Sequence of operations, Troubleshooting – Orion System MUA II Controller User Manual
Page 18
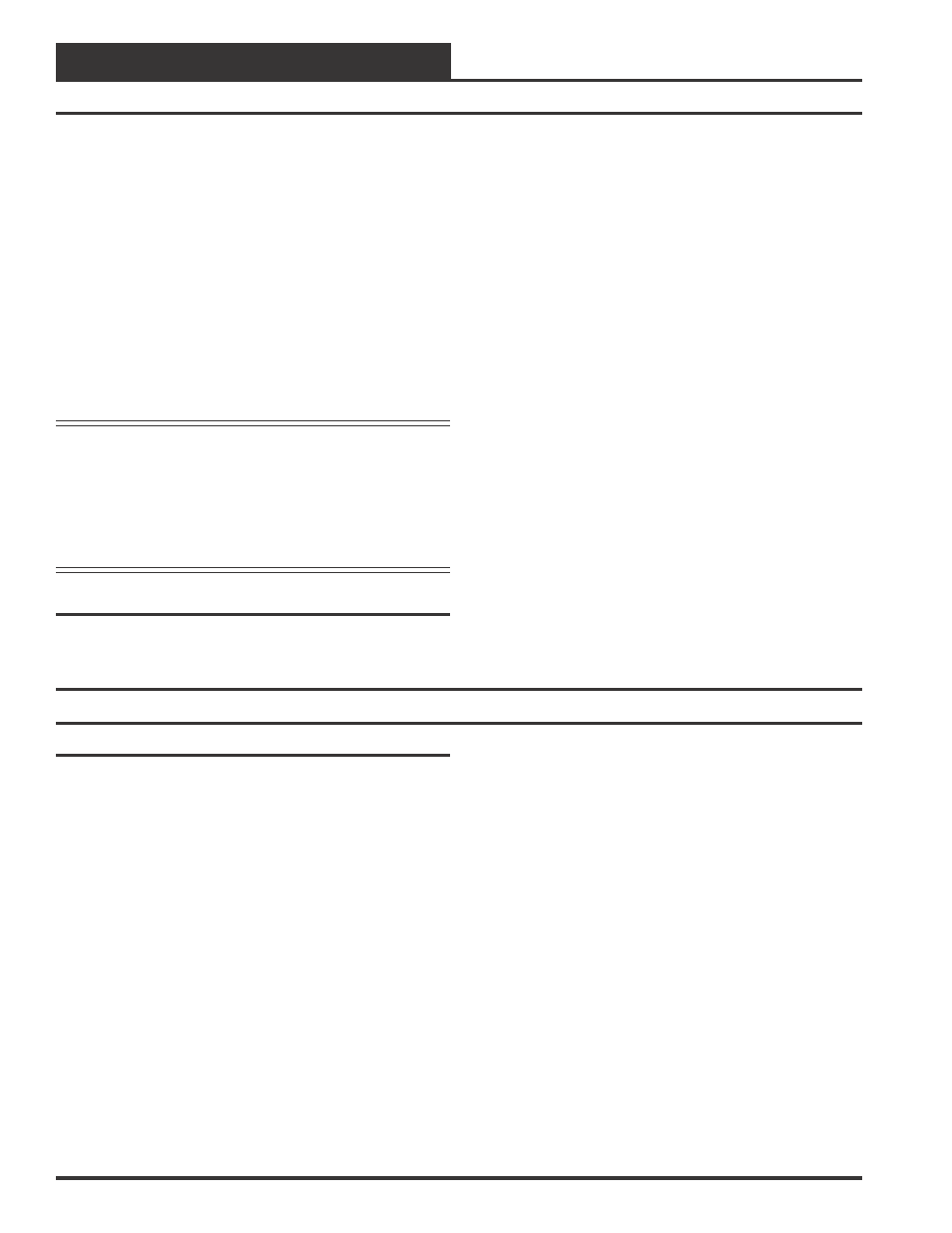
Technical Guide
MUA II Controller
18
Sequence Of Operations
When the analog outputs are forced, the display on the Modular Service
Tool or front-end can be interpreted as the actual voltage. During normal
operation, the display indicates the percentage signal applied based on
the user defined voltage limits. For example, if the user defines a 2.0
VDC to 10.0 VDC range, then 50% would be 6.0 VDC instead of the 5.0
VDC applied when the range is 0.0 VDC to 10.0 VDC.
