8 stopping and shutdown – Flowserve MARK 3 GROUP 4 User Manual
Page 30
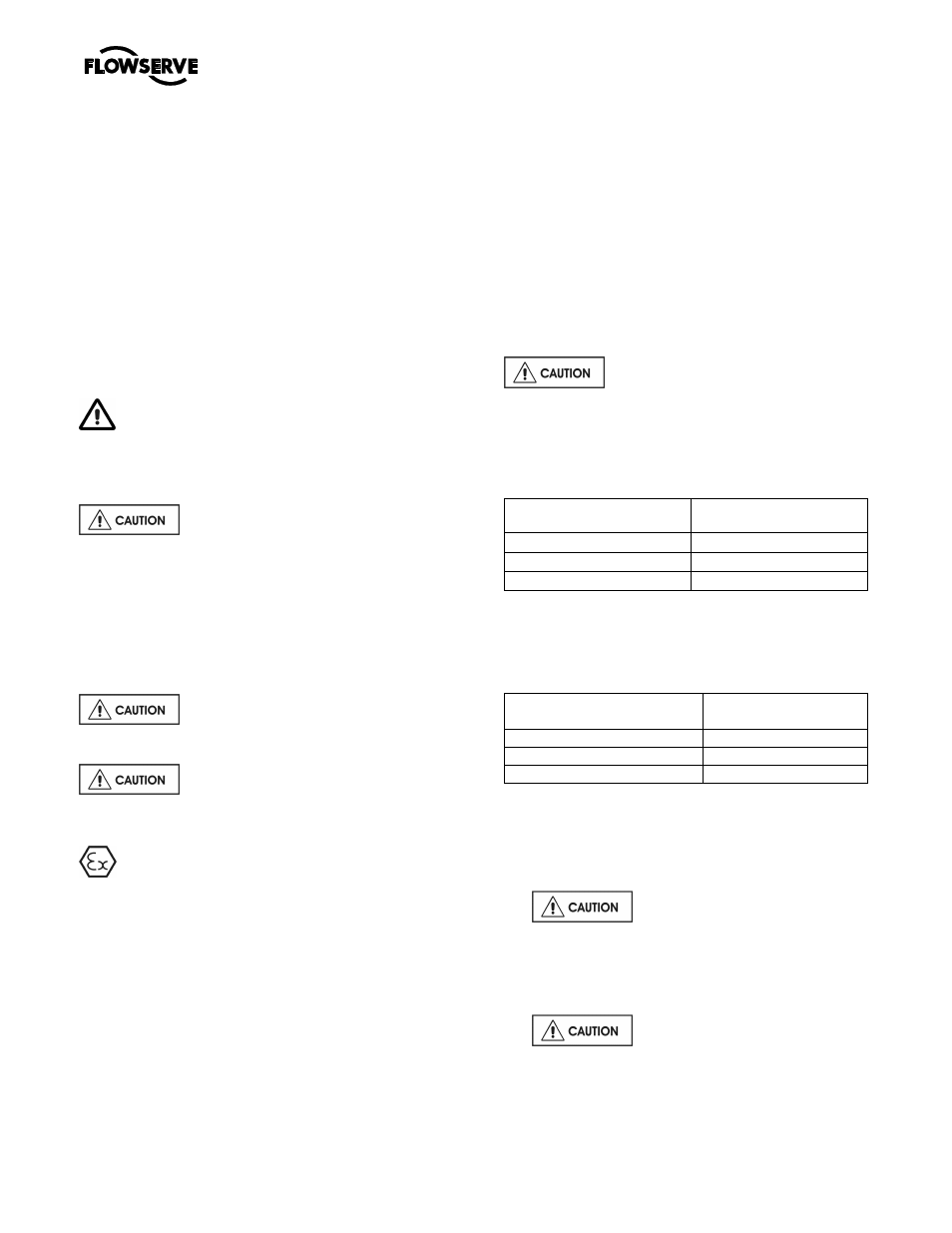
MARK 3 GROUP 4 USER INSTRUCTIONS ENGLISH 71569286 08-12
Page 30 of
48
flowserve.com
®
leakage takes place the packing will begin to
overheat. If overheating takes place the pump
should be stopped and allowed to cool before being
re-started. Loosen the gland when the pump is re-
started; check to ensure leakage is taking place at
the packed gland.
