Electronic lineshaft with alignment – Yaskawa G5 Electronic Lineshaft Alignment User Manual
Page 12
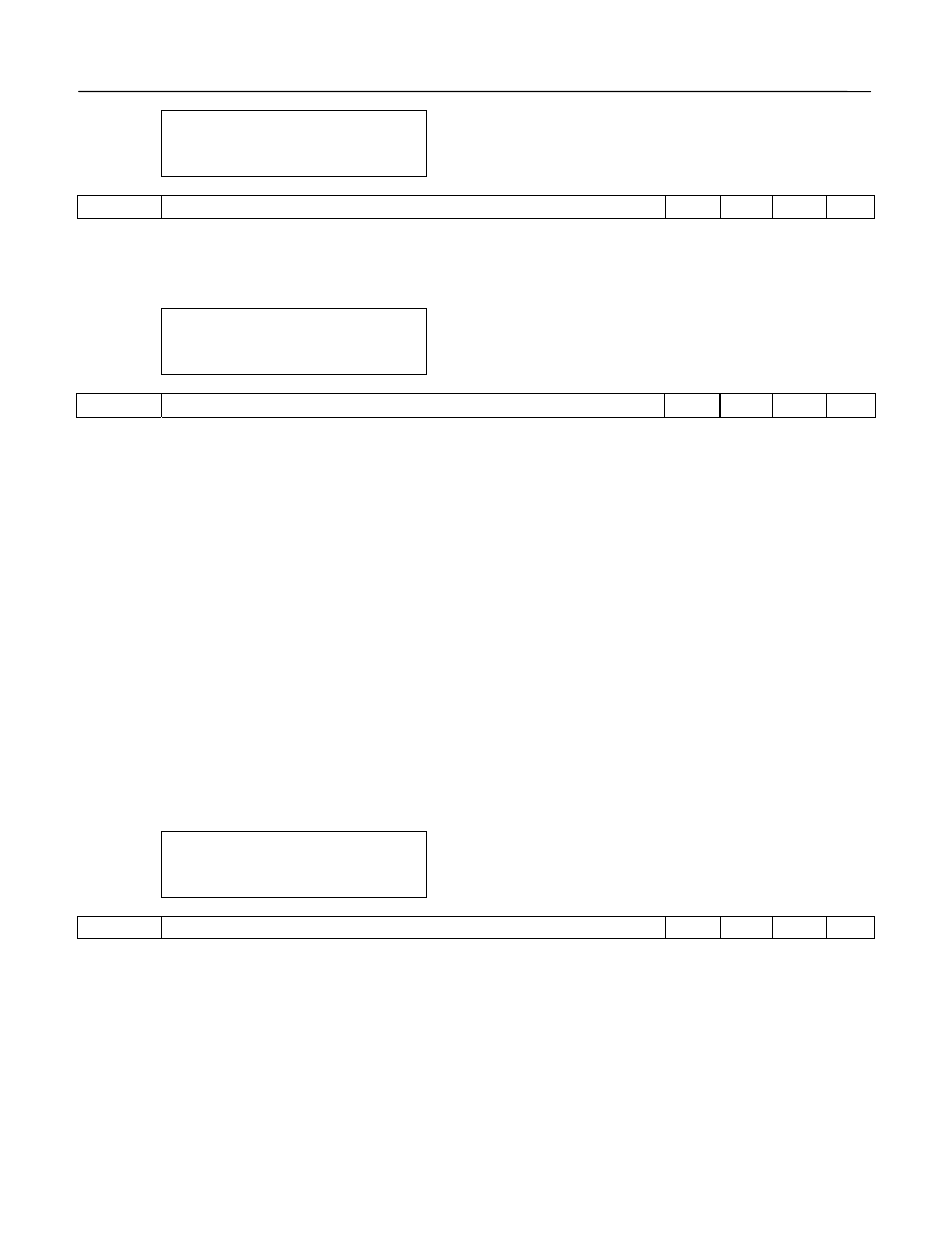
Electronic Lineshaft with Alignment
Date: 07-01-04, Rev: 04-07
Page 12 of 15
TM.G5SW.046
Ratio Numerator
P2-01=1000
P2-01 Ratio
Numerator
Q Q Q Q
The ratio numerator is multiplied by the encoder feedback from the master and then is divided by the ratio
denominator. This provides the ability to use a gear ratio between the master and the slave. See P2-02.
Ratio Demomin
P2-02=1000
P2-02 Ratio
Denominator
Q Q Q Q
The ratio denominator is divided into the product of the ratio numerator and the encoder feedback from the
master.
Example:
Slave Speed = (Master Encoder Feedback x P2-01) / P1-02
Feedback = 10 Hz , P1-01 = 1000, P2-02 = 250
Slave Speed = (10 Hz x 1000) / 250 or 40 Hz
Feedback = 10 Hz , P1-01 = 250, P2-02 = 1000
Slave Speed = (10 Hz x 250) / 1000 or 2.5 Hz
The position relationship between the master and the slave is maintained just as if a lineshaft went through a
gearbox with the same ratio. If the ratio is unknown it may be determined by counting the motor revolutions
required to make a complete machine cycle of both the master and slave. Convert the counts into a four digit
number by multiplying or dividing both by the same number. Set P1-01 to the slave count and set P1-02 to the
master count.
Example:
Master = 10 revs., Slave = 2.5 revs., Multiply both by 100
Master = 1000, Slave = 250
P1-01 = 250, P1-02 = 1000
P Limit
P2-04=2.000 HZ
P2-04 Proportional
Limit
Q Q Q Q
This parameter limits the proportional part of the position regulator.
Setting Range:
0.000 to 20.000
Factory Default:
2000
MODBUS Address:
0593H
Setting Range:
0 to 9999
Factory Default:
1000
MODBUS Address:
0591H
Setting Range:
0 to 9999
Factory Default:
1000
MODBUS Address:
0590H