5 maximum achievable sil, 7 installation, 8 firmware update – Flowserve 3200MD User Manual
Page 31: 9 required confi guration settings, 10 reliability data
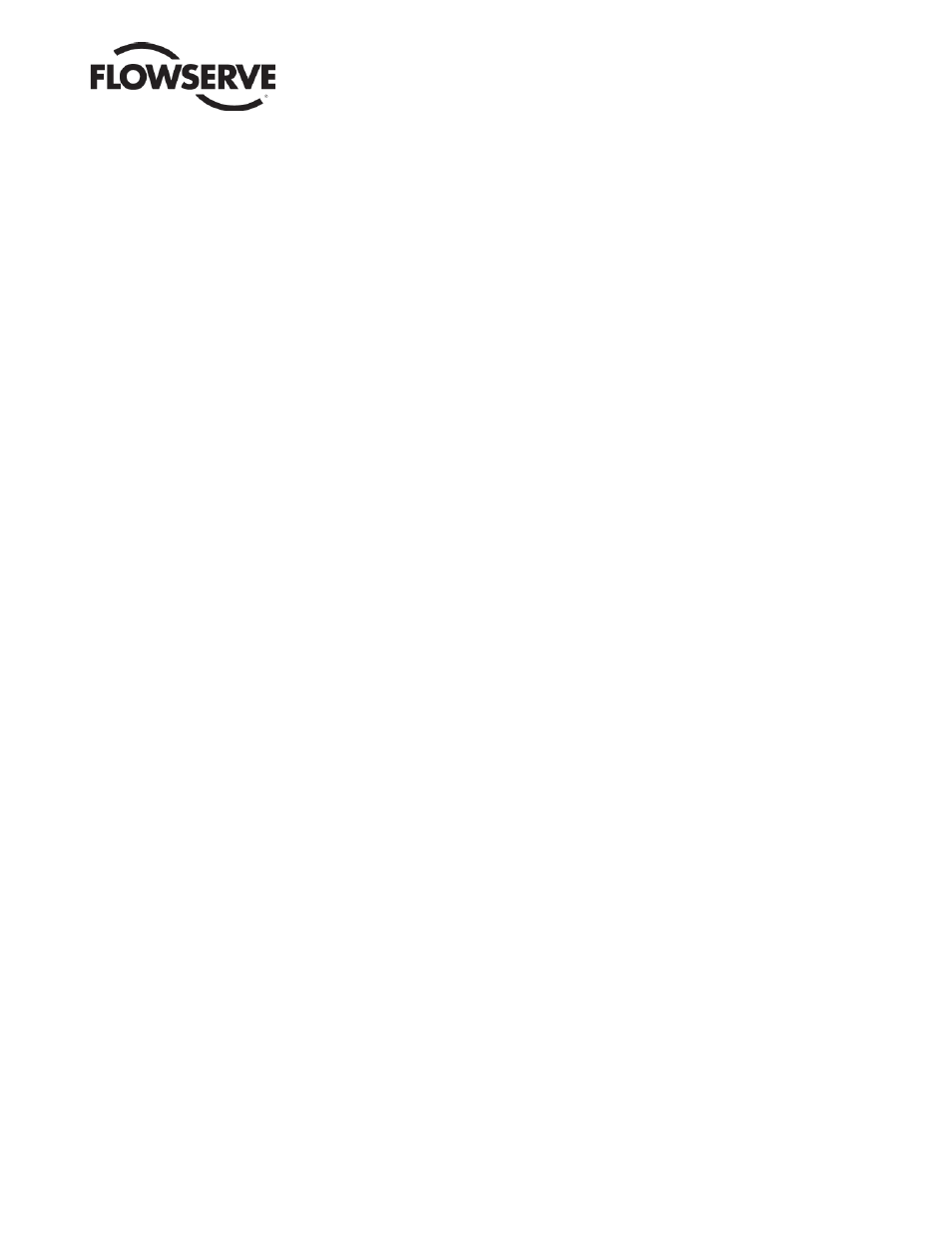
User Instructions - Digital Positioner 3200MD LGENIM0059-09 12/13
31
10.5 Maximum Achievable SIL
The Flowserve 3200MD Valve Positioner covered by this safety
manual is suitable for use in low demand mode of operation Safety
Integrity Functions (SIF) up to SIL 2 in simplex (1oo1) confi gura-
tions. The achieved SIL for a particular SIF needs to be verifi ed by
PFDavg calculation for the entire SIF including the failure rates of the
associated sensors and valves that are also part of the SIF.
