1 hydraulic installation, 2 general advice for installation, 3 flexible hose riser pipe – Flowserve PLEUGER User Manual
Page 14: 4 centralizers, 5 checks before installation
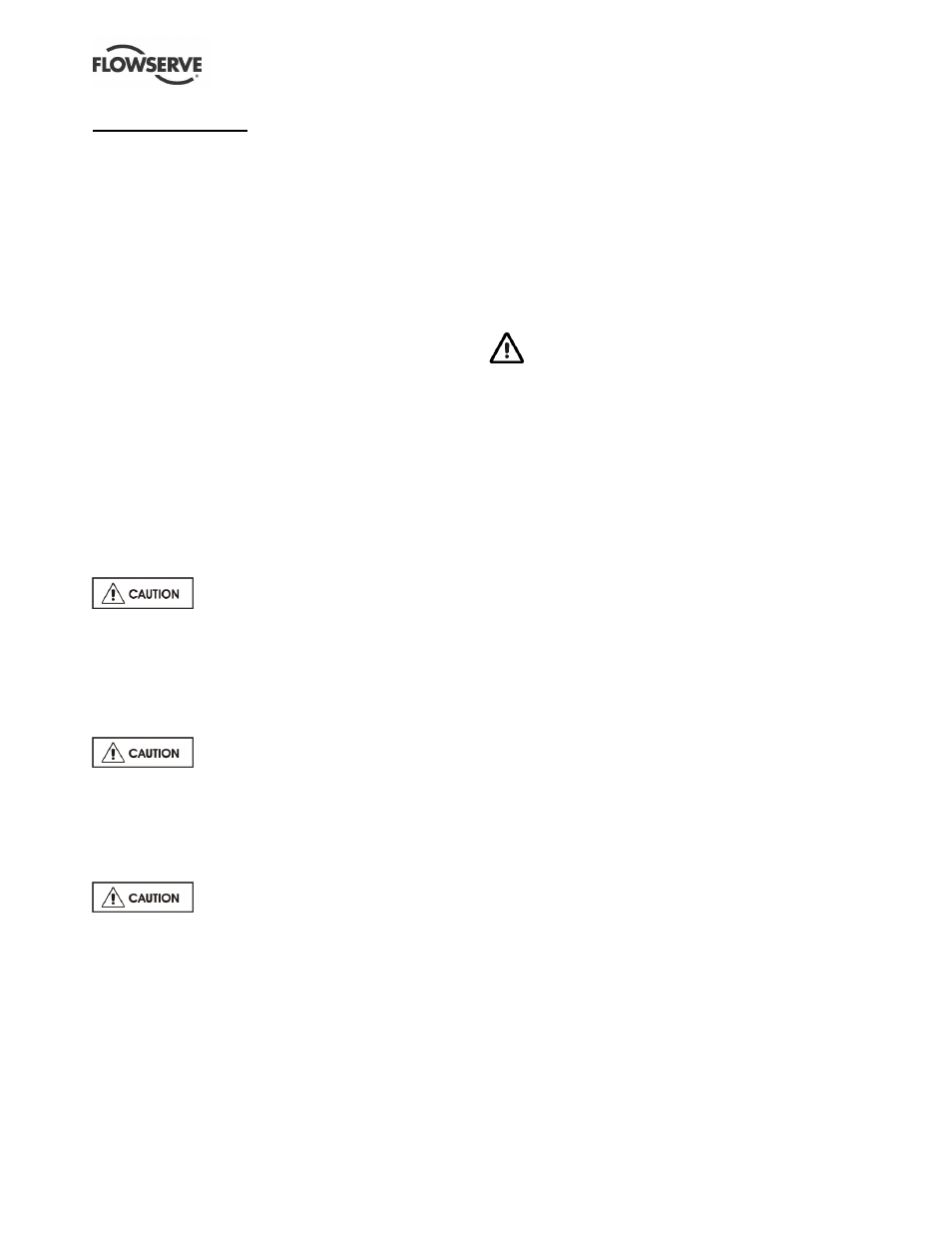
PLEUGER STANDARD USER INSTRUCTIONS ENGLISH 71569293 01-13
Page 14 of 40
flowserve.com
4 INSTALLATION
4.1 Hydraulic installation
A typical design for a water supply system is shown
in figure 3-1, Water supply system. As this shows a
basic arrangement, the actual layout must be
adapted to local conditions. (The additional
components listed are recommendations for
operational safety and protection of the pump unit.)
