3 audience, 2 direct-to-host valve control, 1 advantages of direct-to-host control – Flowserve DDC-100 Modbus Direct-to-Host User Manual
Page 4: Direct-to-host valve control
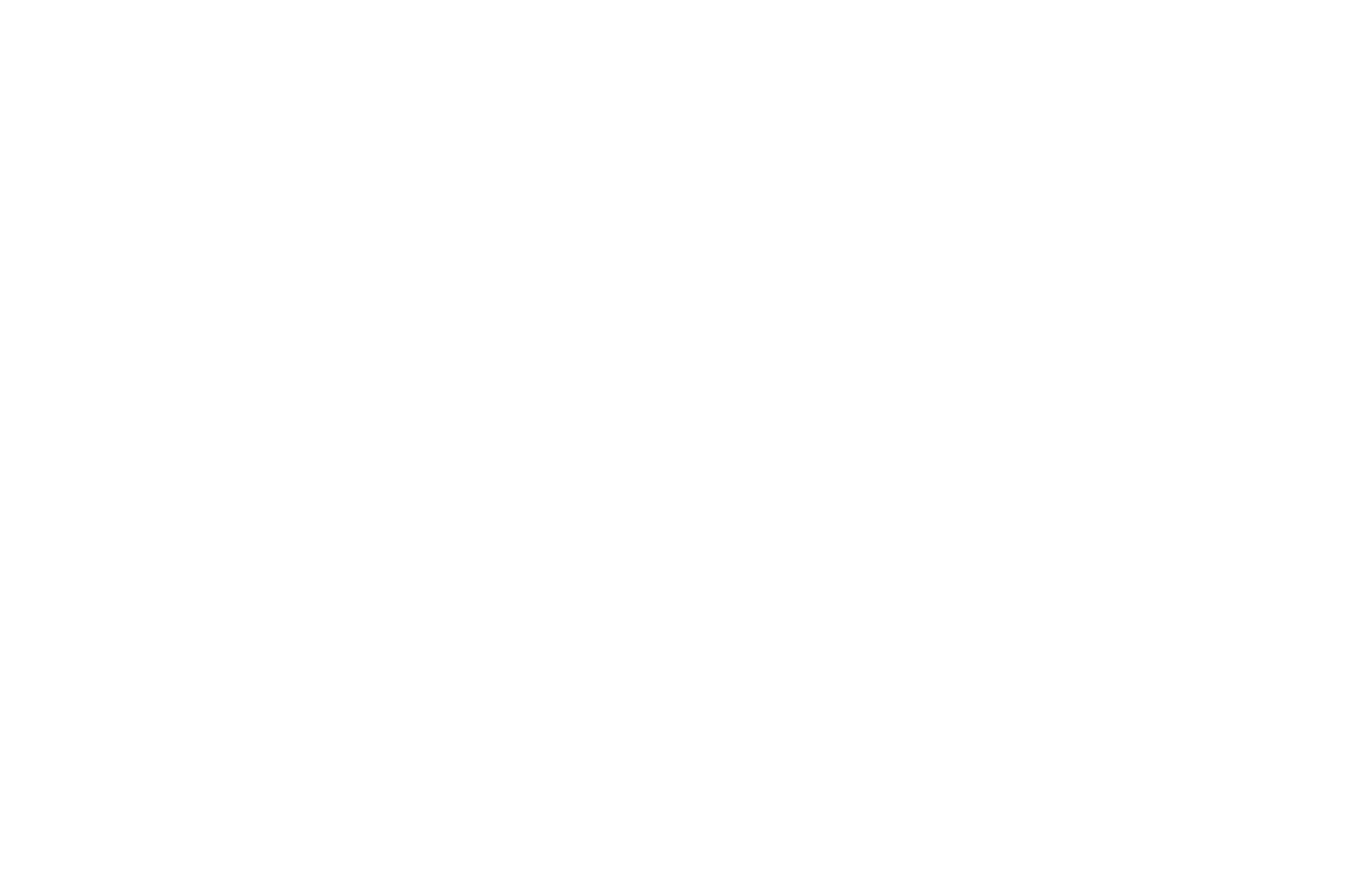
2
DDC-100 Direct-to-Host Programming Guide
FCD LMAIM4019-00
FCD LMAIM4019-00
DDC-100 Direct-to-Host Programming Guide
3
1.3 Audience
These guidelines were written to help you successfully connect Limitorque valve actuators directly
to a control system Host computer. You do not have to be an expert in electronics or digital controls
to utilize this manual. However, this manual assumes that you have a working understanding of
valve actuators and a fundamental understanding of control system programming.
The following manuals should be available before attempting to connect the valve actuators to the
control system:
1) Accutronix Installation and Operation for MX-DDC Field Unit Manual
Bulletin LMAIM1329
2) DDC-100 UEC Field Unit (Modbus®) Installation and Operation Manual
Bulletin LMAIM4029
3) DDC-100 UEC Field Unit Wiring and Startup Guidelines
Bulletin LMAIM4022
4) DDC-100 UEC Field Unit Installation and Commissioning Manual
Bulletin LMAIM4030
5) Modicon Modbus Protocol Reference Guide PI-MODBUS-300 Rev. G
available from Modicon
6) Valve actuator installation manual for the specific model(s) to be installed.
An understanding of valve actuators and digital control systems is beneficial to all system users.
Flowserve assistance and training is available to help you operate your system at top efficiency. It
is recommended that you read this entire manual before attempting to install the valve actuators in
your control system.
2
Direct-to-Host Valve
Control
In this document, Direct-to-Host valve control is defined as the use of a customer-supplied
(possibly pre-existing) Host control system (PLC, DCS, PC, etc.) to directly control the actuation of
valves that are equipped with DDC-100 Network-compatible field units. The field units are micro-
processor-based devices that can communicate with the Host and respond to Host commands for
valve motion and status. The DDC-100 Network uses the EIA RS-485 standard for the physical layer
and the A.E.G. Modicon Modbus protocol for the command structure.
The Direct-to-Host solution to valve actuation systems provides distinct advantages for many
users. These benefits range from maximizing system design flexibility to utilizing existing plant
equipment for valve actuator control. The customer can emphasize selecting the best equipment
and software that closely matches the application’s requirements. This solution allows the user to
add valve control while avoiding the need to incorporate new control equipment into the facility.
Direct-to-Host functionality is accomplished through the use of open architecture control and
communications in the valve actuator controls that economically accommodate widely available
interfaces for existing SCADA, PLC, or personal computers.
2.1 Advantages of Direct-to-Host Control
• Freedom to design a valve actuator system to interface directly with customer-preferred supervi-
sory equipment with open-market availability and off-the-shelf components.
• Maximizes valve actuator system flexibility by utilizing the industry standard protocol of Modbus,
complemented with the EIA RS-485 electrical standard.
• Increases control room equipment utilization while incorporating a cost savings to the customer
through the elimination of unnecessary hardware.
• Supports the use of control system components familiar to the user and eliminates the require-
ment to learn third-party interfaces.
• Strengthens control system architecture with components readily available on the open market.
• Encourages parts replacement and support programs favorable to the user.
• Promotes direct downloading of valve actuator data to the supervisory control system without
intervening proprietary hardware or protocols.