12 rebuilding instructions – Flowserve F39 Series Pneumatic Actuator User Manual
Page 9
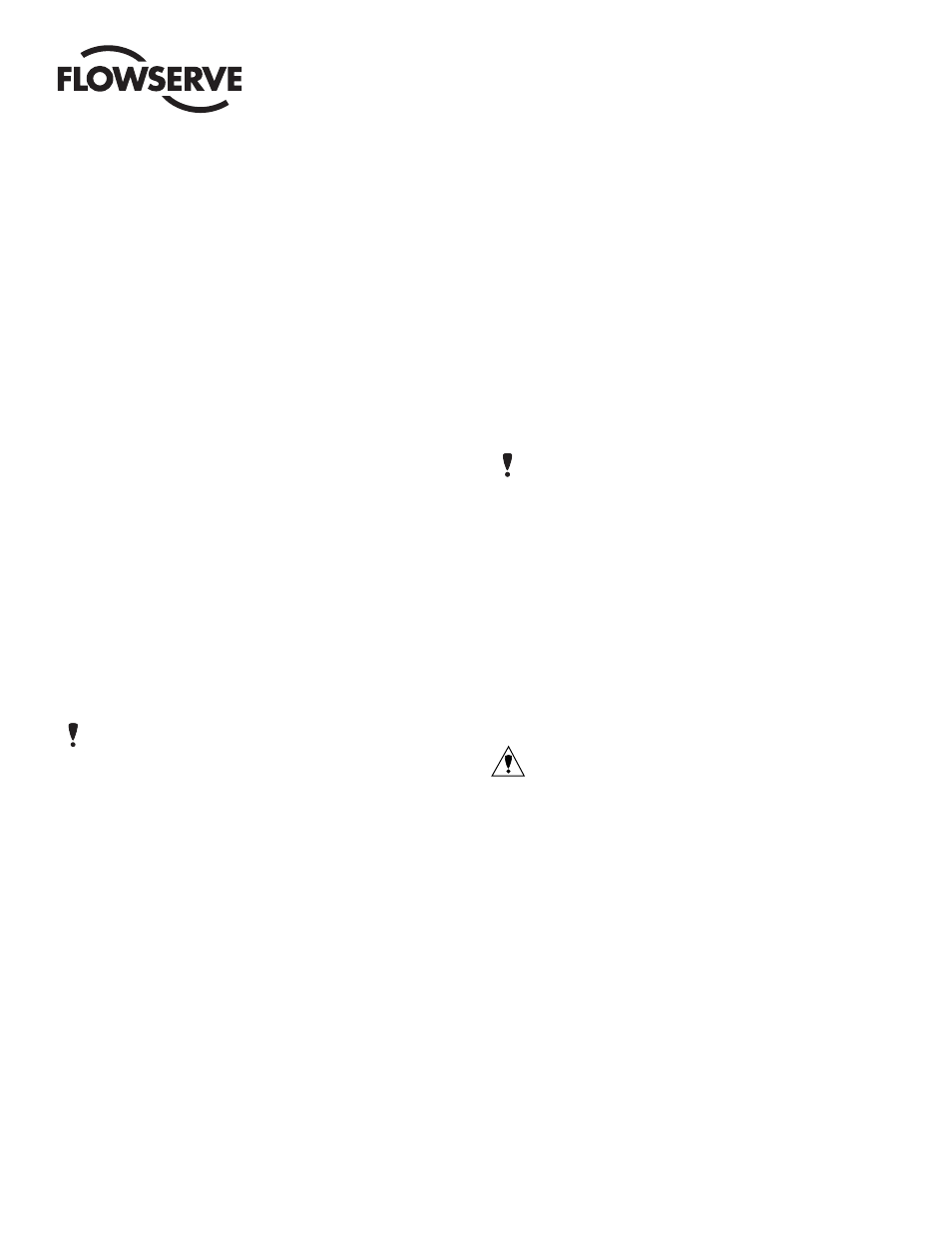
9
®
Series F39 Pneumatic Actuator - WCENIM2036-00 05/15
11.3.2 Check air supply. Be certain that no sharp air pressure
drops occur as unit is cycled. Loss of air pressure can
cause incomplete shifting of the spool valves used in all
double-acting units, which results in bypass leakage and
substantial actuator torque losses.