If hot liquids are being pumped it may be necessary
to slacken the gland nuts to achieve leakage.
The pump should be run for 30 minutes with steady
leakage and the gland nuts tightened by 10 degrees
at a time until leakage is reduced to an acceptable
level, normally a minimum of 120 drops per minute is
required. Bedding in of the packing may take
another 30 minutes.
Care must be taken when adjusting the gland
on an operating pump. Safety gloves are essential.
Loose clothing must not be worn to avoid being
caught up by the pump shaft. Shaft guards must be
replaced after the gland adjustment is complete.
Never run gland packing dry, even for
a short time.
5.7.3
Pumps fitted with mechanical seal
Mechanical seals require no adjustment. Any slight
initial leakage will stop when the seal is run in.
Before pumping dirty liquids it is advisable, if
possible, to run in the pump mechanical seal using
clean liquid to safeguard the seal face.
External flush or quench should be
started before the pump is run and allowed to flow for
a period after the pump has stopped.
Never run a mechanical seal dry,
even for a short time.
5.7.4
Bearings
If the pumps are working in a potentially
explosive atmosphere temperature or vibration
monitoring at the bearings is recommended.
If bearing temperatures are to be monitored it is
essential that a benchmark temperature is recorded
at the commissioning stage and after the bearing
temperature has stabilized. Record the bearing
temperature (t) and the ambient temperature (ta).
Estimate the likely maximum ambient temperature
(tb). Set the alarm at (t+tb-ta+5)
°
C [(t+tb-ta+10)
°
F]
and the trip at 100
°
C (212
°
F) for oil lubrication and
105
°
C (220
°
F) for grease lubrication.
It is important, particularly with grease lubrication, to
keep a check on bearing temperatures. After start up
the temperature rise should be gradual, reaching a
maximum after approximately 1.5 to 2 hours. This
temperature rise should then remain constant or
marginally reduce with time. Refer to section 6.2.3.1
for further information.
5.7.5
Normal vibration levels, alarm and trip
For guidance, pumps generally fall under a
classification for rigid support machines within the
International rotating machinery standards and the
recommended maximum levels below are based on
those standards.
Alarm and trip values for installed
pumps should be based on the actual measurements
(N) taken on the pump in the fully commissioned as
new condition. Measuring vibration at regular
intervals will then show any deterioration in pump or
system operating conditions.
Vibration velocity –
unfiltered
mm/s (in./s) r.m.s.
MARK 3
Normal
N
≤
5.6 (0.22)
Alarm
N
x 1.25
≤
7.1 (0.28)
Shutdown trip
N
x 2.0
≤
11.2 (0.44)
5.7.6
Stop/start frequency
Pump sets are normally suitable for the number of
equally spaced stop/starts per hour shown in the
table below. Check actual capability of the driver and
control/starting system before commissioning.
Motor rating kW (hp)
Maximum stop/starts
per hour
Up to 15 (20)
15
Between 15 (20) and 90 (120)
10
Above 90 (120)
6
Where duty and standby pumps are installed it is
recommended that they are run alternately every
week.
5.8 Stopping and shutdown
a)
Close the outlet valve, but ensure
that the pump runs in this condition for no more
than a few seconds.
b) Stop the pump.
c) Switch off flushing and/or cooling/heating liquid
supplies at a time appropriate to the process.
d)
For prolonged shut-downs and
especially when ambient temperatures are likely
to drop below freezing point, the pump and any
cooling and flushing arrangements must be
drained or otherwise protected.