Flowserve MARK 3 GROUP 4 User Manual
Page 19
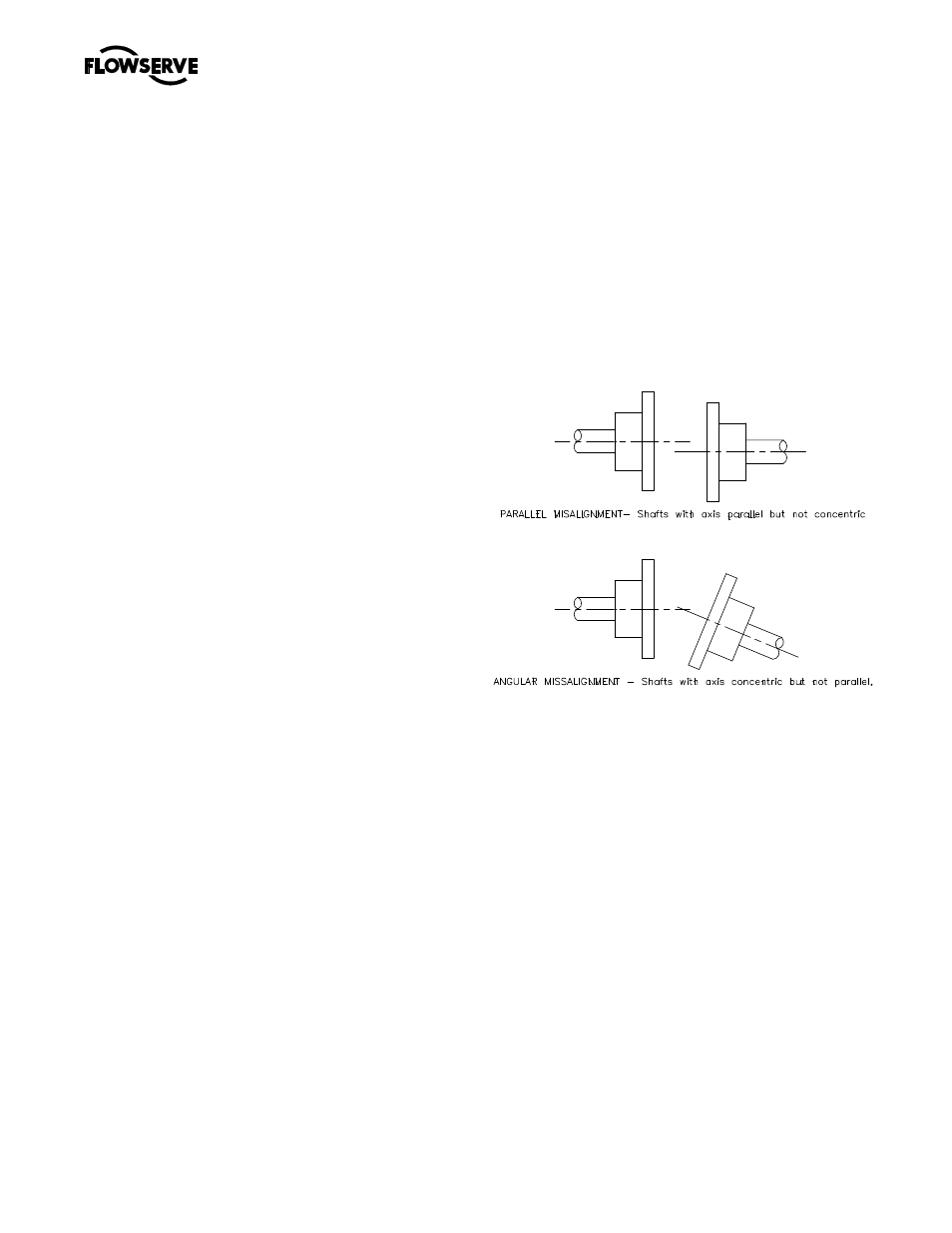
MARK 3 GROUP 4 USER INSTRUCTIONS ENGLISH 71569286 08-12
Page 19 of
48
flowserve.com
®
jackscrews are not provided, shims and wedges
should be used. (See Figure 4-5.) Check for
levelness in both the longitudinal and lateral
directions. Shims should be placed at all base
anchor bolt locations. Do not rely on the bottom
of the baseplate to be flat. Standard baseplate
bottoms are not machined and it is not likely that
the field mounting surface is flat.
c) After leveling the baseplate, tighten the anchor
bolts. If shims were used, make sure that the
baseplate was shimmed near each anchor bolt
before tightening. Failure to do this may result in
a twist of the baseplate, which could make it
impossible to obtain final alignment.
d) Check the level of the baseplate to make sure
that tightening the anchor bolts did not disturb
the level of the baseplate. If the anchor bolts did
change the level, adjust the jackscrews or shims
as needed to level the baseplate.
e) Continue adjusting the jackscrews or shims and
tightening the anchor bolts until the baseplate is
level.
f) Check initial alignment. If the pump and motor
were removed from the baseplate proceed with
step g) first, then the pump and motor should be
reinstalled onto the baseplate using Flowserve’s
factory preliminary alignment procedure as
described in section 4.5, and then continue with
the following. As described above, pumps are
given a preliminary alignment at the factory. This
preliminary alignment is done in a way that
ensures that, if the installer duplicates the factory
conditions, there will be sufficient clearance
between the motor hold down bolts and motor
foot holes to move the motor into final alignment.
If the pump and motor were properly reinstalled
to the baseplate or if they were not removed from
the baseplate and there has been no transit
damage, and also if the above steps where done
properly, the pump and driver should be within
0.38 mm (0.015 in.) FIM (Full Indicator
Movement) parallel, and 2.5 mm/m
(0.0025 in./in.) FIM angular. If this is not the
case, first check to see if the driver mounting
fasteners are centered in the driver feet holes. If
not, re-center the fasteners and perform a
preliminary alignment to the above tolerances by
shimming under the motor for vertical alignment,
and by moving the pump for horizontal
alignment.
g) Grout the baseplate. A non-shrinking grout
should be used. Make sure that the grout fills the
area under the baseplate. After the grout has
cured, check for voids and repair them.
Jackscrews, shims and wedges should be
removed from under the baseplate at this time. If
they were to be left in place, they could rust,
swell, and cause distortion in the baseplate.
h) Run piping to the suction and discharge of the
pump. There should be no piping loads
transmitted to the pump after connection is
made. Recheck the alignment to verify that there
are no significant loads.
Check the impeller axial clearance and that the rotor
turns freely by hand.
Note: Grout is not poured until an initial
alignment of the pump and driver has been
performed. See section 4.5
4.5 Initial alignment
The purpose of factory alignment is to ensure that the
user will have sufficient clearance in the motor holes
for final job-site alignment. To achieve this, the
factory has designed the mounting holes with
additional clearance to allow the pump to be aligned
in the horizontal plane to the motor, There should be
at least 1/16 clearance around the bolt. The coupling
has been designed to have some overhang of the
coupling hub (in most cases 1 or both hubs may be
overhung between 0.0 and 3 mm (0 and 0.12 in)
unless otherwise stated. This procedure ensures that
there is sufficient clearance in the motor holes for the
customer to field align the motor to the pump, to zero
tolerance. This philosophy requires that the customer
be able to place the base in the same condition as
the factory. Thus the factory alignment will be done
with the base sitting in an unrestrained condition on a
flat and level surface. This standard also emphasizes
the need to ensure the shaft spacing is adequate to
accept the specified coupling spacer.