Use of the Flowserve 3200MD Valve Positioner in a redundant
(1ooN) confi gurations is also limited to SIL 2.
For details, contact your Flowserve representative for Failure Mode,
Effects, and Diagnostics Analysis (FMEDA) report number FLO 09-
11-42 R001 for Logix 3200MD.
10.6 Model Selection and Specifi cation of
Flowserve 3200MD Positioner
In order to be used for SIL 2 applications as stated above, the Logix
3200MD positioner must have software version 2.05 or greater and
an Analog Output board.
The model number can be viewed on the metal tag on the positioner.
You may have a 3200IQ model that was upgraded to a 3200MD in
which case, stickers on the cover will denote the upgrade has taken
place. The software version may be verifi ed by following the instruc-
tions in section 7.9. The presence of an Analog Output board can be
verifi ed by removing the covers and viewing the circuit board. See
fi gure 24.
10.7 Installation
Ensure installation is properly performed according to this manual.
Ensure tubing is confi gured to the actuator so that the fail-safe state
of the positioner matches the desired fail-safe state of the valve.
Ensure the feedback spring is confi gured for the appropriate fail-safe
direction for the valve. For SIL 2 applications, the positioner may be
ordered with the feedback spring reversed. See Fail Option Feedback
in the How To Order section.
Ensure the A/O board has been installed. If no A/O board has been
installed, follow installation instructions in section 9.3.
!
NOTE: After
market installation of the A/O board will void FM and CSA certifi ca-
tions in North America.
10.8 Firmware Update
Ensure the fi rmware version is 2.05 or greater. The software version
may be verifi ed by following the instructions in section 7.9. Only
authorized representatives of Flowserve may update fi rmware. If
fi rmware update is required, contact your sales representative. See
the back cover of this manual for contact information.
10.9 Required Confi guration Settings
The following user settable options must be properly confi gured
for the individual application in order to provide the designed safety
integrity for that application. A method of HART communication is
required such as a HART 375 Handheld Communicator or confi gura-
tion software such as ValveSight.
•
Calibrate the A/O board.
•
Software version 2.08 or later requires the following confi gura-
tion: Enable the AO safety annunciation using the ValveSight
DTM or a Hand-held device. If using the DTM, locate the “Edit
Variables”feature. Change variable 240 to a value of 1. If using
a Hand-held device, navigate to the Confi guration menu. Use
the Write Register function to change variable 240 to a value of
1. The register type is “char”.
•
Calibrate the analog input (command). The fail safe state must
correspond to the analog input command at low current. (e.g.
For fail safe state = closed, low command (at least 4 mA)
must correspond with fully closed. For fail-safe state of open,
the low command (at least 4 mA) must correspond with fully
opened.)
•
Set the MPC to be active when the positioner is given an analog
input command to move to the fail safe state. Guarantee tight
shut-off by allowing some degree of margin taking into account
command input tolerances. (For example, if the input command
tolerance is +\- 0.5%, set the MPC to 2% when the fail safe
state is closed.)
•
Set the MPC such that during normal operation MPC is not ac-
tive. When MPC is active, some diagnostics are disabled.
•
Adjust the Pilot Relay Response Alarm settings as desired.
•
Adjust the Position Deviation Alarm settings as desired.
•
It is recommended to lock the local interface to prevent unin-
tended adjustments of the settings by an unauthorized user.
10.10 Reliability Data
For reliability data, a detailed Failure Mode, Effects, and Diagnostics
Analysis (FMEDA) report has been prepared and is available from
Flowserve with all failure rates and failure modes for use in SIL
verifi cation. See FMEDA report number FLO 09-11-42 R001 for
Logix 3200MD.
!
NOTE that the failure rates of the associated sensors and actua-
tors need to be accounted for in the Safety Instrumented Function
(SIF) level Probability of Failure High on Demand PFDavg calcula-
tion.