Flowserve MARK 3 GROUP 4 User Manual
Page 27
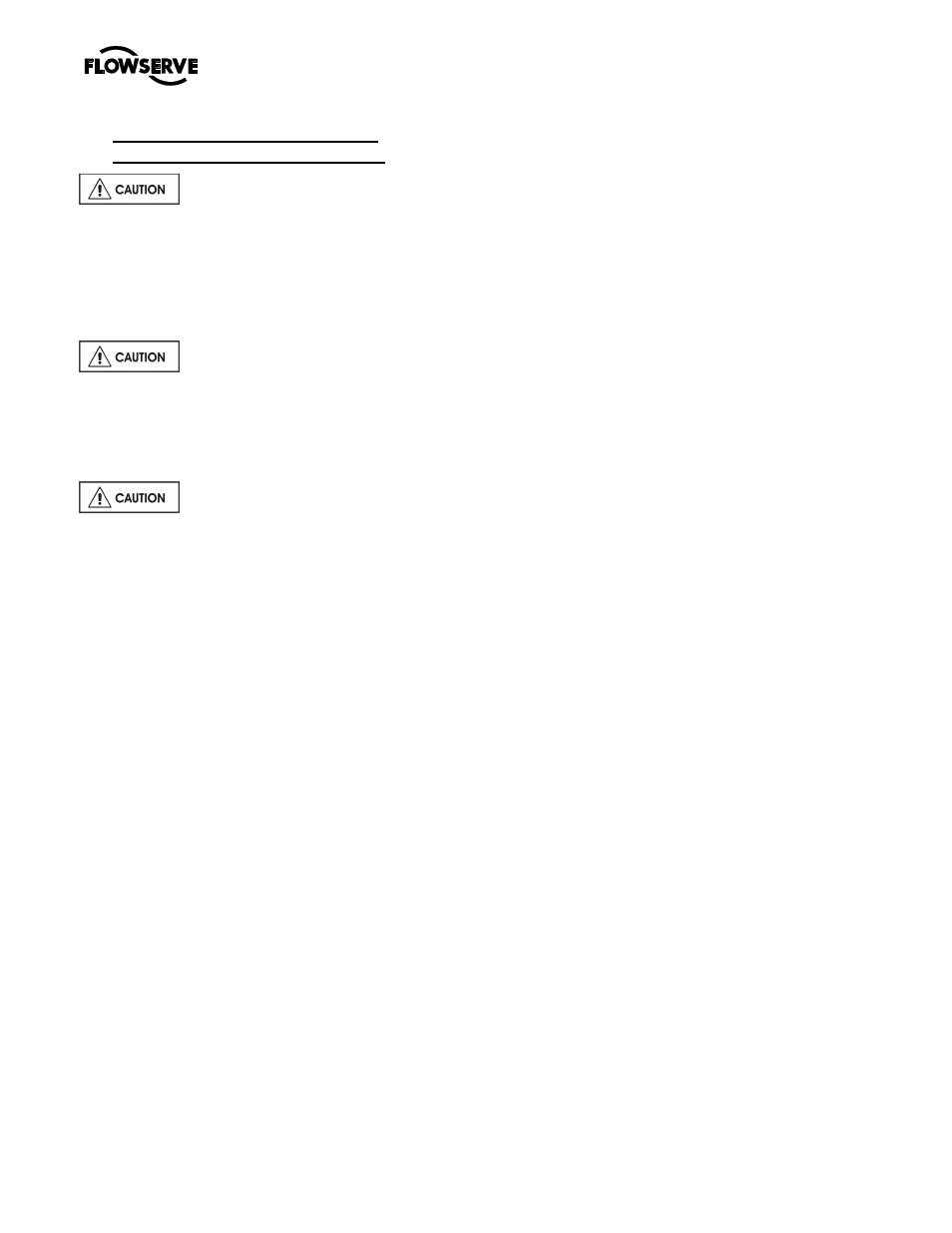
MARK 3 GROUP 4 USER INSTRUCTIONS ENGLISH 71569286 08-12
Page 27 of
48
flowserve.com
®
5
COMMISSIONING, START-UP,
OPERATION AND SHUTDOWN
These operations must be carried
out by fully qualified personnel.
5.1 Pre-commissioning procedure
5.1.1
Lubrication Methods
Determine the mode of lubrication of the pump set,
eg grease, oil, product lubrication etc.
For oil lubricated pumps, fill the
bearing housing with correct grade of oil to the
correct level, ie sight glass or constant level oiler
bottle.
Other drivers and gearboxes, if appropriate, should
be lubricated in accordance with their manuals.
In the case of product lubricated
bearings the source of product supply should be
checked against the order. There may be
requirements for an external clean supply, particular
supply pressure or the commencement of lubrication
supply before pump start-up.
5.1.2
Oil Bath Lubrication
When fitted with a constant level oiler, the bearing
housing should be filled by unscrewing or hinging
back the transparent bottle and filling the bottle with
oil. Where an adjustable body Trico oiler is fitted this
should be set to the proper height.
The oil filled bottle should then be refitted so as to
return it to the upright position. Filling should be
repeated until oil remains visible within the bottle.
Approximate oil volumes are shown in section 5.2.3,
Pump and impeller data
.
5.1.3
Grease Lubrication
Grease lubricated pumps and electric motors are
supplied pre-greased.
5.1.4
Oil Mist Lubrication
Mk3 Group 4 pumps may be lubricated by pure or
purge oil mist. See comments below.
5.1.4.1 Purge Mist
In the case of purge mist an oil level is maintained in
the bearing frame. No changes are required to be
made to the pump, however, the oil level must be
maintained at site glass center. Excess oil must be
removed. Oil is injected outboard of each bearing.
5.1.4.2 Pure Oil Mist
In this method all oil is drained from the oil sump, this
is sometimes referred to as a dry sump. Oil is
injected outboard at each bearing. To use this
method some modifications must be made to the
pump. If pumps are shipped for standard oil or
grease lubrication the pumps must be dismantled
and reworked. All oil return grooves that permit
movement of oil from outboard of each bearing back
to the sump shall be blocked. These passages may
be blocked using epoxy filler or other compounds
compatible with the mist oil. Pressure inside the
center of the bearing frame must be controlled,
recommended pressure to be 25mm - 50mm (1”-2”)
H
2
O. Excessive will cause fogging and venting of oil
through the bearing seals. High inboard pressures
could result in poor mist distribution and could result
in bearing failure as mist is not forced through the
bearing. It is recommended that mist system operate
for 24 hrs before starting of the pump to ensure
bearing surfaces have been properly misted. Testing
completed has used an oil viscosity of 100 cSt. For
additional information refer to TR-3326, Pure Oil Mist
lubrication of FRBH and R/M Slurry Pumps. Contact
Flowserve engineering for copy or additional
information such as reclassifier sizing.