6 maintenance, 0 general, 1 maintenance schedule – Flowserve PHL User Manual
Page 20
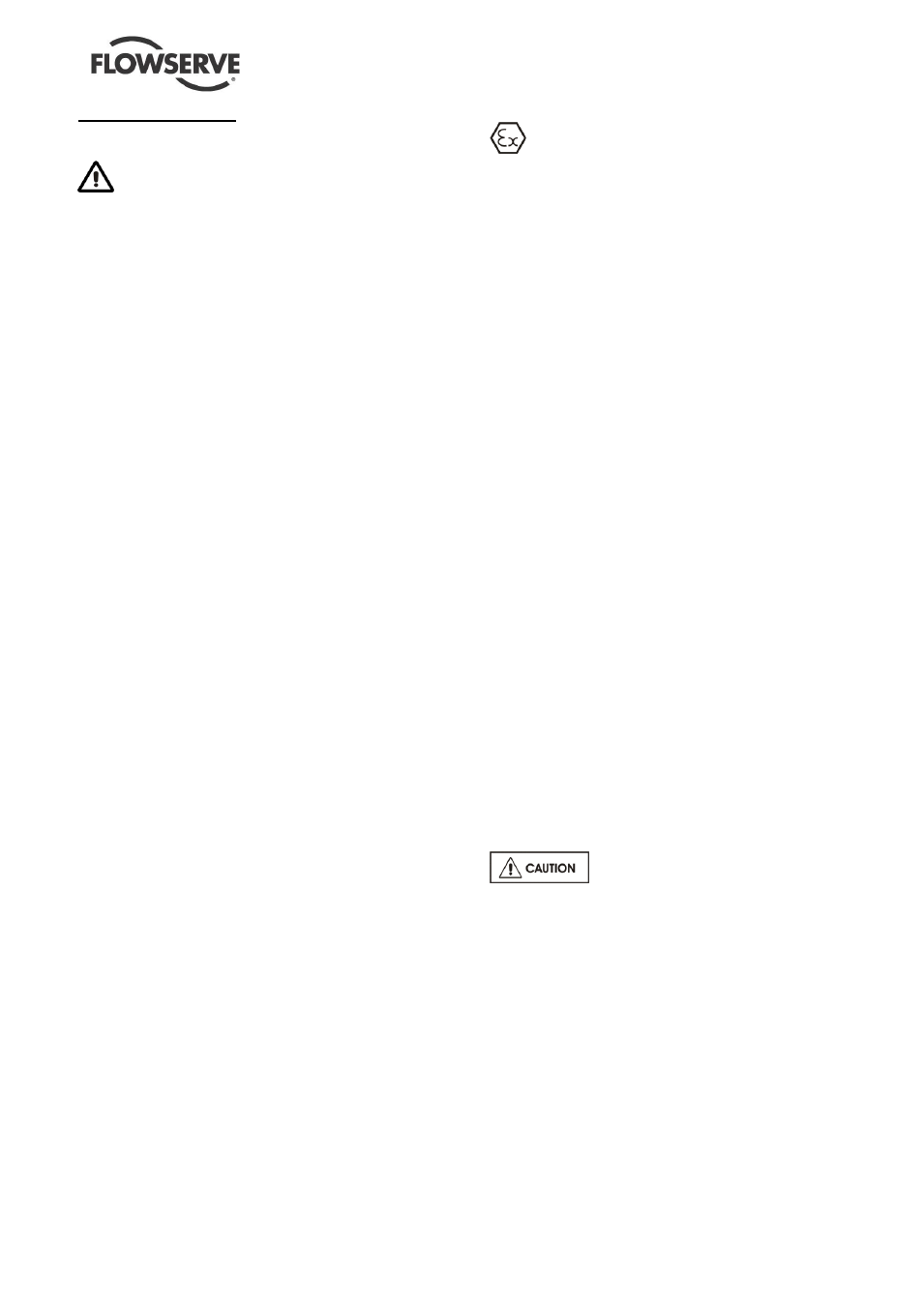
PHL USER INSTRUCTIONS ENGLISH 00079593
– 10/10
Page 20 of 31
6 MAINTENANCE
6.0 General
It is the plant operator's responsibility to ensure
that all maintenance, inspection and assembly work is
carried out by authorized and qualified personnel who
have adequately familiarized themselves with the
subject matter by studying this manual in detail. (See
also section 1.6.2.)
Any work on the machine must be performed when it
is at a standstill. It is imperative that the procedure for
shutting down the machine is followed, as described in
section 5.8.
On completion of work all guards and safety devices
must be re-installed and made operative again.
Before restarting the machine, the relevant
instructions listed in section 5, Commissioning, start
up, operation and shut down must be observed.
Oil and grease leakage can make the floor
slippery. Machine maintenance must always
begin and finish by cleaning the floor and the
exterior of the machine.
If platforms, stairs and guard rails are required for
maintenance, they must be placed for easy access to
areas where maintenance and inspection are to be
carried out. The positioning of these accessories must
not limit access or hinder the lifting of the part to be
serviced.
When air or compressed inert gas is used in the
maintenance process, the operator and anyone in the
vicinity must be careful and wear the appropriate
protection.
Do not spray air or compressed inert gas on skin.
Do not direct an air or gas jet towards other people.
Never use air or compressed inert gas to clean
clothes.
Before working on the pump, take measures to
prevent an uncontrolled start. Put a warning board on
the starting device with the words:
"Machine under repair: do not start".
With electric drive equipment, lock the main switch
and withdraw any fuses. Put a warning board on the
fuse box or main switch with the words:
"Machine under repair: do not connect".
Never clean equipment with inflammable solvents or
carbon tetrachloride. Protect yourself against toxic
fumes when using cleaning agents.
6.1 Maintenance schedule
It is recommended that a maintenance plan
and schedule is adopted, in line with these User
Instructions. It should include the following:
a) Any auxiliary systems installed must be
monitored, if necessary, to ensure they function
correctly.
b) Gland packings (if applied instead of a
mechanical seal) must be adjusted correctly to
give visible leakage and concentric alignment
of the gland follower to prevent excessive
temperature of the packing or follower.
c) Check for any leakage from gaskets and seals.
The correct functioning of the shaft seal must
be checked regularly.
d) Check pump bearing lubricant and relevant
provisions (such as constant level oiler).
e) Check motorbearing lubricant at intervals as
described in the motor instructions.
f) Check that the duty condition is in the safe
operating range for the pump.
g) Check vibration, noise level and surface
temperature at the bearings to confirm
satisfactory operation.
h) Check dirt and dust is removed from areas
around close clearances and motors.
Our specialised service personnel can help with
preventative maintenance records and provide
condition monitoring for temperature and vibration
to identify the onset of potential problems.
If any problems are found the following sequence of
actions should take place:
a) Refer to section 7, Faults; causes and
remedies, for fault diagnosis.
b) Ensure equipment complies with the
recommendations in this manual.
c) Contact Flowserve if the problem persists.
6.1.1 Routine inspection (daily/weekly)
The following checks should be
made and the appropriate action taken to remedy
any deviations:
a) Check operating behaviour. Ensure noise,
vibration and bearing temperatures are normal.
b) Check that there are no abnormal fluid or
lubricant leaks (static and dynamic seals) and
that any sealant systems (if fitted) are full and
operating normally.
c) Check that shaft seal leakage is within
acceptable limits.
d) Check pumpbearing lubricant level.
e) For motors with regreasable bearings, check
number of running hours since last recharge of
grease or since complete grease change.
f) Check any auxiliary supplies e.g.
heating/cooling, if fitted, are functioning
correctly.