Flowserve MARK 3 GROUP 4 User Manual
Page 12
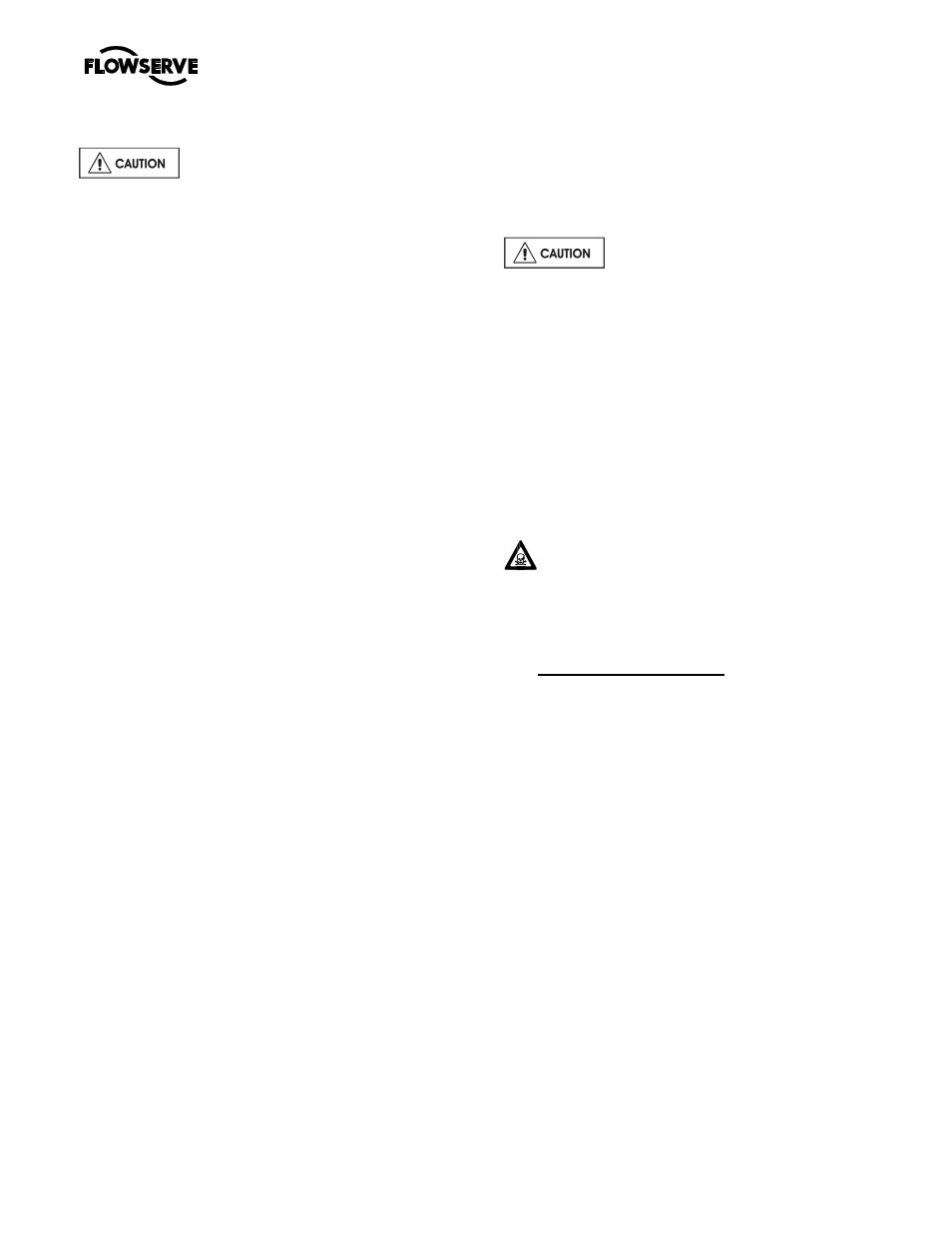
MARK 3 GROUP 4 USER INSTRUCTIONS ENGLISH 71569286 08-12
Page 12 of
48
flowserve.com
®
2.4 Storage
2.4.1
Short-Term Storage
When it is necessary to store a pump for a short time
before it can be installed, place it in a dry, cool
location. Protect it thoroughly from moisture and
condensation. Protective flange covers should not be
removed until the pump is being installed.
