Flowserve 3200MD User Manual
Page 19
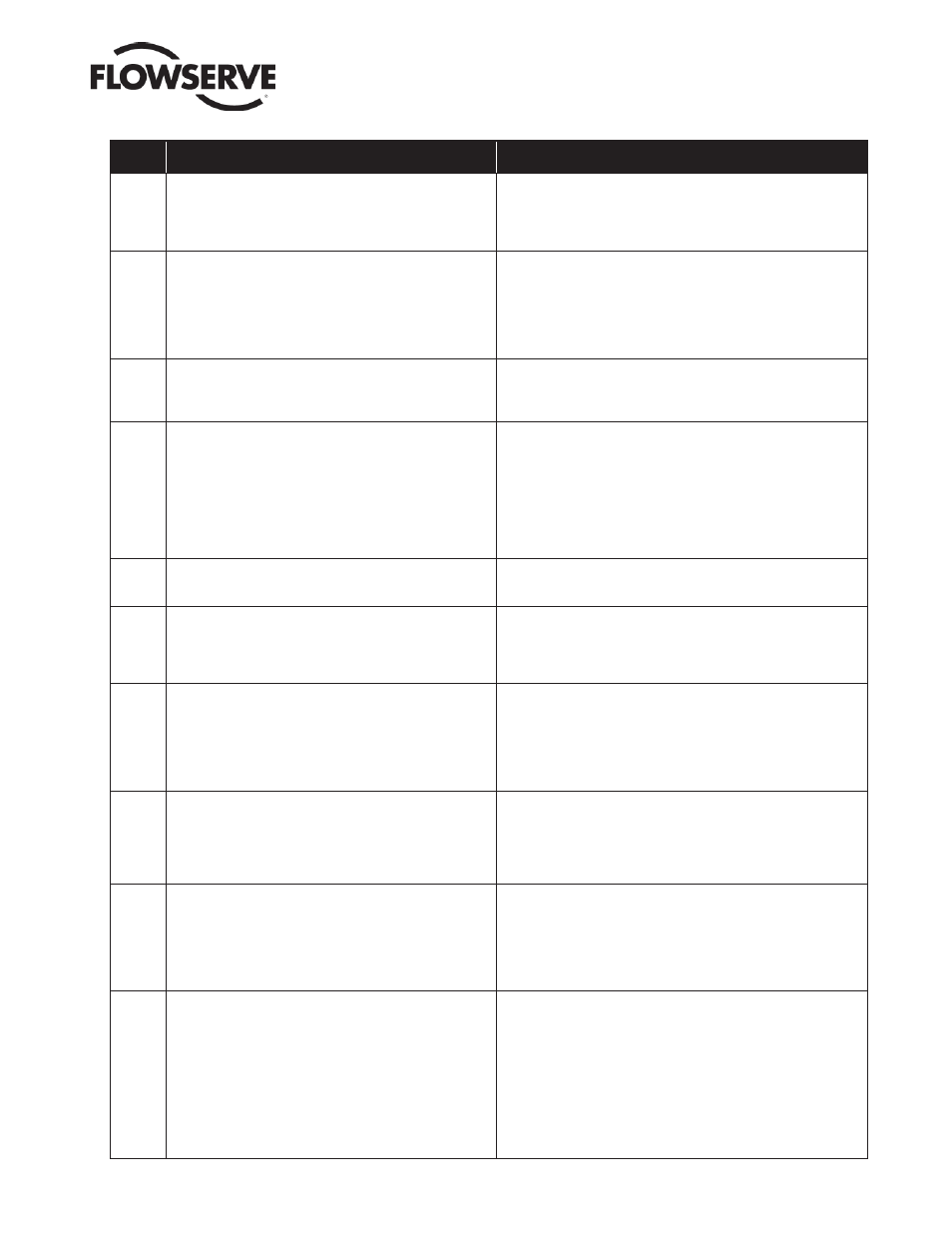
User Instructions - Digital Positioner 3200MD LGENIM0059-09 12/13
19
Blink
Code
Description
Recommendations
**YYGR SUPPLY PRESSURE HIGH WARNING indicates the positioner
has determined that the supply pressure is above the user set
warning limit.
Regulate the supply pressure at the positioner below the maximum limit
recommended for your actuator. Recalibrate pressure sensors. Check
the pressure sensor board connections. Replace pressure sensor board
if necessary. See DTM screen: Health Status/Actuator Health. This
indicator can be disabled.
**YYYG SUPPLY PRESSURE LOW WARNING (user set) indicates that the
supply pressure is below the user set warning limit. Low supply
pressure can cause poor valve response or positioner failure.
The minimum recommended supply pressure is 30 PSI (2.1 bar)
for proper operation. The unit will fail at less than approximately
17 PSI (1.2 bars). Low supply pressure indications can also be
caused by pneumatic leak.
