Repair procedures – Flowserve V-377 R4 Edward Valves User Manual
Page 15
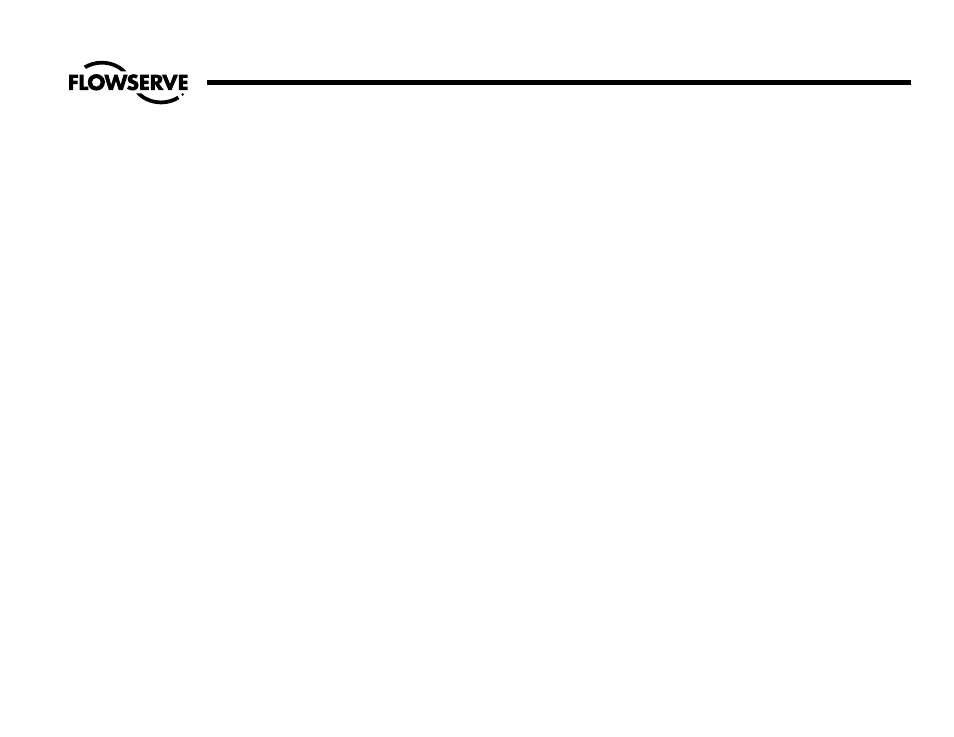
15
Flow Control Division
Edward Valves
For smaller size valves, a driving han-
dle can be easily made of 3/8” diame-
ter wire bent as per Fig. B on page 17.
These small assemblies, being much
lighter, do not require a supporting
spring. Stellited seating faces are hard
and lapping time is variable, depend-
ing on the extent of flaws on the surface
and the position of the valve in the line.
If a seat requires machining prior to
lapping, a fixture similar to that shown
in Illustrations 8 and 9 on page 17,
can be used.
The disk of stop valves will also require
refinishing. When the only defects that can
be found on the disk-stem assembly occur
on the seating surface, it becomes very
convenient to push the stem into a lathe
spindle and chuck on the disk nut diameter
without taking the assembly apart. (Howev-
er, if the stem is too large to fit through the
lathe spindle, it will have to be taken apart
as described in the following paragraph).
Hold the disk using a four jaw chuck so
that the large O.D. and seating surface run
true. Grind the seating surface using a tool
post grinder. Just go deep enough to clean
the surface. Polish the seating surface with
fine emery cloth.
If, when checking the disk-stem assembly,
it is found that the assembly is tight or does
not swivel freely, it will be necessary to
disassemble. Occasionally it is possible to
cut the lock welds with a hack saw and
unscrew the disk from the disk nut. Howev-
er, it will usually be found expedient to
chuck the disk O.D. in a lathe and cut the
lock welds, including the weld that pene-
trates the first thread. After this weld metal
has been cleaned away, the disk nut will
readily unscrew. Repair any damaged sur-
faces on the stem, disk nut, stem collars or
disk. Then proceed to repair the disk seat-
ing surface as described above. When fin-
ishing the disk in this manner, it will not be
necessary to lap it to the seat.
Body Wall Repair
There are five basic steps in repairing a
casting defect:
1. Cut out to sound metal. Attempting to
weld over the defect will only leave a
notch that may reintroduce the defect.
Cutting may be done by chipping,
grinding or flame gouging. The amount
of metal removed should be held to a
minimum to avoid distortion during sub-
sequent welding.
2. Preheat, using the minimum temperature
specified by the material specification
and/or the design code. Use at least
400F on WC9 or C5 material, 300F on
WC6. Although cast carbon steels such
as WCB or WCC do not require pre-
heat, it may be advantageous to
remove any moisture or other contami-
nants from the area to be welded. This
may also identify any leak paths. There
are also disadvantages to preheat,
especially localized preheat, that must
be considered when working in areas
of the casting with finish machined
dimensions. Distortion may result in
more damaging problems than those
concerns created by the original defect.
Lower preheats and the control of inter-
pass temperature are two methods used
to minimize distortion.
3. Welding should be done by qualified
welders, using qualified procedures and
weld material of a chemistry matching
the casting (see Table on page 16 for
welding rod recommendations). The
final weld should be blended into the
contour of the casting.
4. Stress relieving is generally recommend-
ed. Decisions to not stress-relieve should
factor in piping code rules. The temper-
atures must be based on material speci-
fication and piping code recommenda-
tions. Again, since temperatures are
much higher than those experienced in
welding, there are also disadvantages
that must be considered. Distortion may
result in more damaging problems.
Lower temperature post-weld heat treat-
ment is sometimes an option for carbon
steels.
5. The final weld should receive any need-
ed nondestructive testing. This should
include a visual examination and liquid
penetrant or magnetic particle examina-
tion. Some major weld repairs could
even mandate radiography to ensure a
sound weld.
VALVE COMPONENT REPAIR
Disk-Piston Assembly Repair
It is possible that the bearing surfaces on
the O.D. of the disk-piston assembly and
I.D. of the body can become scored
deeply enough to cause a binding or
wedging of the piston assembly in a full, or
partially, open or closed position. Such
scores and resulting burrs may be caused
by particles of weld spatter, flakes of hard
Repair Procedures
(continued)