4.2 General advice for installation
The following criteria must be taken into account to
determine the installation position and depth:
Vertical installation in the well above the filter line,
so that an adequate motor cooling flow is
guaranteed along the external motor surface
Sufficient water cover
Static water level at least 2 m (6.6 ft.) above the
pump outlet
A dynamic water level above the suction housing,
taking into account the required NPSH for the
pump. (See pump characteristic curve.)
Flow rate. (See pump characteristic curve.)
Supply conditions of the pumping medium
(depends on the installation conditions)
Regardless of the above, the pump
unit should be installed above the well screen
whenever possible, to avoid foreign matter being
drawn directly into the pump inlet, and also to ensure
that there is sufficient water flowing across the motor
to assist heat transfer. If this is not possible a flow
shroud should be provided to induce the flow of water
over the motor.
Pump units can only be operated with
a completely filled and immersed motor. The liquid
level of the motor must always be checked before
installation and, if necessary, adjusted according to the
information on the data card supplied with the motor.
4.3 Flexible hose riser pipe
If a flexible hose is used instead of
steel pipes, these will twist against the direction of
rotation of the motor when it is switched on,
depending on the locked rotor torque of the motor. In
this case, the power cable (and, if provided, the
signal cable) fastened to the riser hose would also
twist and tighten. To prevent the cables being pulled
out of their junction boxes, they should not be laid
parallel to the riser hose but wound around it in the
opposite direction to the rotation of the motor. The
number of turns required will depend on the length
and stiffness of the riser hose line and the locked
rotor torque of the motor. The exact operating
characteristics will need to be requested from the
hose manufacturer.
4.4 Centralizers
When pump units are installed in narrow wells the
risers, whether steel pipes or hose lines, will need to
be centralized to prevent them from touching the wall
of the well which could cause damage to any cables
fastened to them.
4.5 Checks before installation
Before beginning installation, check the
dependability of auxiliary equipment, particularly
hoists, as well as comparing the information on the
data sheet with that on the rating plate on the motor.
Ensure that the line voltage (measured between two
phases) is equal to the motor voltage shown on the
rating plate.
The maximum permissible voltage fluctuation can be
seen in the data sheet. Greater voltage and frequency
fluctuations must be stated in the order and confirmed by
the factory. In case of doubt, contact Flowserve or the
nearest factory representative before starting up the unit.
Before installing, the insulating resistance of the
motor must be measured as shown in section 8.3,
Measuring insulation.
Ensure that the well diameter is large enough down
to the installation depth, so that the pump unit can be
installed without difficulties. If the riser connections
are made of pipes with flanges, these must have cut
outs for the cable if the well diameter is narrow.
When lowering the unit, ensure the power cable is
neither squeezed nor scraped. To protect the power
cables, we recommend that the well head is lined
with a rubber sheet at the entry point of the power/
signal cable into the well pipe and it is fed into the
well shaft using a cable roller. (See figure 4-1.)
During lowering, the unit must always hang freely and
must not become wedged in the well shaft. Always
ensure that the pump can be rotated freely. If
needed, attach a cable clip every 3 m (approx. 10 ft.)
of pipe length.
For especially narrow and deep wells, the insulating
measurements shown in section 8.3, Measuring
insulation, should be repeated to determine possible
damage to the power cables in time.