Flowserve MARK 3 GROUP 4 User Manual
Page 25
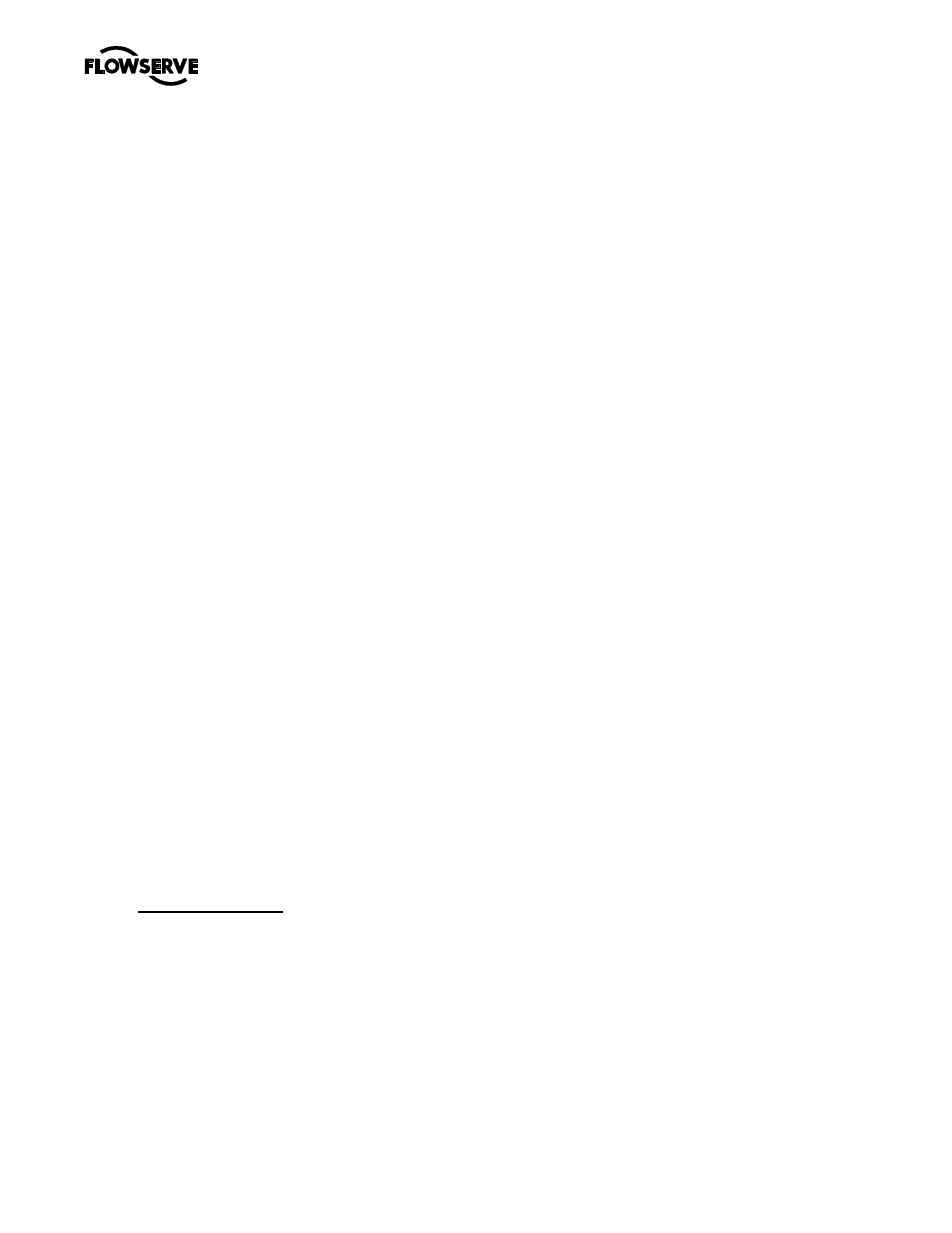
MARK 3 GROUP 4 USER INSTRUCTIONS ENGLISH 71569286 08-12
Page 25 of
48
flowserve.com
®
f) Inlet strainers, when used, should have a net
`free area' of at least three times the inlet pipe
area.