Wrap the exposed portions of the shaft and coupling
to protect against sand, grit or other foreign matter.
Oil lubricated units should be lubricated (refer to
Section III) to protect the bearings. Grease
lubricated units are lubricated at the factory during
assembly. Turn the rotor over by hand at least once
a week to maintain a protective film on the bearing
components.
2.4.2
LONG-TERM STORAGE
More than precautions are required if long-term
storage in excess of 90 days from factory shipment is
unavoidable.
The internal surfaces of the pump should be sprayed
with a rust preventative such as a water soluble oil or
other suitable alternative. Particular attention should
be given to the impeller, wear plate and stuffing box.
An optional method of protection is to suspend bags
of desiccant material inside casing and completely
seal all openings from the surrounding atmosphere.
The stuffing box should be packed with clean, dry
rags. Use of this method requires that the casing be
initially free of liquid. The desiccant material should
be checked at regular intervals to ensure that it has
not absorbed excessive water vapour. A warning
instruction, advising that the desiccant must be
removed prior to installation should be wired to the
pump.
A rust inhibitor should be added to the lubricating oil
of oil lubricated units to give additional protection
without destroying the lubricating properties of the oil.
For specific recommendations, consult your
lubrication dealer. Grease lubricated units, which
can be identified by the grease fitting at each bearing
location, should be well lubricated prior to placing in
storage. Small amounts of additional grease should
be added at regular intervals during storage. Refer
to Section III for additional information related to
grease lubrication.
Storage of pumps in areas of high ambient vibration
should be avoided to prevent bearing damage due to
brinelling. The risk of such damage can be reduced
by frequent rotation of the shaft.
The pump half coupling and key should be removed
from the shaft, coated with rust preventative and
wrapped to prevent metal-to-metal contact. Exposed
surfaces of the pump shaft should be protected with
a rust preventative. All dismantled parts should be
wrapped and tagged according to pump serial
number and a record kept of their location.
Pumps covered with plastic
should not be stored in a cool environment
because resulting condensation can cause
rusting
.
2.5 Recycling and end of product life
At the end of the service life of the product or its
parts, the relevant materials and parts should be
recycled or disposed of using an environmentally
acceptable method and in accordance with local
regulations. If the product contains substances that
are harmful to the environment, these should be
removed and disposed of in accordance with current
local regulations. This also includes the liquids
and/or gases that may be used in the "seal system"
or other utilities.
Make sure that hazardous substances are
disposed of safely and that the correct personal
protective equipment is used. The safety
specifications must be in accordance with the current
local regulations at all times.
3
PUMP DESCRIPTION
3.1 Configurations
Flowserve "MARK 3" pumps are single stage, end
suction centrifugal pumps specifically designed for
the chemical process industry and consequently are
ideally suited to many process fluids. A volute type
casing with integrally cast feet and top centerline
discharge nozzle is standard. The semi-open
impeller with rear pump-out vanes is designed for
high efficiency and prevents clogging. Sealing is
provided at the impeller to shaft fit to prevent
corrosion and thereby facilitate impeller removal.
The thrust bearing housing uses a threaded
adjustment that will permits precision bearing
alignment and impeller setting. The back pull-out
feature, typical of all MARK 3 pumps, permits quick
removal of the entire rotor/frame assembly without
disturbing the casing or driver.
The pump is sealed using non-asbestos packing in
the stuffing box, various mechanical seal designs as
specified by the customer may be installed at the
factory or retrofitted in the field.
All pumps are carefully inspected and prepared for
shipment. All exterior machined surfaces are coated