Flowserve TB-MAG INNOMAG User Manual
Page 8
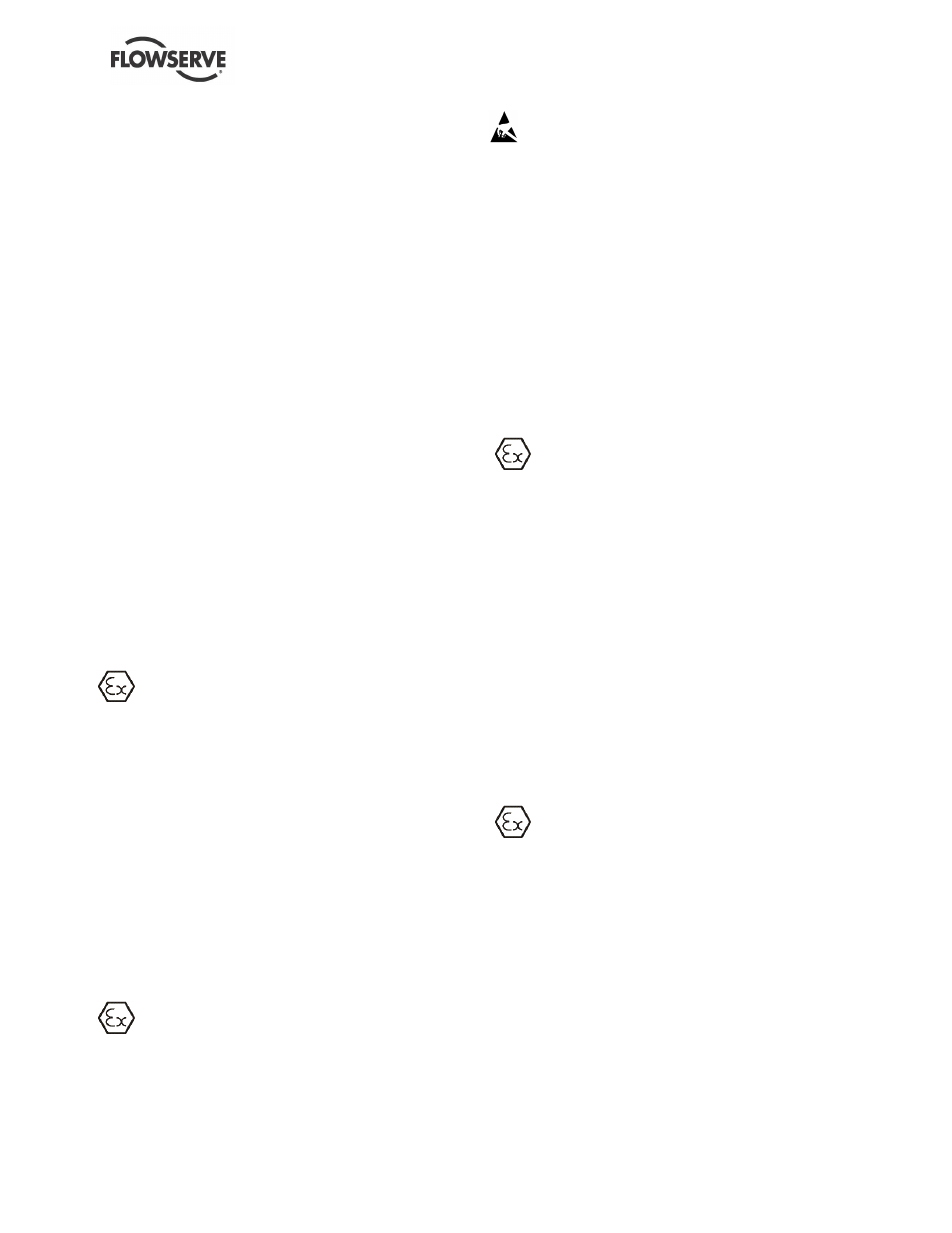
INNOMAG® TB-
MAG™ ASME and ISO SEALLESS ENGLISH 26999988 06-14
Page 8 of 44
The temperature rise at the bearings and due to the
minimum permitted flow rate is taken into account in
the temperatures stated.
The operator is responsible to ensure that the
specified maximum liquid temperature is not
exceeded.
Temperature classification “Tx” is used when the liquid
temperature varies and when the pump is required to be
used in differently classified potentially explosive
atmospheres. In this case the user is responsible for
ensuring that the pump surface temperature does not
exceed that permitted in its actual installed location.
Avoid mechanical, hydraulic or electrical overload by
using motor overload trips, temperature monitors
and/or a power monitor and make routine vibration
monitoring checks.
In dirty or dusty environments, make regular checks
and remove dirt from areas around close clearances,
bearing housings and motors.
Where there is any risk of the pump being run against a
closed valve generating high liquid and casing external
surface temperatures fit an external surface
temperature protection device.
1.6.4.4 Preventing the build-up of explosive
mixtures
ENSURE THE PUMP IS PROPERLY FILLED
AND DOES NOT RUN DRY
Ensure the pump and relevant suction and discharge
pipeline system is totally filled with liquid at all times
during the pump operation, so that an explosive
atmosphere is prevented.
If the operation of the system cannot avoid this
condition, fit an appropriate dry run protection device
(for example liquid detection or a power monitor).
To avoid potential hazards from fugitive emissions of
vapor or gas to atmosphere the surrounding area
must be well ventilated.
1.6.4.5 Preventing sparks
To avoid the potential hazard from random
induced current generating a spark, the baseplate
must be properly grounded.
Avoid electrostatic charge: do not rub non-metallic
surfaces with a dry cloth
;
ensure cloth is damp.
Additional requirement for metallic pumps on
non-metallic baseplates
When metallic components are fitted on a non-
metallic baseplate they must be individually earthed.
If so equipped, to prevent a potential hazard from
mechanical contact, the coupling guard must be non-
sparking. For ATEX the coupling must be selected to
comply with European Directive 2014/34/EU
(previously 94/9/EC which remains valid until April
20
th
2016 during the transition). Correct coupling
alignment must be maintained.
1.6.4.6 Preventing leakage
The pump must only be used to handle liquids
for which it has been approved to have the correct
corrosion resistance.
Avoid entrapment of liquid in the pump and associated
piping due to closing of suction and discharge valves,
which could cause dangerous excessive pressures to
occur if there is heat input to the liquid. This can occur if
the pump is stationary or running.
Bursting of liquid containing parts due to freezing
must be avoided by draining or protecting the pump
and ancillary systems.
If leakage of liquid to atmosphere can result in a
hazard, install a liquid detection device or secondary
containment.
1.6.4.7 Maintenance to avoid the hazard
CORRECT MAINTENANCE IS REQUIRED
TO AVOID POTENTIAL HAZARDS WHICH GIVE A
RISK OF EXPLOSION
The responsibility for compliance with maintenance
instructions is with the plant operator.
To avoid potential explosion hazards during
maintenance, the tools, cleaning and painting
materials used must not give rise to sparking or
adversely affect the ambient conditions. Where there
is a risk from such tools or materials, maintenance
must be conducted in a safe area.
It is recommended that a maintenance plan and
schedule is adopted. (See section 6, Maintenance.)