Repair procedures – Flowserve V-377 R4 Edward Valves User Manual
Page 14
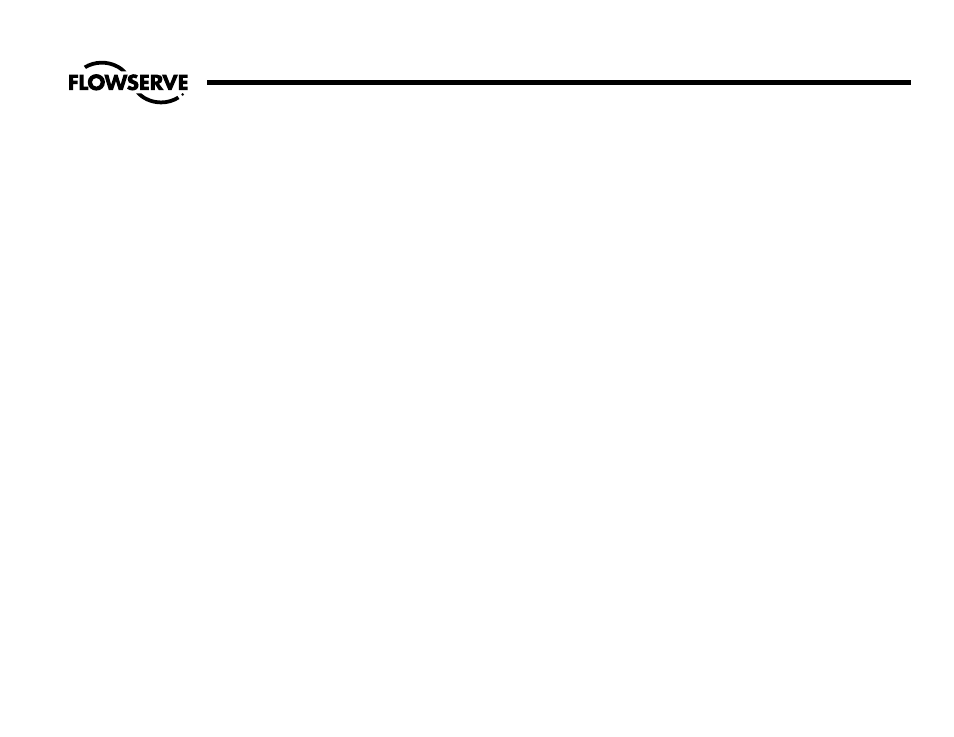
14
Flow Control Division
Edward Valves
2. Heat the body area adjacent to the
guide rib to approximately 200°F.
This can be done locally with an oxy-
acetylene torch.
3. Select the proper welding rod to suit
the body material (1/8” maximum
size rod is recommended here). See
page 16 for weld rod recommenda-
tions. Using the same welding proce-
dure as described for step 6 in the
previous section, build up the guide
rib at least 1/16” above the original
finished surface. The welding should
be started at the bottom so as to cre-
ate a small shelf, and then proceed-
ed up the guide rib.
If stainless steel inlay is desired on
the guide ribs, use AWS 5.4, E309L
stainless electrodes.
4. Finishing after welding is also similar
to that described in the previous sec-
tion and in addition, the edges of the
guide ribs should be rounded off
smooth. Check the progress of the
grinding by using a straight edge
and feeler gauges. As the bonnet
bore and guide rib approach align-
ment a light can be placed on one
side of the straight edge and the high
spots in the guide rib observed on
the other. Where a check valve or
stop-check (non-return) body is being
repaired, the progress of the finishing
cuts can also be measured by slip-
ping some long pieces of shim stock
between the I.D. of the body guide
ribs and the O.D. of the disk-piston
assembly, which has been placed
centrally in position on the seat joint.
A shim should pass around the disk
at all three guide ribs with equal
clearance. The original design clear-
ance is .020 to .030 inches on the
diameter. The disk-piston assembly
should also be moved up and down
to make sure that it is free.
It is recommended that where guide
rib repairs have been made, the seat
and disk joint be checked for distor-
tion and relapped, if necessary.
Seat and Disk Repair
The following description does not apply to
tilting-disk check valves. For repair informa-
tion on these valves, contact your local
Edward Sales representative.
A valve seat joint will require repairing in
any instance where the seating surface per-
mits a leak because it has been altered
from the original state in which it was
shipped from the factory; where corrosion
has set in to cause pit marks on the seating
surfaces of either the body or disk; where
the seat has become distorted because of
an abnormal heating condition; or, where
a groove has been formed on the seat or
disk by closing the valve against a foreign
body. Verification of such a faulty condition
may be obtained by a seat blueing test or
by careful visual examination.
The stellited seats in these pressure-seal
valves are not easily scored, but where
reconditioning is necessary, the following
points should be observed:
Where an indentation or pit marks on
the valve seat joint are deep (.010 or
greater), a cast iron lap with suitable
lapping compound will speed up
repair. The included angle of the valve
seat is 90° and the cast iron lap should
be closely guided in the body bore dur-
ing the lapping.
Lap first with the cast iron lap and finish
with the valve disk, which has been
reground or relapped, if necessary. For
initial lapping, use Clover compound
“A.” Norton 320 mixed with olive oil
or sperm oil to a molasses consistency
is also recommended for finish lapping.
For rough lapping, Carborundum H20
coarse is recommended.
In the lapping operation, lap against
the seat with a small quantity of the lap-
ping compound placed between the
mating surfaces. It is important that not
too much pressure be applied on the
lap or disk against the seat. With the
lapping compound in place between
the mating surface, the lap or disk
should be reciprocally rotated as far as
arm movements will permit while stand-
ing in one position; the strokes should
be light, and the lap or disk should be
lifted frequently and turned to a new
position circularly around the valve
body so that lapping will be rotated
over a new area. To make certain the
pressure strokes are light, it is neces-
sary on large valves to suspend the disk
and stem assembly from a coil spring in
such a manner as to allow the disk to
bear, but lightly, against the seat. See
Figure A on page 17; for another type
see Illustration No. 7.
Repair Procedures
(continued)