As mentioned, force modes can only be activated with an attached re-
mote communications device described previously. Furthermore, the
override condition can only remain in effect as long as the remote device
is connected and communicating with the unit. That means that you
cannot set an override condition and then “walk away” from the equip-
ment with the override still active. The loss of communications or the
removal of the remote interface will automatically terminate the override
within 10 minutes. This is to protect the equipment and to prevent an
override condition from remaining active indefinitely resulting in ineffi-
cient operation of the equipment.
Caution:
No equipment protection is available during the
force mode of operation. That means you could
start a compressor without running the fan or
create other conditions that WILL damage the
HVAC equipment. WattMaster Controls, Inc.
assumes no responsibility or liability for the
misuse of these user overrides that cause damage
to the HVAC equipment!
Internal Trend Logging
The MUA II Controller continuously maintains an Internal Trend Log,
which records a fixed set of values at an interval programmed by the
user. These values can be retrieved only with the PRISM graphical
Using LED’s To Verify Operation
The MUA II controller is equipped with LEDs that can be used as very
powerful troubleshooting tools. Their are four LEDs on the MUA II
controller board. Three of these LEDs are used in troubleshooting. See
Figure 18 for the LED locations. The LEDs and their uses are as fol-
lows:
“COMM”
This LED will light up to indicate system communications.
“PWR”
This LED will light up to indicate that 24 VAC power has been applied
to the controller.
“LED1”
This LED is not used for this controller application.
“LED2”
This is the diagnostic blink code LED. It will light up and blink out
diagnostic codes.
PWR LED Operations
When the MUA II controller is powered up the “PWR” LED should
light up and stay on continuously. If it does not light up, check to be
sure that you have 24 VAC connected to the board, that the wiring
connections are tight and that they are wired for the correct polarity.
The 24 VAC power must be connected so that all ground wires remain
common. If after making all these checks the PWR LED does not light
up, please contact WattMaster technical support for assistance.
COMM LED Operations
When power is applied to the controller The “COMM” LED will also
light up. If this is a Stand Alone System (one controller only on the
loop) or an Interconnected System (several MUA II controllers tied
together without a CommLink) the COMM LED will glow continu-
ously. The COMM LED will flicker when you are connected to the
MUA II controller and you are entering setpoints with the Modular
Service Tool or the System Manager. It will also flicker if this is a
Networked System. If this is a Networked System (the system has a
CommLink installed) the COMM LED should flicker rapidly indicating
that the system is communicating. A “flicker” is defined as a brief mo-
ment when the LED turns off then back on. It may be easier to see this
“flicker” if you cup your hand around the LED.
front-end program. If you don’t have the Remote Communications op-
tion with a front-end program, you do not have access to these logs.
There are 120 log positions available. Once the last ( 120th ) position
has been recorded, the log jumps back to the first position and begins
overwriting the old data. This means the user is required to retrieve the
logs at an interval that is shorter than the duration of the last 120 logs.
Shown below are some log intervals and the duration of 120 logs.
1 Minute Interval =
2 Hour Duration
15 Minute Interval =
30 Hour Duration
30 Minute Interval =
60 Hour Duration
60 Minute Interval =
120 Hour Duration
The fixed items in the log are listed below:
Date
Time
Supply Air Temperature
Outside Air Temperature
Supply Air Setpoint
Outdoor Air Humidity
Dewpoint Setpoint
Onboard Relay Status ( BIT Pattern )
Expansion Board Relay Status ( BIT Pattern )
External Heat (% Of Max Heat )
These items and values are explained in greater detail in the PRISM
manual.
Troubleshooting