Electronic lineshaft with alignment – Yaskawa G5 Electronic Lineshaft Alignment User Manual
Page 2
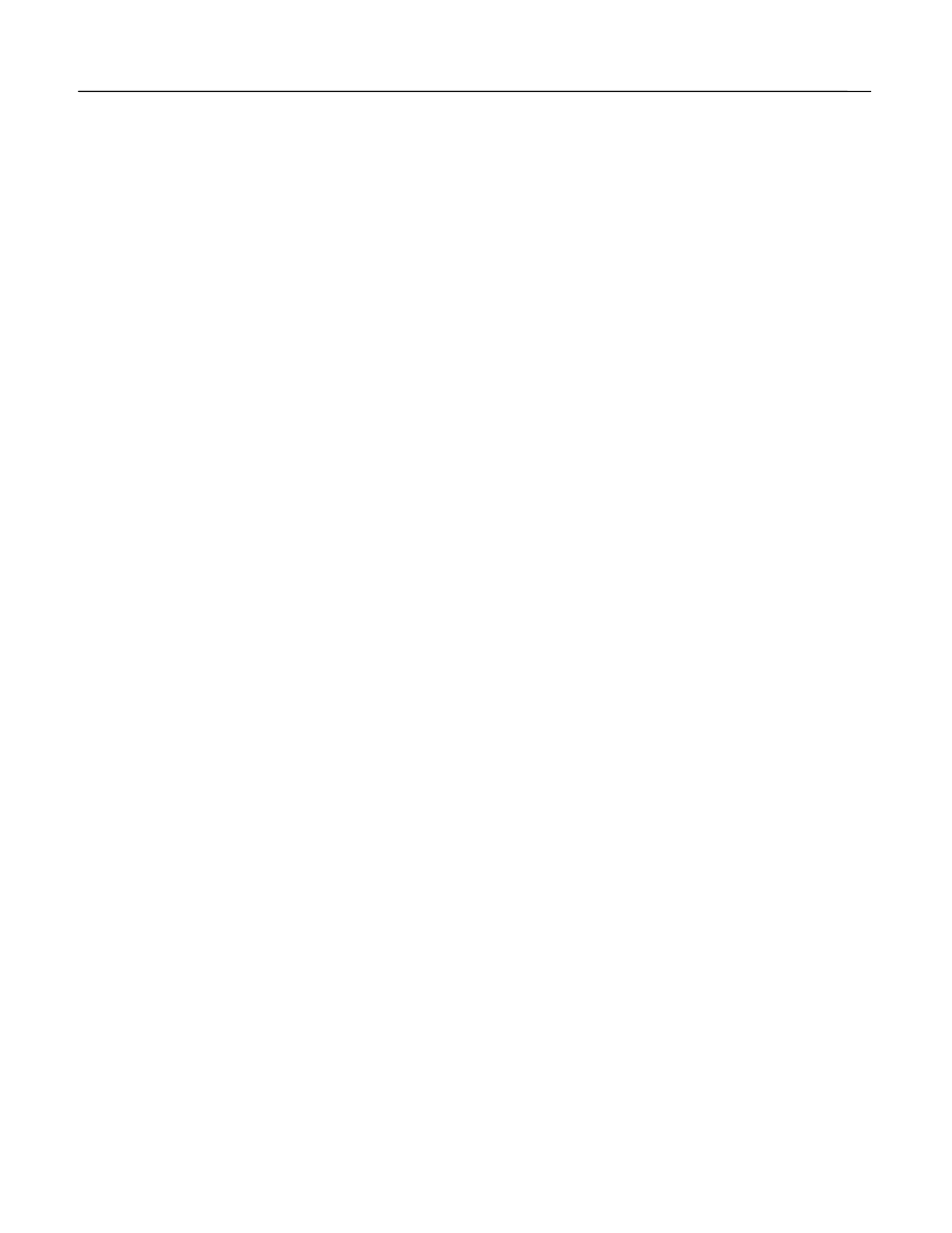
Electronic Lineshaft with Alignment
Date: 07-01-04, Rev: 04-07
Page 2 of 15
TM.G5SW.046
Features:
Disable Lineshaft Input – Disables the lineshaft software placing the drive back into standard control
Advance (Trim) Input – Advances the alignment position of the slave drive at a settable rate
Retard (Trim) Input
– Retards the alignment position of the slave drive at a settable rate
Slave Trigger Input
– Indicates the position of the slave drive when activated
Master Trigger Input
– Indicates the position of the master drive when activated
Align Slave Input
– Enables the automatic alignment feature
Aligned Output
– Indicates the alignment procedure was performed and the following drive did align
Alignment Checking
– Monitors the difference between the trigger inputs with the result controlling an output
Alignment Fault
– Monitors the travel during alignment and faults the drive when the limit is exceeded
Following Alarm
– Monitors the following error and provides a selectable result when it exceeds the limit
Gear Ratio
– Adjust the ratio of the following drive in respect to the master
Monitors
– Displays useful information to indicate how close the follower is following
The disable lineshaft input provides a means to operate the drive independent from the master drive. This feature
can be selected at any time and disables all lineshaft features when active. The position relationship between the
master and the slave drive will be lost when this input is activated. The slave drive will maintain the current
position with the master when the lineshaft disable input is deactivated.
The trim controls provide a means to adjust the position relationship between the master and the slave drives.
The trim rate is settable. The slave position can be advanced or retarded in relation to the master drive when the
slave’s run input is on. The trim can function if the run input is on.
The align slave, master and slave trigger inputs are required to perform an alignment. The alignment procedure
can be used to align the slave to the master using fixed trigger positions. This process does not control the
master drive. All correction is made by the slave drive. The amount of the correction is controlled by the
quadrature counts that are accumulated from the time when the first or leading trigger starts the process and
continues until the trailing trigger stops it. The correction will be made as soon as the trailing trigger input
becomes active. This process was intended to be performed at lower frequencies but will function if the triggers
provide a minimum of a 5 millisecond signal.
The alignment check is provided to indicate whether the trigger inputs are activated within a settable quadrature
count range. An alignment check output will be on when the triggers are within the defined range and will go off
when the range is exceeded. This output will only change after the trailing trigger has activated. This check is
always active in lineshaft mode.
The following alarm monitors the quadrature error count that exists between the master and the slave drive. If the
count exceeds the settable range a selectable action will occur.
The gear ratio provides a means to apply a ratio between the master device and the slave drive. This may be
used to correct for errors in drivetrain ratios or to apply a required ratio between the drives.
The monitors provided allow monitoring of how well the slave drive is following the master signal. The master
signal can also be monitored.