9 maintenance, 10 spare parts, 11 troubleshooting – Flowserve F39 Series Pneumatic Actuator User Manual
Page 8
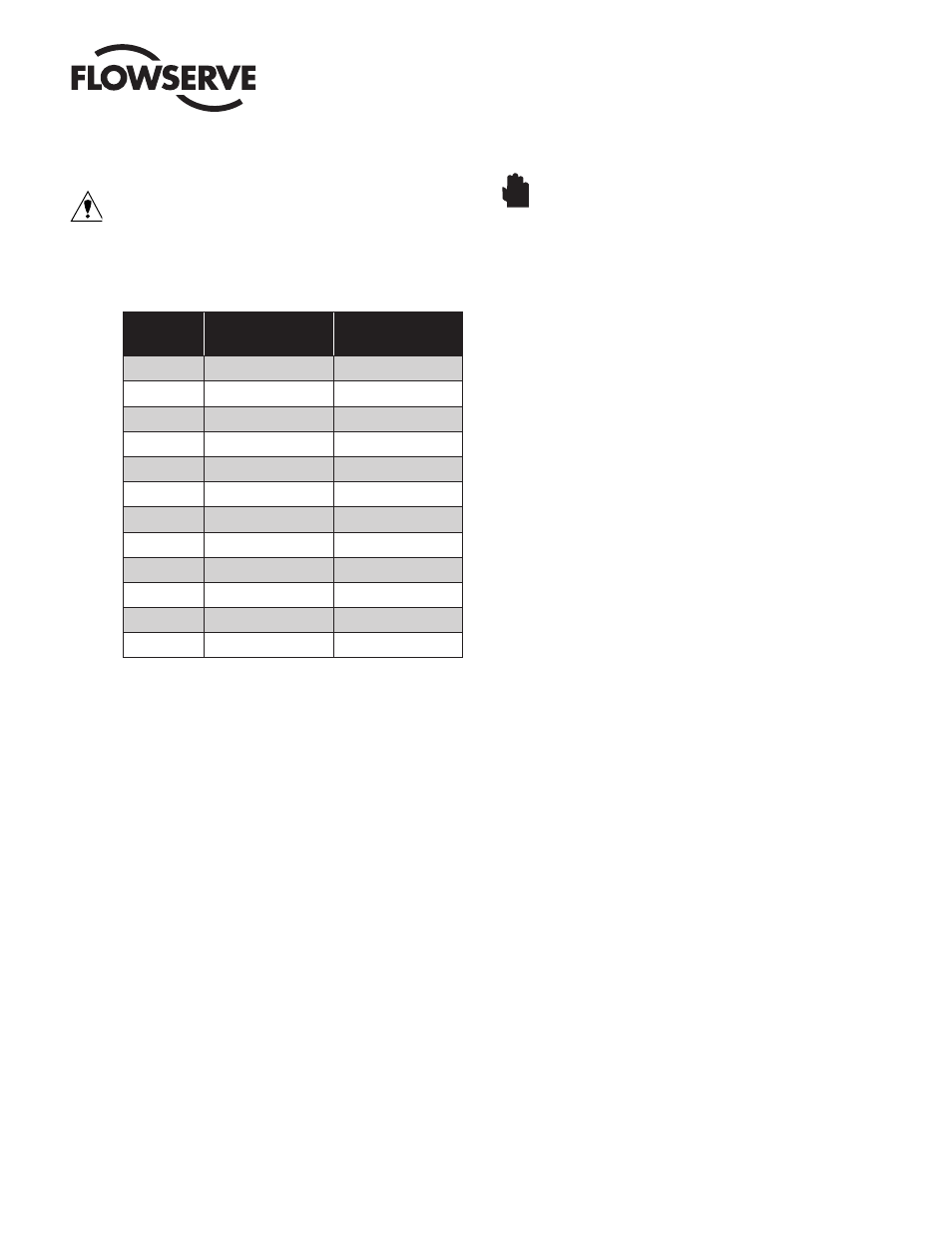
8
®
Series F39 Pneumatic Actuator - WCENIM2036-00 05/15
9 MAINTENANCE
CAUTION: The actuator must be isolated both pneumat-
ically and electrically before any maintenance activity is
begun.
