ProSoft Technology MVI71-MNET User Manual
Page 20
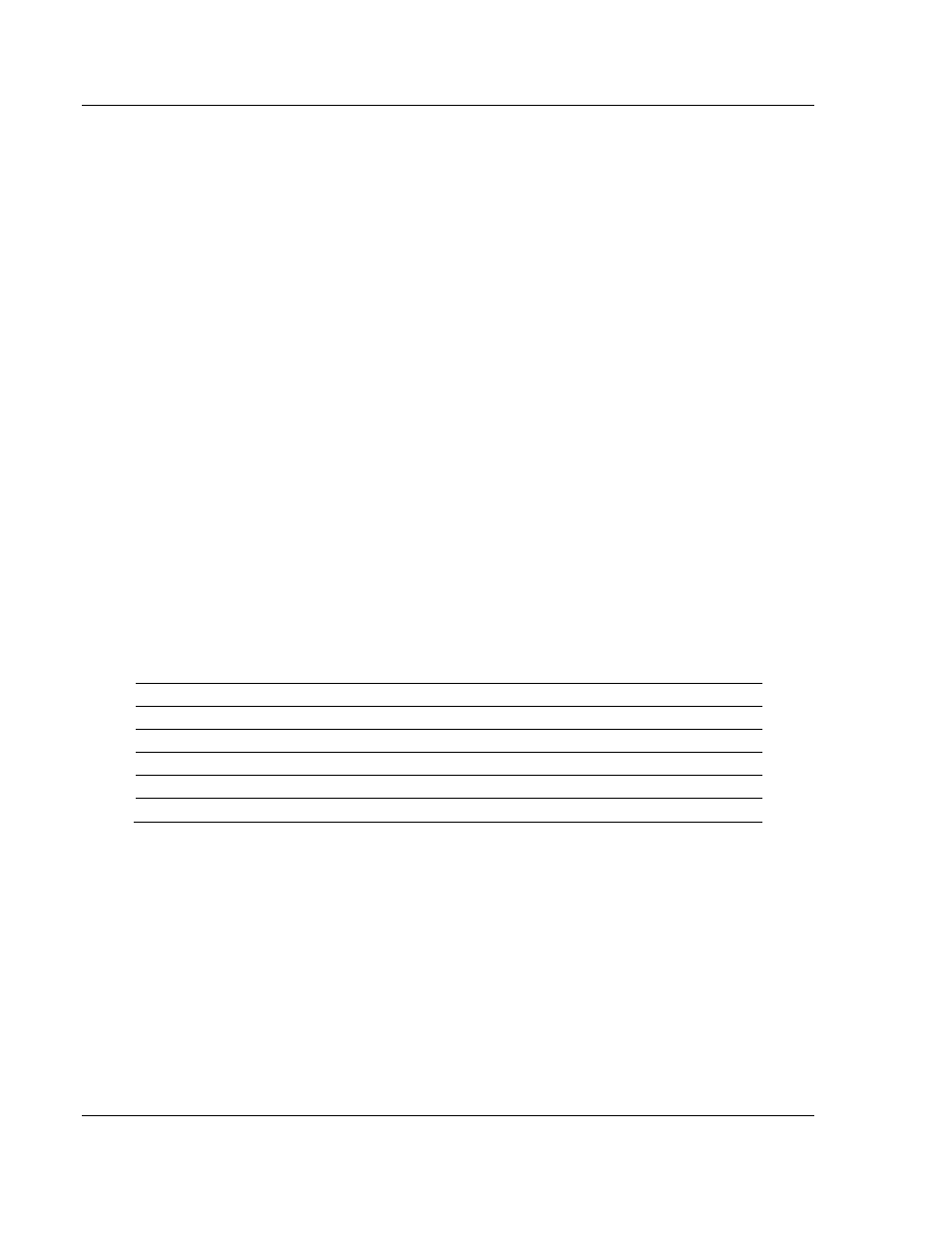
MVI71-MNET ♦ PLC Platform
Module Configuration
Modbus TCP/IP Interface Module
User Manual
Page 20 of 109
ProSoft Technology, Inc.
June 23, 2009
The next step in installing and configuring the module is to define whether the
block transfer or side-connect interface will be utilized. If the block transfer
interface is to be used you should be ready to connect the module to the Modbus
TCP/IP network if the ladder logic is defined correctly.
If the side-connect interface is utilized, make sure the file SC_DATA.TXT on the
Compact Flash Disk contains the correct first file number. You can run the
setdnpsc.exe program to set the file number to be used with your application.
Install the module in the rack and turn on the power. Connect the serial cable to
the module’s debug/configuration port and exit the program by pressing [E
SC
][X].
This will cause the program to exit and remain at the operating system prompt.
Run the setdnpsc.exe program with a command line argument of the file number
to use for the first file. For example, to select N10: as the first file, enter the
following:
SETDNPSC
10
The program will build the SC_DATA.TXT on the Compact Flash Disk (C: drive in
the root directory).
Next, define the data files to be used with the application. If the block transfer
interface is used, define the data files to hold the user data (read and write data).
Enter the ladder logic to handle the blocks transferred between the module and
the PLC. Download the program to the PLC and test the program with the
module.
If the side-connect interface is used, no ladder logic is required for data transfer.
The user data files to interface with the module must reside in contiguous order
in the processor. The first file to be used by the interface is the status/control file.
This is file number set in the SC_DATA.TXT file using the SETDNPSC.EXE
program. The following table lists the files used by the side-connect interface:
File Number
Example
Size
Description
Cfg File
N10
200
Control/Status File
Cfg File+1
N11
to 1000
Data transferred from the module to the processor
Other files for read data
Cfg File+1+n
N12
to 1000
Data transferred from the processor to the module
Cfg File+1+n+m
Other files for write data
n is the number of read data files minus one. Each file contains up to 1000
words.
m is the number of write data files minus one. Each file contains up to 1000
words.
More than one read and/or write file may exist in an application. This is required
when more than 1000 words of data are required. Two examples are given below
for the files used with different data set sizes: