Worcester actuation systems – Flowserve DRC-17 User Manual
Page 15
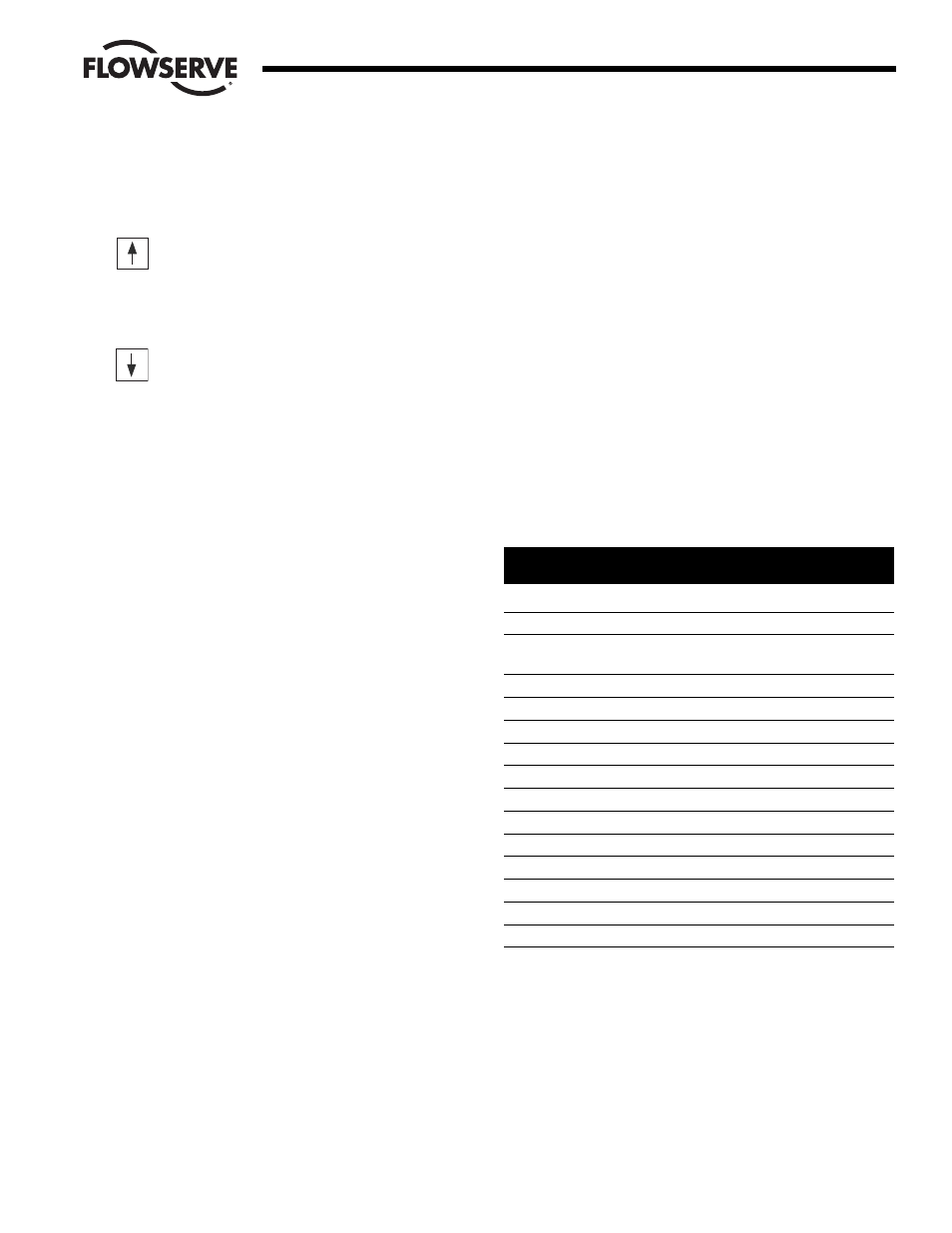
WCAIM2058
DataFlo Digital Electronic Remote Controller DRC17
15
This is the ENTER key. This key is used to accept an edited
value. While viewing alarms in the Run Mode, pressing this key
will attempt to clear the alarm condition. In the Calibration Mode,
pressing this key while setting viewing a voltage or option will
record the displayed value.