g) Do not install elbows at an angle other than
perpendicular to the shaft axis. Elbows parallel
to the shaft axis will cause uneven flow.
h) Except in unusual circumstances strainers are
not recommended in inlet piping. If considerable
foreign matter is expected a screen installed at
the entrance to the wet well is preferable.
i) Fitting an isolation valve will allow easier
maintenance.
j) Never throttle pump on suction side and never
place a valve directly on the pump inlet nozzle.
4.7.4
Discharge piping
A non-return valve should be located in the discharge
pipework to protect the pump from excessive back
pressure and hence reverse rotation when the unit is
stopped.
Pipework reducers should have a maximum total
angle of divergence of 15 degrees. Fitting an
isolation valve will allow easier maintenance.
4.7.5
Auxiliary piping
4.7.5.1 Drains
Pipe pump casing drains and gland leakage to a
convenient disposal point.
4.7.5.2 Pumps fitted with gland packing
It is required that a clean water flush be provided to
the packing to provide lubrication and to prevent the
ingress of air. When the product is clean and free of
solids this can be achieved with a supply from the
pump discharge volute to the stuffing box (Plan 11).
A control valve or orifice may be fitted in the line to
enable the pressure to the gland to be controlled.
If the pumped liquid is dirty and cannot be used for
sealing, a separate clean compatible liquid supply to
the gland at a pressure equal to the estimated
stuffing box pressure, Ps (psig).
TDH = total developed head at shut valve (feet)
S.G. = Specific Gravity of pump liquid
Suction Pressure = maximum suction pressure
corrected for specific gravity (psig).
4.7.5.3 Pumps fitted with mechanical seals
Single seals requiring re-circulation will normally be
provided with the auxiliary piping from pump casing
already fitted.
If the seal requires an auxiliary quench then a
connection must be made to a suitable source of
liquid flow, low pressure steam or static pressure
from a header tank. Recommended pressure is 0.35
bar (5 psi) or less. Check
General arrangement
drawing
.
Special seals may require different auxiliary piping to
that described above. Consult separate User
Instructions and/or Flowserve if unsure of correct
method or arrangement.
For pumping hot liquids, to avoid seal damage, it is
recommended that any external flush/cooling supply
be continued after stopping the pump.
4.7.6
Final checks
Check the tightness of all bolts in the suction and
discharge pipework. Check also the tightness of all
foundation bolts.
4.8 Final shaft alignment check
After connecting piping to the pump, rotate the shaft
several times by hand to ensure there is no binding
and all parts are free.
The baseplate should be levelled and grouted by this
stage.
Recheck the coupling alignment, as previously
described, to ensure no pipe strain. If pipe strain
exists, correct piping.
a) Mount and level pump if appropriate. Level the
pump by putting a level on the discharge flange.
It may be necessary to adjust the bearing frame
foot by adding or deleting shims [3126.1]
between the foot piece and the bearing housing
(or baseplate).
b) Check initial alignment. If pump and driver have
been remounted or the specifications given
below are not met, perform an initial alignment as
described in section 4.5. This ensures there will
be sufficient clearance between the motor hold
down bolts and motor foot holes to move the
motor into final alignment. The pump and driver
should be within 0.38 mm (0.015 in.) FIM (full
indicator movement) parallel, and 2.5 mm/m
(0.0025 in./in.) FIM angular.
c) Run piping to the suction and discharge to the
pump. There should be no piping loads
transmitted to the pump after connection is
made. Recheck the alignment to verify that there
are no significant changes.
Ps =
+ Suction Pressure
0.6 x TDH X S.G.
2.31