Flowserve MNV User Manual
Page 20
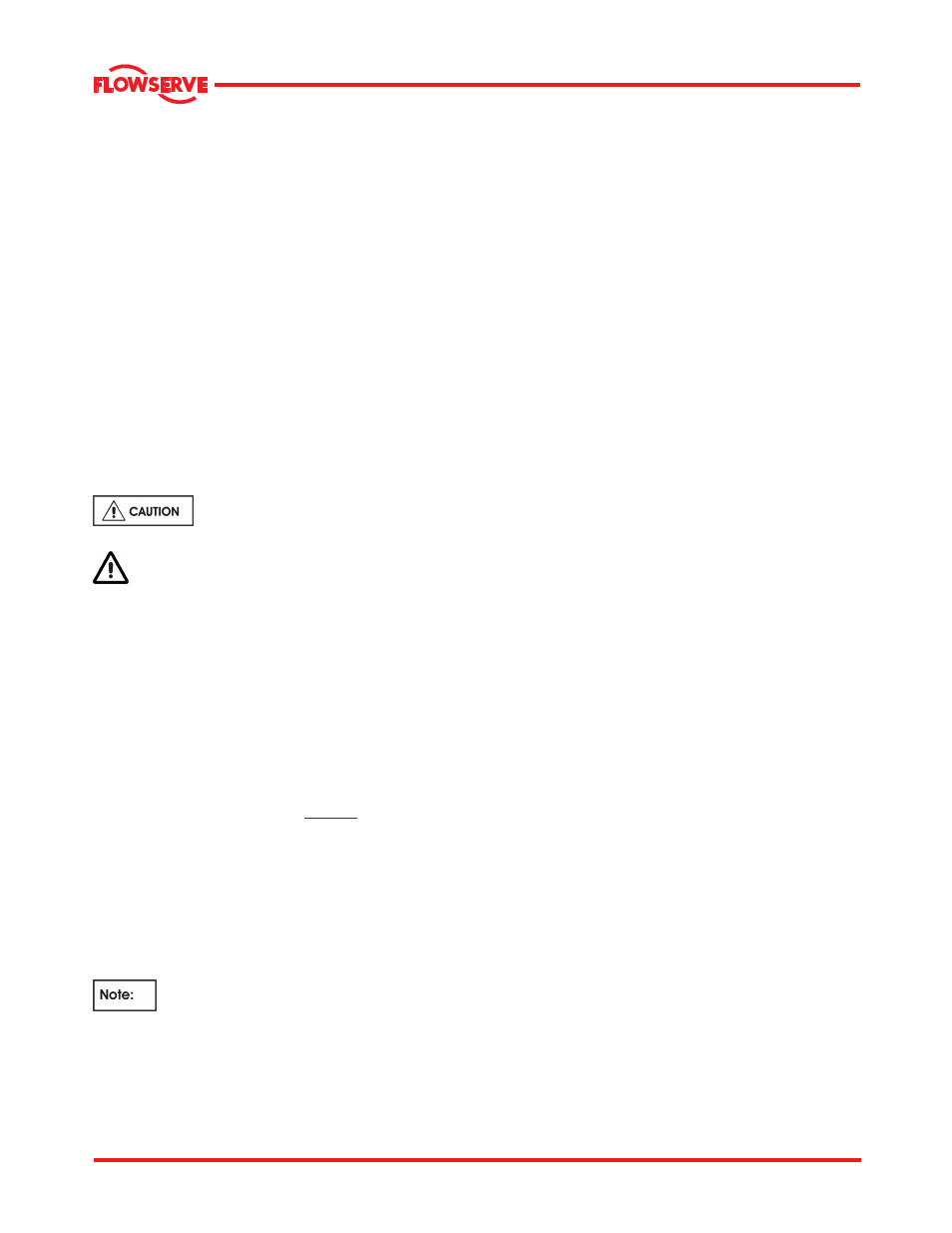
MNV & MNZ USER INSTRUCTIONS ENGLISH 71569188 11/04
Page 20 of 47
®
Consequently, when pipe couplings lack axial rigidity,
a suitable pipe anchor must be installed between it
and the pump proper. Alternately, adequate
restraining devices should be used and properly
adjusted to prevent these forces from being
transmitted to the pump. Maximum forces and
moments allowed on the pump flanges vary with the
pump size and type.
To minimize these forces and moments that may, if
excessive, cause misalignment, hot bearings, worn
couplings, vibration and the possible failure of the
pump casing, the following points should be strictly
followed:
•
Prevent excessive external pipe load
•
Never draw piping into place by applying force to
pump flange connections
•
Do not mount expansion joints so that their force,
due to internal pressure, acts on the pump flange
Ensure piping and fittings are flushed
before use.
Ensure piping for hazardous liquids is arranged
to allow pump flushing before removal of the pump.
4.6.2 Suction piping
Experience has shown that the major source of
trouble in centrifugal pump installations, other than
misalignment, is traceable to a faulty suction line.
The utmost attention must be given to this portion of
the installation to ensure that the pump receives
hydraulically stable flow. The suction piping should
be direct as possible and its length held to a
minimum. If a long suction line is required, increase
the pipe size to reduce friction losses. Then
gradually reduce the pipe size in steps before
entering the pump. The piping should be run without
having high spots and should have a continual rise
toward the pump. This prevents air pockets.
Clean out all debris from the suction line and wet well
prior to operating the pumps. Care should be
exercised to keep the suction piping air tight and
sealed against leakage.
Isolation valve in suction line is strongly
recommended to facilitate future servicing needs. An
isolation valve is recommended in the suction line, if
a positive head exists.
4.6.2.1 Suction piping guidelines
a) The inlet pipe should be one or two sizes larger
than the pump inlet bore and pipe bends should
be as large a radius as possible.
b) Pipe work reducers should have a maximum total
angle of divergence of 15 degrees.
c) On suction lift the piping should be inclined up
towards the pump inlet with eccentric reducers
incorporated to prevent air locks.
d) On positive suction, the inlet piping must have a
constant fall towards the pump.
e) Flow should enter the pump suction with uniform
flow, to minimize noise and wear. This is
particularly important on large or high-speed
pumps that should have a minimum of four
diameters of straight pipe on the pump suction
between the elbow and inlet flange.
f) Inlet strainers, when used, should have a net free
area of at least three times the inlet pipe area.
g) Do not install elbows at an angle other than
perpendicular to the shaft axis. Elbows parallel
to the shaft axis will cause uneven flow.
h) Except in unusual circumstances strainers are
not recommended in inlet piping. If considerable
foreign matter is expected a screen installed at
the entrance to the wet well is preferable.
i) Fitting an isolation valve will allow easier
maintenance.
j) Never throttle pump on suction side and never
place a valve directly on the pump inlet nozzle.
4.6.3 Discharge piping
A check valve and a gate valve are normally installed
in the discharge line. The check valve is normally
placed between the pump and the gate valve to
protect the pump from any excessive back pressure
and reverse rotation that may be caused by water
running back through the pump casing during a driver
or power failure. Any reverse flow through the pump
or excessive back pressure should be kept to an
absolute minimum. The check valve will also prevent
suspended solids from accumulating in the casing
and will increase wearing life.
•
Pipe work reducers should have a maximum total
angle of divergence of 9 degrees.
•
Fitting an isolation valve will allow easier
maintenance.
•
A compound pressure gauge should be
connected to the suction and a pressure gauge
connected to the discharge side of each pump.
Mount the gauges at a convenient location as
they are necessary for any adequate check on
pump performance.