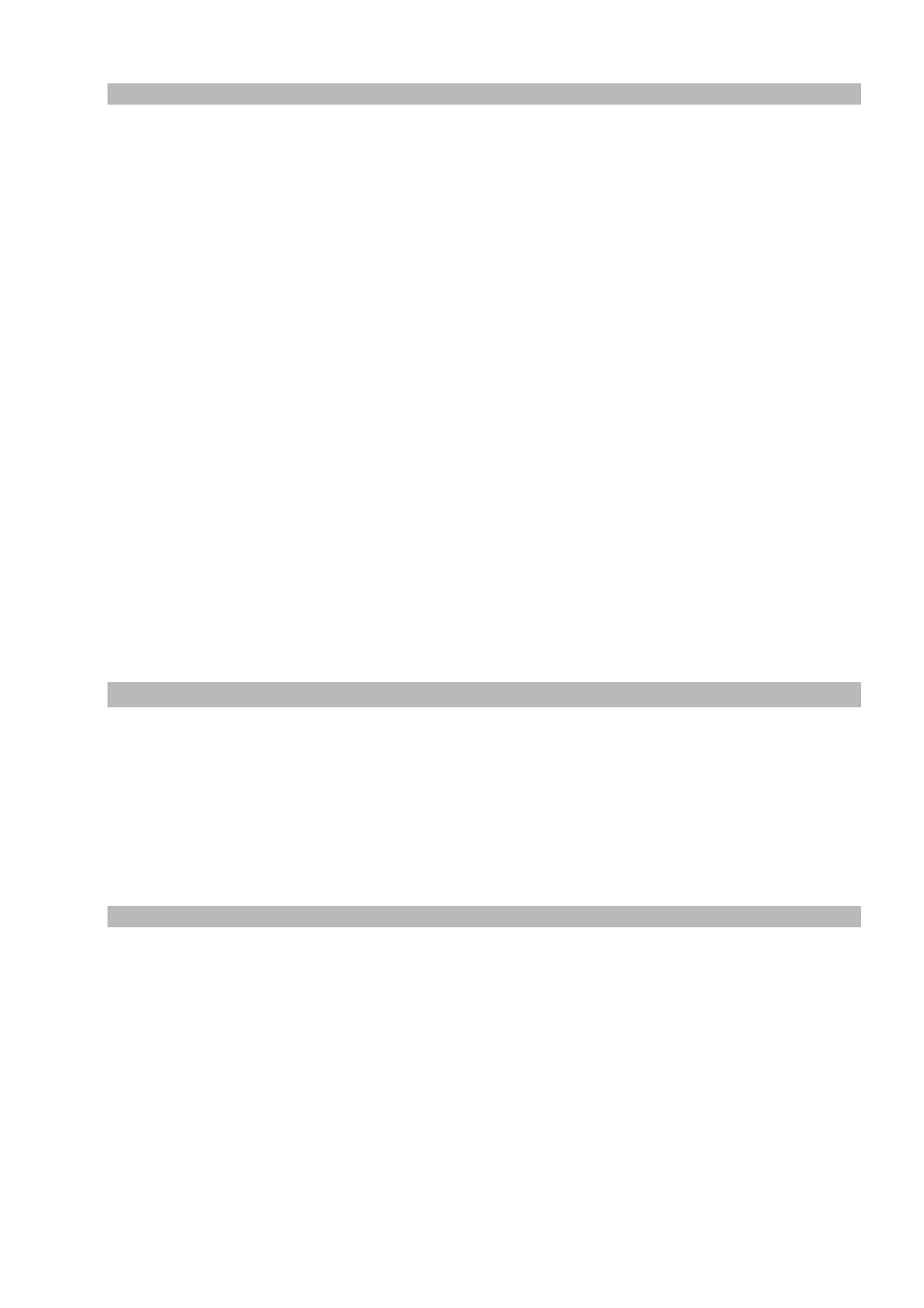
Function
A measuring current of variable frequency flows through the fluid and creates a potential
gradient between the measuring electrode and the measuring tube. The potential gradient
is evaluated as measuring voltage U
U
.
In order to compensate for polarisation, which would reduce the measuring current, the
measuring frequency is adapted accordingly. The resulting measuring current is sensed
and transmitted as measuring voltage U
I
.
The electrical conductivity changes as a function of temperature. The resistance
thermometer integrated in the electrode measures the fluid temperature and establishes a
reference temperature on which the measured values will be based.
The electrical conductivity is calculated from the measuring voltages U
U
and U
I
and -
depending on the adjusted temperature coefficient Tk - is based linearly on the reference
temperature 25 °C. After converting it into a conductivity-proportional current signal, a
current of 4 - 20 mA is provided for external processing.
The cables leading to the measuring electrode, the measuring tube and the resistance
thermometer are monitored for interruption and short circuits. In addition, the electronic
insert is protected against excessive temperatures in the terminal box. In case of a
malfunction the LEDs are permanently illuminated or flashing and the current signal is set
to 0 or 0.5 mA.
The transmitter is parameterised via code switch. The code switch can also be used for
adaptation of the cell constant and triggering a functional test.
The electrical conductivity is measured in µS/cm. In some countries use is also made of
ppm (parts per million). Conversion: 1 µS/cm = 0.5 ppm.
Installation
The conductivity transmitter system is designed such that it can be screwed directly into
boiler standpipes or suitably tapped flanges.
The electrode must be installed such that it is always submerged.
The installation in protection tubes is not permitted according to WÜ 100.
Ensure a minimum distance of approx. 20 mm between the lower part of the measuring
tube and the boiler wall, the smoke tubes, any other metal parts and the low water level
(LW).
Installation of the Measuring Electrode
1. Check seating surfaces of threads or flange provided on vessel or boiler standpipe.
2. Place ring joint onto the seating surface of the transmitter. Note: Use only ring joint (of
stainless steel 1.4301 E8P) D 33 x 39 to DIN 7603 supplied with the electrode.
3. Apply a light smear of silicone grease (e. g. DOW Corning 111 Compound) to electrode
thread.
4. Screw conductivity transmitter electrode into threads or flange provided on vessel or
boiler standpipe and tighten with a 41 mm open-end spanner. The torque required
when cold is 150 Nm. The tapped hole must conform to DIN 3852 part 2, 1" BSP (DIN
ISO 228) form X or Y, standard version. The subsequent hole must have a diameter of
> 24 mm.
5