Periodic checks should be performed to make certain
that all fasteners remain tight.
All actuators are supplied with sufficient lubrication for
their normal working life. If required, recommended lubri-
cation for all standard actuators is a #1 grease. Consult
Flowserve for lubricants used for high or low temperature
applications.
Depending upon the conditions under which the actu-
ator must work, such as extended duty, non-compatible
operating media or abnormal operating conditions,
periodic replacement of internal seals is recommended.
Repair kits containing all necessary seals can be obtained
through any authorized Worcester/McCANNA distributor.
On spring-return actuators, the springs may need replace-
ment after extended duty since springs may fatigue and
break. SPRINGS SHOULD ALWAYS BE REPLACED IN
COMPLETE SETS. Spring kits are available through any
authorized Worcester/McCANNA distributor.
10 SPARE PARTS
The following are recommended spare parts which should
be kept on hand for Series F39 pneumatic actuators:
Repair Kit(s) – Kits contain all necessary seals, bearings
and instructions.
Spring Kit(s) – For Spring-Return Actuators.
11 TROUBLESHOOTING
WARNING:
BEFORE DISASSEMBLING ACTUATOR FOR
ANY REASON, CONSULT REBUILDING INSTRUCTIONS
CONTAINED IN FOLLOWING SECTION.
For solenoid controlled actuators (with Worcester/
McCANNA solenoid control block)
11.1
If actuator does not function, check to ascertain:
11.1.1 That valve is free to rotate. This can be done as described
above in Manual Operation (Section 8.4).
11.1.2 That actuator is the correct size.
11.1 3 That speed control screws are loose (if screws are tight-
ened all the way, actuator will not operate).
11.1.4 That correct voltage is supplied to solenoid.
11.1.5 That sufficient air supply is available at inlet to control
block. Inlet pressure to control block should be at least 40
psig for double-acting, 80 psig for spring-return (unless a
reduced spring complement is installed (fewer springs)).
When checking supply pressure, place gauge in line at
control block inlet and monitor gauge for unexpected
pressure drops.
11.2 If proper voltage and air pressure have been verified and
valve is free, proceed as follows:
11.2.1 Turn on signal voltage. Check solenoid for clicking sound.
11.2.2 If no sound is detected, remove air pressure and turn off
signal voltage.
• Carefully unscrew solenoid and solenoid stem from
block.
• Reapply signal voltage and observe solenoid plunger. If
it does not retract, replace solenoid.
11.2.3 If solenoid functions, remove solenoid valve block and
place on bench. Connect to reduced air supply (50 psig)
and correct voltage. Switch signal voltage and check air
flow. Air should flow out only one output port when sole-
noid is energized. The flow should occur only at the other
port when de-energized. (Slight back pressure may be
required to shift the valve spool. This may be generated
by obstructing the outlet ports.)
11.2.4 If control block and solenoid are operating correctly,
proceed to Section 11 below.
11.3 If the actuator functions but exhibits leakage, or power
loss accompanied by leakage, proceed as follows:
11.3 .1 Check voltage. Voltage must be within 10% of the spec-
ified voltage (low voltage will cause leakage out of the
back of the solenoid and burn out the coil).
Actuator
size
Fastening size
Torque
05F39
M5
4Nm
10F39
M6
9Nm
15F39
M6
9Nm
20F39
M8
19Nm
25F39
M8
19Nm
30F39
M10
35Nm
33F39
M10
35Nm
35F39
M12
49Nm
40F39
M12
49Nm
42F39
M16
98NM
45F39
M16
98Nm
45F39
M20
216Nm
STOP!