5 limit switch settings, 3 three-phase motor, 4 dc motor – Flowserve L120-85 Actuator User Manual
Page 15
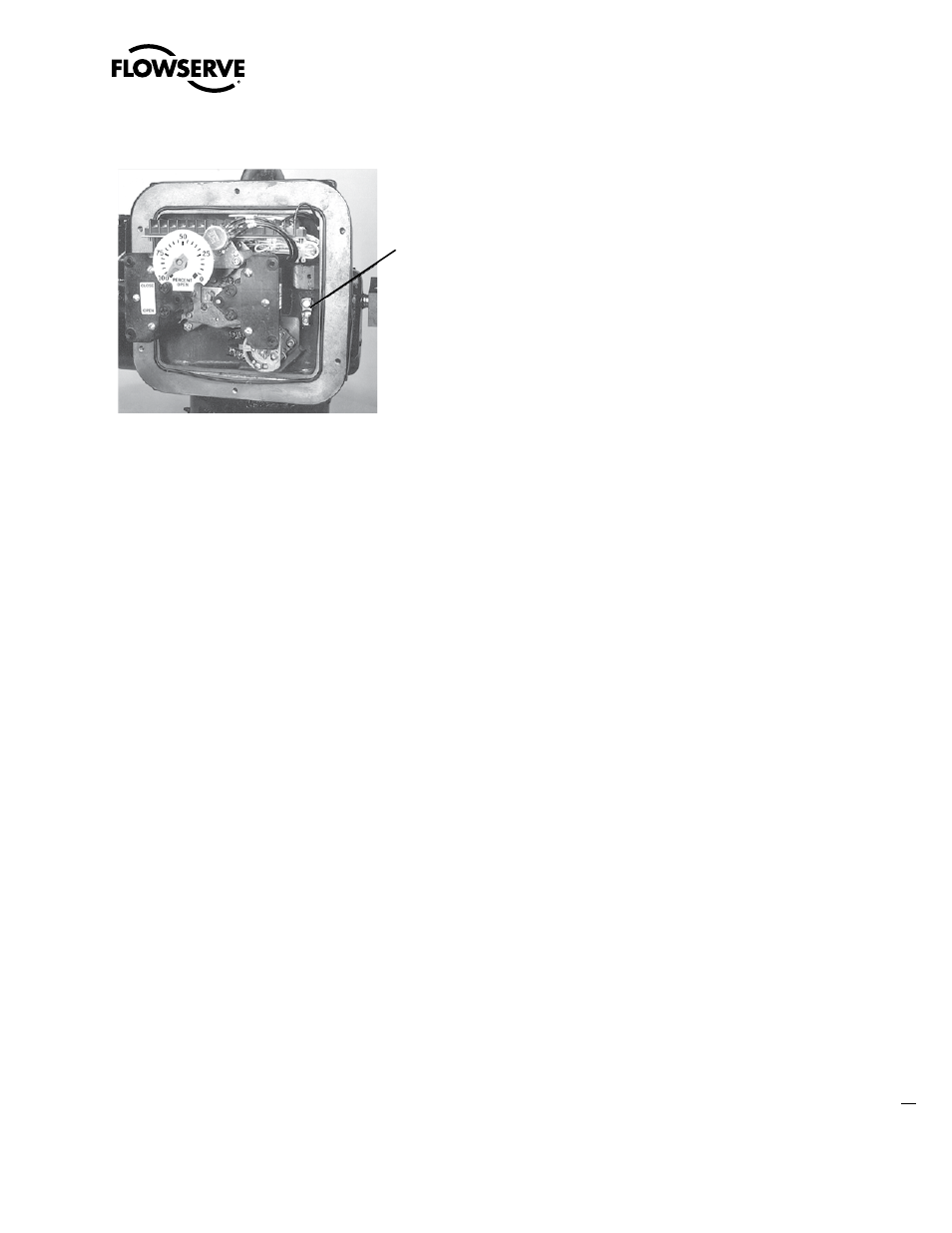
Figure 7: Grounding Lug location
Grounding Lug
7. Inspect actuator for proper lubrication. Refer to “Lubrication”
Section 6.1 for lubrication instructions.
8. Verify that Motor rotation is operating in the proper direction; the
Motor rotation will have a direct impact on the Limit Switch and
Torque Switch functions. Follow the procedure “Verifying Motor
Rotation Direction” in Sections 4.4.2, 4.4.3 and 4.4.4).
9. Close Electrical Compartment Cover (piece 200-1).
10. Unit is now ready for electrical operation. Continue to “Electrical
Start-up Procedure” in Section 5.3.
4.4.2 Motor rotation (phasing) and OPEN/
CLOSE pushbutton operation.
It is very important to check for correct motor rotation to ensure that
serious damage to your valve or other equipment does not occur.
If the actuator motor rotates in the wrong direction, damage could
occur by over-torquing equipment into a seated position.
Prior to being shipped from the factory, each actuator is inspected to
verify proper operation of the Torque and position Limit Switch and
to ensure that they function correctly (i.e. closes when the CLOSE
pushbutton is depressed, opens with the OPEN pushbutton, etc.).
These inspections are made with a properly phased power source
connected as described in the actuator manual.
a
CAUTION: To ensure proper operation and to prevent your
actuator or other actuated equipment from damage, verify
that your unit is properly connected to its power source.
NOTE: Your application may vary from the following standard wiring
configurations for Three-phase, Single-phase and DC motors. Refer
to your actuator wiring diagram for user-specific wiring configuration.
4.4.3 Three-Phase Motor
1. Using the Handwheel, move the valve to a midtravel position
(midtravel position allows electrical operation in the valve “safe”
area and keeps the OPEN and CLOSED Limit Switches from trip-
ping while testing motor direction).
2. Be prepared to immediately remove power should the actuator
run the wrong way.
3. Test motor direction by momentarily pressing the OPEN push-
button:
A) If the actuator moves toward CLOSED, immediately turn all
power OFF and reverse the motor leads T1 and T3.
NOTE: Refer to your actuator wiring diagram for user-spe-
cific wiring configuration.
B) If the actuator moves toward OPEN, the motor is wired
properly for the application.
4.4.4 DC Motor
1. Using the Handwheel, move the valve to a midtravel position
(midtravel position allows electrical operation in the valve “safe”
area and keeps the OPEN and CLOSED limit switches from trip-
ping while testing motor direction).
2. Test motor direction by momentarily pressing the OPEN push-
button:
A) If the actuator moves toward CLOSED, immediately turn all
power OFF and reverse the motor leads A1 and A2.
NOTE: Refer to your actuator wiring diagram for user spe-
cific wiring configuration.
B) If the actuator moves toward OPEN, the motor is wired
properly for the application.
4.5 Limit Switch Settings
The standard L120-85 Limit Switch has 16 contacts. The OPEN/
CLOSE Limit Switch (first eight contacts) has two Rotor Sets, one
for the OPEN position and one for the CLOSED position. Each Rotor
Set has four electrical contacts which can be arranged in any com-
bination of normally OPEN and normally CLOSED. The SPARE Limit
Switch (second eight contacts) has two additional Rotor Sets with
four contacts each that can be set to operate anywhere between the
OPEN and CLOSE positions. These can be used to stop the valve in
mid-travel or to interlock with other equipment such as pumps, fans,
mixers, etc. Refer to Figure 8.
15
Limitorque L120-85 Installation, Operation and Maintenance FCD LMENIM1202-00 – 11/05
flowserve.com