Flowserve StarPac II Control Valves User Manual
Page 20
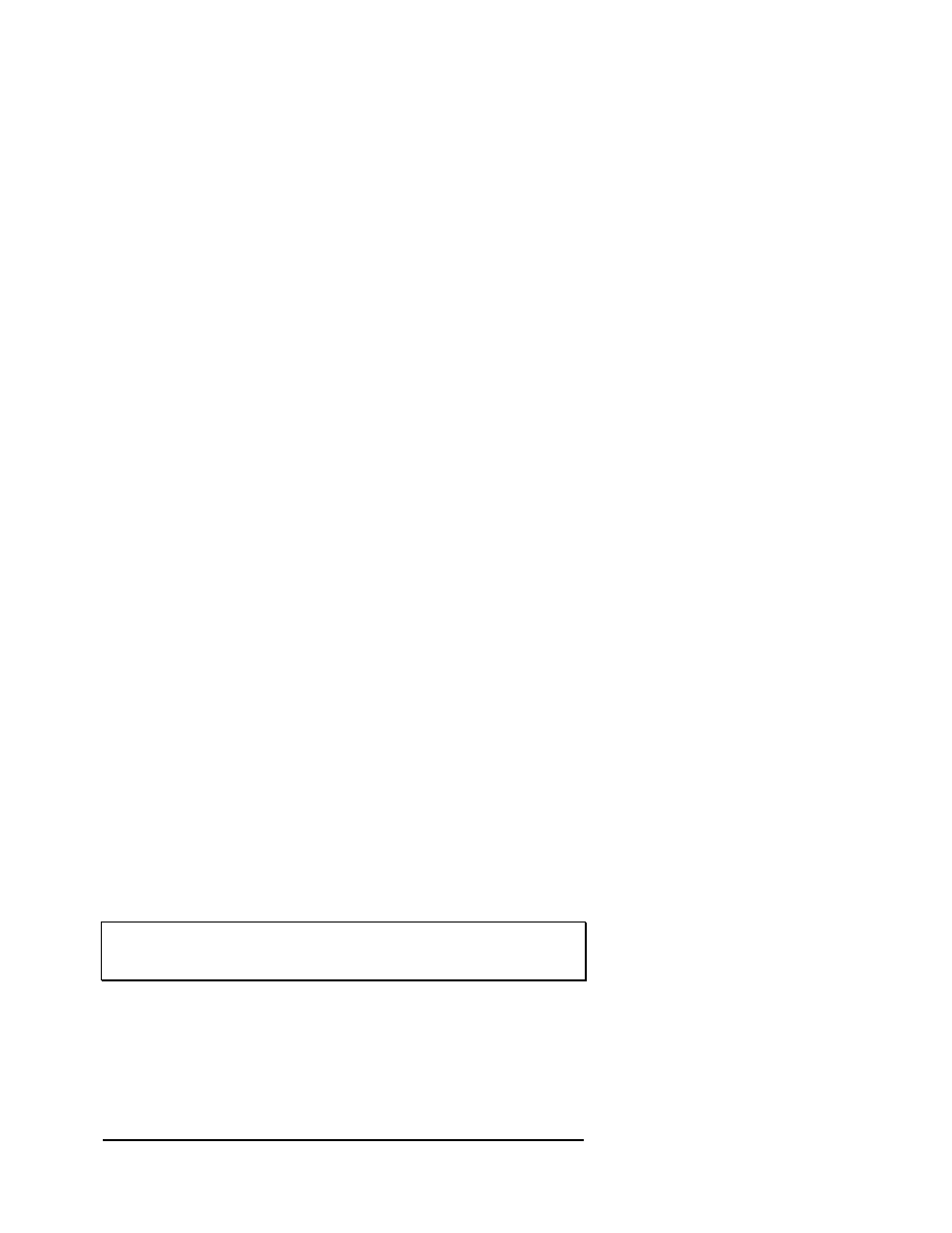
source should be connected to terminals 24(-) and 25(+) of the
terminal block. The display will give instructions to adjust the signal
until the reference meter reads 4 mA. When the 4 mA value has
been accepted, the user is then prompted to set the 20 mA value. If
the CANCEL key is pressed at any time, all of the calibration values
are returned to their original value. The number shown at the end of
the second line indicates the raw A/D value that the unit is receiving
and is only for reference during calibration. Configuration of the
variable and scaling for the channel is done in the T
UNE
menu.
Analog In No. 2 - This option is used to calibrate the second analog
input of the StarPac II system. During the calibration, a reference
milliamp source should be connected to terminals 22(-) and 23(+) of
the terminal block. The display will give instructions to adjust the
signal until the reference meter reads 4 mA. When the 4 mA value
has been accepted, you are then prompted to set the 20 mA value.
If the CANCEL key is pressed at any time, all of the calibration
values are returned to their original value. The number shown at the
end of the second line indicates the raw A/D value that the unit is
receiving and is only for reference during calibration. Configuration
of the variable and scaling for the channel is done in the C
ONFIGURE
menu.
Actuator - This option calibrates the actuator pressure sensors in
the unit. The process requires that the valve stroke from full open to
full closed. Because the valve will change position during this
process you must confirm that you want to proceed. You will then be
prompted for the instrument air supply pressure to the unit. If the air
supply varies by more than 1 psi during the calibration, the test may
abort. Hence, a regulator may be required if the air supply is not
stable. The unit will then complete the calibration process by
stroking the valve open and closed over 30 to 60 seconds. Upon
successful completion, the display will momentarily flash the
message “Calibration Successful”.
Stroke - This option calibrates the position feedback sensor in the
unit. The process requires that the valve stroke from full open to full
closed. Because the valve will change position during this process
you must confirm that you want to proceed. You will then be
prompted for the valve type; linear or rotary. If the air supply varies
by more than 1 psi during the calibration, the test may abort. Hence,
a regulator may be required if the air supply is not stable. The unit
will then complete the calibration process by stroking the valve open
and closed over one to five minutes. Upon successful completion of
the process, the system will momentarily flash the message
“Calibration Successful”.
WARNING: Notify personnel working nearby that the valve will
stoke during this procedure; otherwise, serious injury may
occur.
P1 and P2 - This option simultaneously calibrates the process
pressure sensors in the unit and is the recommended sensor
calibration method. Because it calibrates both sensors at the same
time, this procedure automatically moves the valve’s stroke to mid-
stroke. This calibration should always be done with the flow through
the valve blocked. If there is flow through the valve you must use
StarPac II User Interface Manual
14