Regulate the supply pressure at the positioner above 30 PSI (2.1
bar). Recalibrate pressure sensors. Ensure system air/gas supply is
adequate. Repair kinked supply tubing. Check the pressure sensor board
connections and replace pressure sensor board if necessary. Check for
pneumatic leaks in the actuator and actuator tubing. See DTM screen:
Health Status/Actuator Health. This indicator can be disabled.
**YYYY ACTUATION RATIO WARNING (user set) indicates a decreased
ability of the system to actuate the valve. It is based on the ratio
of available force to required force to actuate. It is affected by the
process load, friction, spring force, and available supply pressure.
Increase the supply pressure. Reduce the friction. Check the actuator
spring. Resize the actuator. Adjust user set limits. See DTM screen:
Health Status/Actuator Health. This indicator can be disabled.
**YRGG PILOT RELAY RESPONSE WARNING (user set) indicates that
the pilot relay is sticking or slow to respond. This affects the
responsiveness, increases the chance of limit cycling and
excessive air consumption. The pilot relay is part of the inner
loop and consists of the driver module assembly with piezo (I-P
relay) which is coupled to the spool valve. The value of this
indicator corresponds with inner loop lag. Delayed response can
be caused by a partially clogged piezo or debris, oil, corrosion, or
ice on the spool, or low supply pressure.
Check response of the valve. If OK, adjust Pilot Relay Response limits.
Check supply pressure. Check the spool for debris, oil, corrosion, ice
on the spool. Clean or replace the spool assembly. Replace the piezo
or driver module assembly. Maintain a clean, water-free air/gas supply.
See DTM screen: Health Status/Positioner Health. This indicator can be
disabled.
**YRGY FRICTION LOW WARNING (user set) indicates the friction has
passed below the user set limit.
Low friction is usually an indication of improperly loaded packing or seals
in the valve and actuator. See DTM screen: Health Status/Valve Health. This
indicator can be disabled.
**YRGR PNEUMATIC LEAK WARNING (user set) indicates that the positi-
oner has detected a leak in the actuation assembly. Leakage from
the actuator can cause decreased responsiveness and excessive
air/gas consumption. Low supply pressure can also trigger this
warning.
Repair pneumatic leaks at the tubing junctions and actuator seals. Ensure
proper supply pressure. See DTM screen: Health Status/Actuator Health.
This indicator can be disabled.
YRYG
FRICTION HIGH WARNING (user set) indicates the valve/actuator
friction has passed the user set limit. High friction can cause loop
oscillations, poor position control, jerky motion, or valve sticking.
It can be caused by build-up from the process on the stem, trim or
seat , by a failing bearing or guides in the valve and actuator,
galling of the trim or stem, excessively tightened packing, linkages,
or other valve/actuator mechanical issues.
Determine if the friction is signifi cantly interfering with the valve control. If
not, consider increasing the friction warning limit. Consider the following
to reduce friction: Stroke the valve to clear off build-up. Clear any external
mechanical obstruction, loosen the packing, clean the stem, repair or re-
place the actuator. Highly localized friction or very jerky travel can indicate
internal galling. Repair or replace internal valve components. See DTM
screen: Health Status/Valve Health. This indicator can be disabled.
YRRY
ELECTRONIC INABILITY TO FAIL SAFE WARNING indicates that
the piezo may be damaged. This may prevent the proper failure
position upon loss of signal/power. This condition may occur
briefl y on an air-to-close valve that is held for long periods of
time in the closed position, or and air-to-open valve held in the
open position.
If alarm persists for more than 30 minutes, the Piezo assembly is dama-
ged and should be replaced. This indicator can be disabled.
**YRRR PNEUMATIC INABILITY TO FAIL SAFE WARNING indicates that
upon loss of air supply, the valve may not move to the fail-safe
position. The spring alone is not adequate to overcome the
friction and process load in the system. The system is relying on
pneumatic force to actuate in the direction the spring is pushing.
The failsafe spring may have failed, or it was not sized properly
for the application. Friction or process load may have increased.
Check for high friction. Repair or replace actuator spring. Reduce pro-
cess load. This indicator can be disabled.
RGGY
FEEDBACK READING PROBLEM DURING CALIBRATION ALARM
indicates that during calibration, the range of motion of the positi-
on feedback arm was too small for optimum performance, or the
position sensor was out of range.
Check for loose linkages and/or adjust the feedback pin to a position
closer to the follower arm pivot to create a larger angle of rotation if the
feedback rotation is less than 15 degrees for the total valve travel and
recalibrate. Briefl y pushing the QUICK-CAL button acknowledges this
condition and the positioner will operate using the current short stroke
calibration if otherwise a good calibration. If the condition does not clear
then adjust the positioner mounting, linkage or feedback potentiometer
to move the position sensor back into range then restart the calibration.
This error may be cleared by briefl y pushing the QUICK-CAL button,
which will force the positioner to use the parameters from the last good
calibration.