1 pre-commissioning procedure, 2 pump lubricants, 3 impeller clearance – Flowserve PHL User Manual
Page 17: 4 direction of rotation, 5 guarding, 6 priming and auxiliary supplies, 7 warming-up instructions for hot pumps, 8 starting the pump
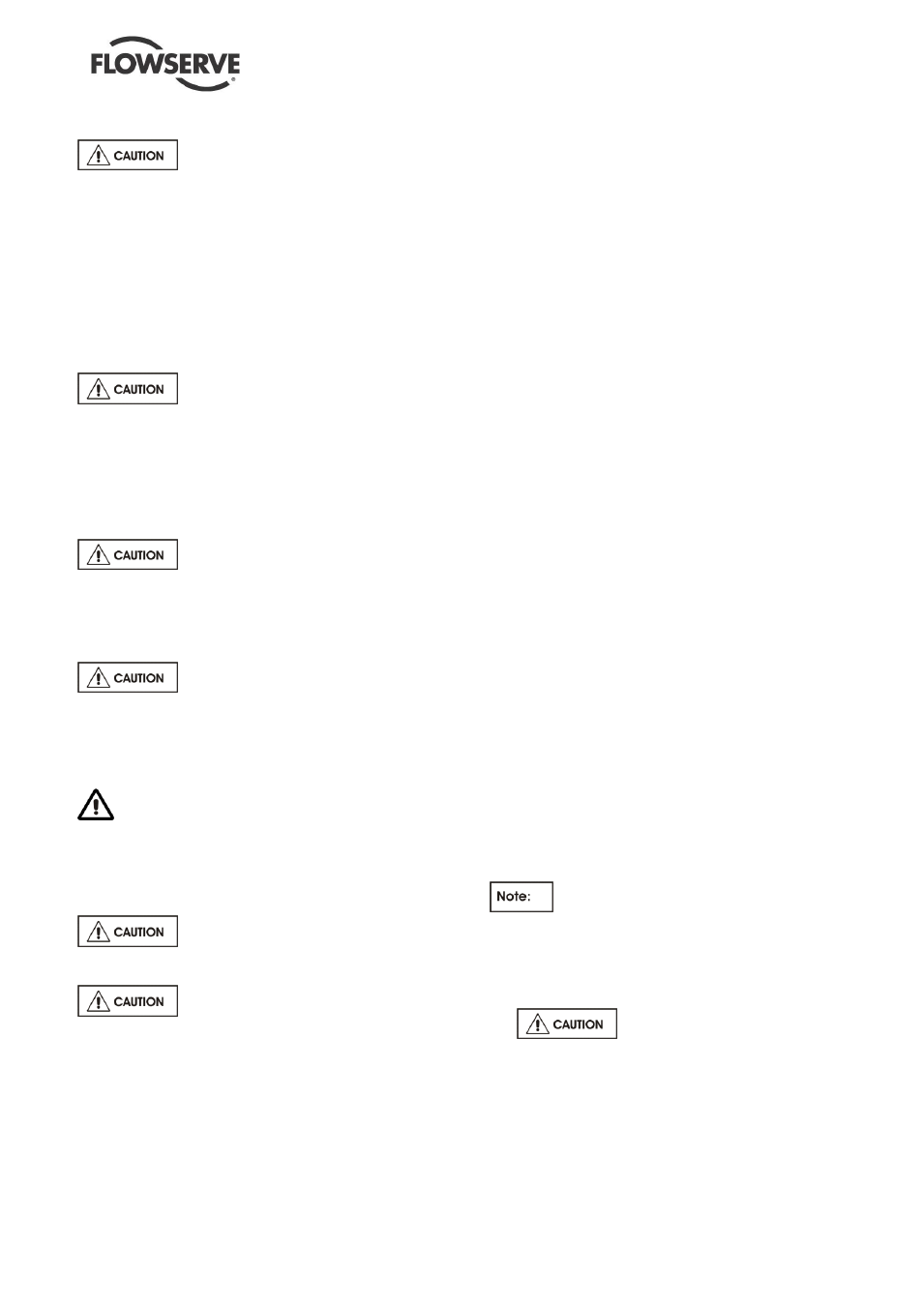
PHL USER INSTRUCTIONS ENGLISH 00079593
– 10/10
Page 17 of 31
5.1 Pre-commissioning procedure
BEFORE START-UP REMOVE
TEMPORARY RUBBER GASKET ABOVE SEAL
DRIVE COLLAR.
GASKET CAN BE EASILY REMOVED BY USING A
KNIFE OR SCISSOR TO MAKE A RADIAL INCISION.
Before using the pump, flush it with hot water to
remove any preservatives or contaminants. Drain off
the flushing water from underneath the pump.
5.2 Pump lubricants
See lubrication schedule under
Appendix 1.
5.3 Impeller clearance
No functional adjustments are to be considered.
5.4 Direction of rotation
Ensure the pump is given the same
rotation as the pump direction arrow mounted on the
pump casing.
To avoid dry running the pump must be filled with
liquid.
If maintenance work has been carried
out to the site's electricity supply, the direction of
rotation should be re-checked as above in case the
supply phasing has been altered.
5.5 Guarding
Guarding is supplied fitted to the pump set.
If this has been removed or disturbed ensure that all
the protective guards around the exposed parts of the
shaft are securely fixed.
5.6 Priming and auxiliary supplies
Ensure all electrical, hydraulic,
pneumatic, sealant and lubrication systems (as
applicable) are connected and operational.
Ensure the inlet pipe and pump casing
are completely full of liquid before starting continuous
duty operation.
De-aerate the pump via the chamber of the
mechanical seal or via the flange of a pipe connected
to the mechanical seal
5.7 Warming-up instructions for hot
pumps
5.7.1 Prefix
For pumps with a duty temperature above 200
o
C,
bearing cooling is required as to be specified on the
pump data sheet. Stuffingbox cooling is required
depending on the sealselection and conditions
required to the seal. In general, this means that
stuffingbox cooling is not required, when a cooling
system on the sealharness is sufficient to maintain
a constant duty temperature of the seal, which is
lower than the design temperature of the seal.
However, because not all factors which have their
impact on the temperature and duty of the seal are
constant factors, such as heat flux pump, heatload
seal, ambient temperature, the wear of the seal and
friction of the sealfaces etc. or in case that process
fluid cooling is required, jackets on the
stuffingboxes might be applied.
5.7.2 Warming-up procedure
When a cooling jacket is applied on the stuffingbox,
the pump with a duty temperature above 100
o
C
has to be warmed-up, to avoid difficulties caused
by thermal expansion of the relevant pump parts
through thermal shock (pumphousing, cover, shaft,
jacket, seal and connection parts etc.).
Follow below mentioned instructions punctual:
First-
Check if cooling medium to the jacket is
connected and with the required flow.
Second- Bring the pump to the working
temperature from 100
o
C at a time
schedule of 5
o
C per minute. Up to 100
o
C no special time schedule is required.
(see also chapter commissioning).
Third-
Check at duty of the pump that no major
thermal fluctuations appear with a time
schedule larger than described under
“second”.
for stopping the pump, the time schedule
as described for warming-up should be
held in opposite time-temp. schedule
(cooling-down 5
o
C per minute).
5.8 Starting the pump
a)
Ensure flushing and/or cooling/
heating liquid supplies are turned ON before
starting the pump.
b) CLOSE the outlet valve.
c) OPEN all inlet valves.
d) Prime the pump.
e) Start motor and check outlet pressure.
f) If the pressure is satisfactory, slowly OPEN
outlet control valve.