When editing parameters, pressing this key causes the
value to increase. When in either the Run Mode or
Calibration Mode, this key will move to the previous
display item. When a parameter is alternating with its value in
the Program Mode, pressing this key will move to the previous
parameter.
When editing parameters, pressing this key causes the
value to decrease. When in either the Run Mode or
Calibration Mode, this key will move to the next display
item. When a parameter is alternating with its value in the
Program Mode, pressing this key will move to the next
parameter.
4.3 Changing Modes
When the DRC has power first applied, it enters the Run Mode
and will stay in that mode to control the process. To run other
modes, use the keypad as described below:
Press either the
key or the
key until the mode display
appears.
Press ENT to edit the value. It will start blinking the current
mode.
Press either
or
until the new mode is visible.
With the correct new mode blinking, press the ENT key to
change to the new mode.
To return back to the Run Mode, press the
key.
4.4 Tuning the Controller
Proper performance of the DRC controller depends on proper
tuning of controller parameters. The DRC is shipped from the
factory with preset variables that may provide good process
control. However, optimal performance can be obtained by
tuning the system parameters.
The DRC controller provides an automated tuning procedure
(called Auto-Tune) that can help establish a starting point for
tuning the control parameters. Auto-Tune is performed as an
option in the Manual Position Mode. See paragraph 4.8.3. for
more information.
Auto-Tune can determine proper control parameter settings,
however it may be necessary to manually tune the system
further for optimum control. Several methods exist for tuning
controllers. Some methods use an open-loop approach where
the process is examined as valve position is manually changed.
Other approaches use a closed-loop method where the controller
is actively performing its function and the process is examined.
The DRC Auto-Tune procedure uses the open-loop method.
Closed-loop tuning can tell the period of cycling which is also
useful in determining the dead (or lag) time and the Motor Cycle
Interval. J. G. Ziegler and N. B. Nichols have done a great deal in
the area of control systems and have established a set of tuning
rules that can be followed for closed-loop tuning. Refer to their
work for further information.
4.5 The Run Mode
The Run Mode is the state of the DRC when it is controlling the
process. In this mode, the operator can view the process and
setpoint values, and other data. The DRC is attempting to control
the process by making it track the setpoint while in this mode.
As described above, other modes can be entered from the Run
Mode to set parameters, perform calibration, manually set the
valve position, or to manually set the operating setpoint.
4.5.1 The DRC Display
The display on the front panel of the DRC enclosure
shows operating data, parameters, alarms and other
messages. The table below shows the Run Mode displays
and their meaning. The displays are in the order they will
appear when the
key is pressed. Pressing the
key
simply reverses the order in which the displays appear.
From any data display in the Run Mode pressing the
key will return to the process variable display.
Table 1
Run Mode
Display
Definition
PV: 0
Process Variable.
SV: 0
Setpoint Variable.
AL: NONE Alarm conditions that are active
as shown below:
AL: HiPr
Process is above high-process limit.
AL: LoPr
Process is below low-process limit.
AL: HiPo
Valve shaft is above high-position limit.
AL: LoPo
Valve shaft is below low-position limit.
AL: NoFB
No shaft position feedback signal.
AL: NoPr
Invalid process signal.
AL: HiSp
Invalid setpoint signal.
AL: Ther
Thermal warning (DC motors only).
AL: NONE No active alarms.
PH: 0
Process highest tracked value.
PL: 0
Process lowest tracked value.
Md: RUN
Mode of operation.
4.5.2 Alarms
If an alarm condition occurs, the condition is viewed with
the alarm display as shown above. If more than one alarm
condition is active, the highest priority alarm will be shown.
The priority of alarms is the order shown in the table. So if
the process has gone above the programmed high limit
and the shaft position is lower than the programmed limit,
the display will show the high-process alarm.
Flow Control
Worcester Actuation Systems