Acme or other special threads, Carbide-tipped cutters and cutter forms – Smithy Midas 1220 XL User Manual
Page 46
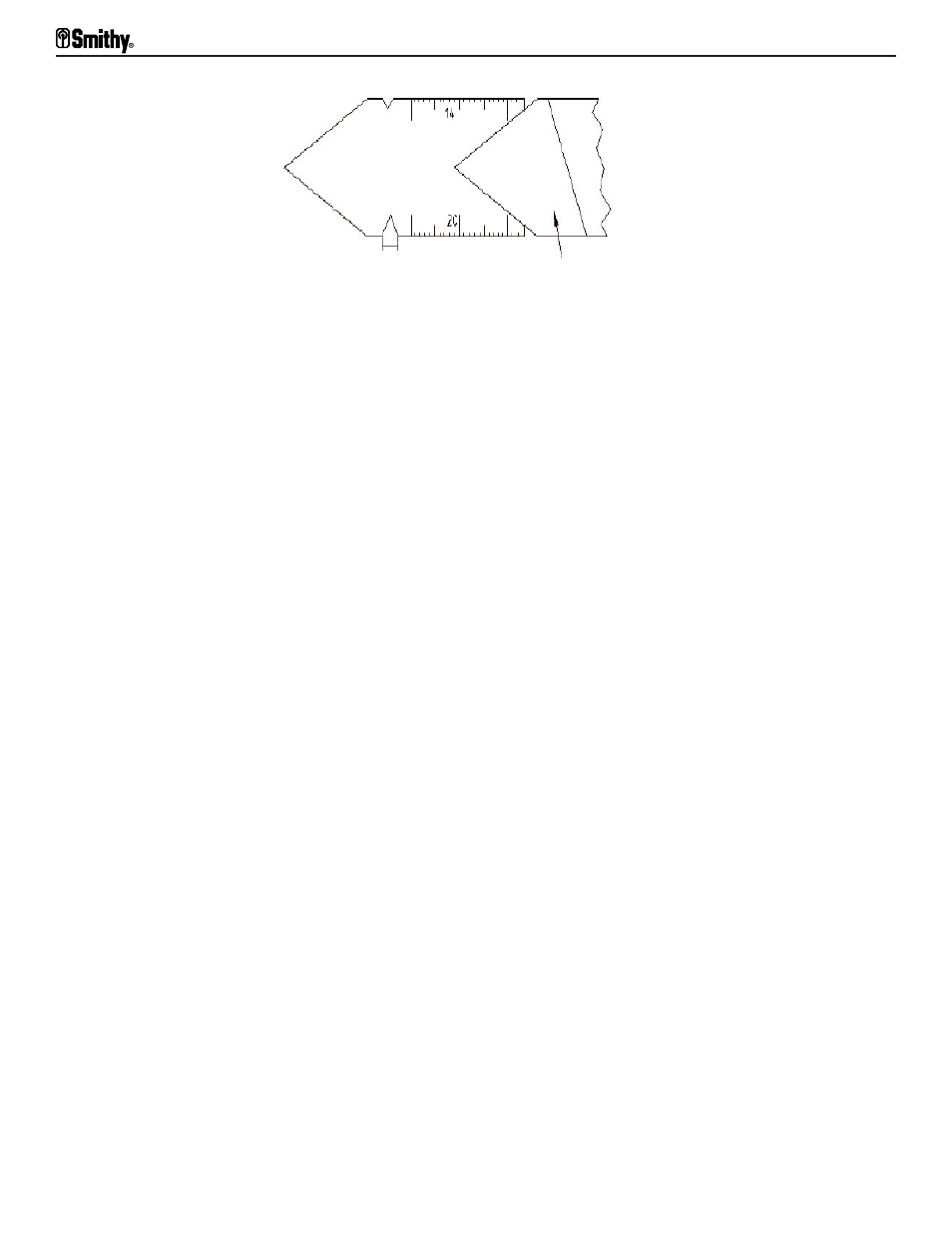
Figure 9.8 Insert the point into the nearest seized V in the center gauge.
Acme or Other Special Threads
Thread gauges are available for all standard threads. Before grinding such cutters,
ascertain the correct pitch angle of the particular thread profile. For example, the pitch
of an acme thread is 29° to a side, and the toolpoint is ground back square to an exact
thread profile that requires a different end width for each thread size.
Thread forms must be accurate if threads are to fit snugly and smoothly. Every
resharpening of this type of cutter requires regrinding the entire form. It is far better,
when doing any amount of threading, to use a threading tool with a special form cutter.
Sharpening such cutters requires only flat, top grinding, which does not alter the cutting
profile.
Carbide-Tipped Cutters and Cutter Forms
Carbide is a compound of carbon and a metal. In cutting tools, it is usually carbon and
tungsten. The hardness of carbide cutting materials approaches that of diamond. While
carbides permit easy machining of chilled cast iron, hard and tough steels, hard rubber,
Bakelite, glass, and other difficult or "unmachinable" materials, its primary use in
industry is for long production runs on ordinary steels. On such work, carbide-tipped tools
permit higher running speeds and much longer runs between resharpenings. The cutting
edge of carbide tools stands up 10 to 200 times as long as the edge of HSS tools (Table
9.1).
The advantage of carbide is that it tolerates much higher heat than HSS or other alloys
so you can run at higher speeds. The disadvantage is that it is more brittle than HSS and
must have adequate support in the toolpost to prevent vibration and breakage.
9-5
For Assistance: Call Toll Free 1-800-476-4849
Midas 1220 XL Operator’s Manual