11.4
If air supply and voltage are adequate, proceed as follows:
11.4.1 If leak is at solenoid exhaust port, replace the solenoid.
11.4.2 If leak occurs at exhaust ports in the block itself, the
trouble will be in either the spool valves in the block, or
at one of the piston seals of the actuator. A leaking piston
seal will usually leak on either cycle.
On spring-return actuators, piston seal leakage will show
at the breather port of the end cap, or for 05F39, the sole-
noid block interface plate.
The recommended procedure in the cases above is to
replace the spool valve O-rings. If the leakage persists,
rebuild the actuator using a factory-supplied repair kit.
11.5 For actuators without the Worcester/McCANNA solenoid
control block, or if block and solenoid are operating
correctly, remove the actuator from the valve, disas-
semble (per Rebuilding Instructions) and check the
following:
11.5.1 Make sure that all internal porting is free and clear of any
obstructions. End caps, guide rods and pistons are air
transporting components.
NOTE: The most common problem encountered on F39
actuators is the improper replacement of the piston guide
rod assembly with the hole in it, relative to the nameplate
on the body (see section 12.2.6 on page 11).
11.5.2 Make certain that the actuator has lubrication, and that
there is no solidified grease between the pinion and the
piston racks:
• If actuator has no lubrication, apply generous amount
of a #1 grease. If actuator is prepared for high or low
temperature operation, consult Flowserve for proper
lubricants.
• If solidified grease between the pinion and the piston
racks is present, clean, dry, re-grease and reassemble.
11.5.3 Verify that actuator pinion shaft and/or pistons are not
bound. If bound, reassemble per Rebuilding Instructions.
11.5.4 If unit exhibits excessive amounts of backlash, check
teeth on piston racks for wear. If worn, replace piston
assemblies.
11.5.5 In spring-return actuators, check for misplaced or broken
springs. If springs are broken, check body bore for
scoring:
• If springs are broken, replace springs. SPRINGS
SHOULD ALWAYS BE REPLACED IN COMPLETE SETS.
• If body bore is scored, replace it. Also, replace piston
O rings (contained in repair kit).
11.5.6 If actuator is free, valve is free and control block (if used)
is shifting air properly, reassemble the actuator and
retest. If unit still fails to operate, consult Flowserve.
12 REBUILDING INSTRUCTIONS
NOTE: For identification of all numbered parts discussed
below, consult exploded view of actuator (see pages
14/15)
After actuator has been repaired, mark rebuild label
accordingly and apply to actuator.
12.1 Actuator disassembly
12.1.1 Disconnect the air supply and electrical service to the
actuator.
12.1.2 Remove the actuator and its mounting bracket from the
valve. If the actuator uses a positioner, loosen the set
screws in the coupling between the valve and actuator.
(See Caution note below.)
CAUTION: Ball valves can trap pressurized media in the
cavity. Isolate the piping system in which the actuator/
valve assembly is mounted and relieve any pressure on
the valve. To remove the actuator bracket from a three-
piece non-top-mount style “Miser” valve, the two top
valve body bolts must be removed. For all the valves
listed in Section 3.5, the actuator bracket can be removed
without loosening or removing any valve body bolts.
12.1.3 Remove the actuator bracket (and actuator positioner)
from the actuator to begin repair. (Note mounting of
removed bracket and positioner for easy reassembly.)
12.1.4 It is not necessary to remove solenoid control block (7A)
or (7B) (if so equipped) to rebuild actuator. However,
if it becomes necessary to remove the block, begin by
removing the solenoid block bolts (8E). Use care to retain
the solenoid block gasket (9).
For 05 size only, also remove the solenoid block interface
plate (20) and the interface gasket (19) by removing the
three screws (21).