Worcester actuation systems – Flowserve DRC-17 User Manual
Page 28
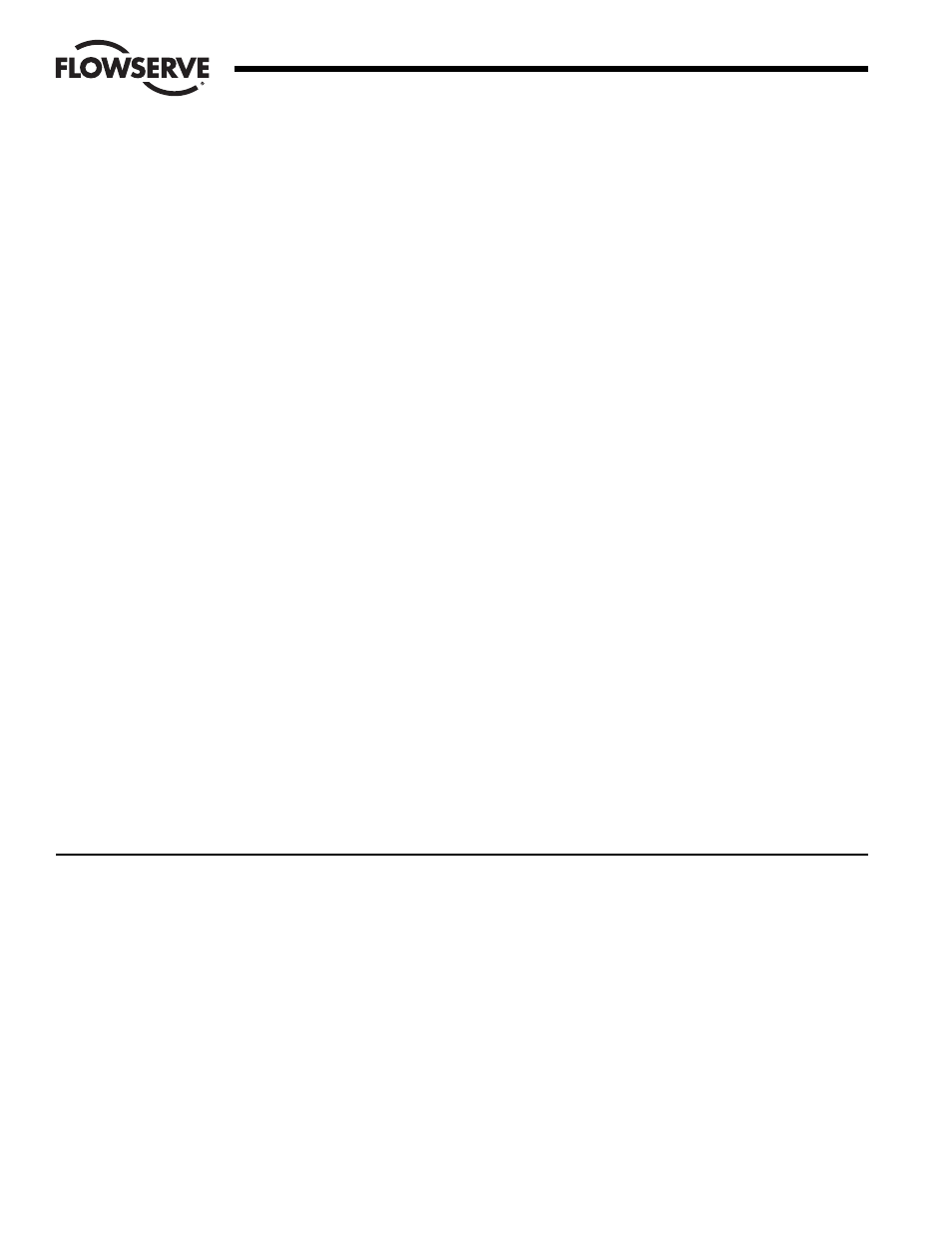
6.5.9 What to check: With power off and using a capacitance
meter, check the motor run capacitor for a short, for
excessively high leakage and for low capacitance.
Action to take: Replace as necessary
Notes and cautions: Disconnect all leads from the
capacitor terminals prior to testing. Do not exceed the
rated voltage of the capacitor. Make certain capacitor is
discharged before reconnecting.
6.5.10 What to check: Check the temperature of the motor(s).
One motor has a thermal cutout switch built in that opens
when the winding reaches about 210°F. If the thermal
cutout has opened, both motors are de-energized until the
thermal switch resets (20-23 75 sizes).
Action to take: Allow the motor(s) to cool so that the
thermal switch can reset. Normally the thermal switch will
not open unless the motor’s rated duty cycle is exceeded
and/or the ambient temperature is very high. Correct the
problem.
Notes and cautions: Duty cycle is specified at an ambient
temperature of 70°F and 60 Hz.
6.5.11 What to check: Check the operating torque of the valve. If
necessary, remove the actuator from the valve. Measure
valve torque with an accurate torque wrench. Check
torque under actual operating conditions if possible.
Action to take: If the operating torque of the valve exceeds
the specified torque for the seats used and the ΔP across
the valve, determine the cause and correct it. If torque
falls within normal range, the actuator may be undersized.
Notes and cautions: If the actuator is removed from a
three-piece valve that requires the body bolts to also be
removed, the valve body bolts must be tightened to
torque specifications before checking the valve torque.
See the valve IOM.
6.5.12 What to check: Check ambient temperature.
Action to take: Actuator duty cycles are specified at an
ambient temperature of 70°F.
Notes and cautions: Higher ambient temperature de-rates
the duty cycle.
6.5.13 What to check: Check to see that the mechanical brake is
operating correctly.
Action to take: Replace a defective mechanical brake. If
one was never installed, order a kit and install it in the
actuator.
Notes and cautions: All 2-inch CPT valves with the motor
driver board inside the actuator must have a mechanical
brake installed to prevent oscillation.
6.5.14 What to check: Check to see if the actuator can move a
high torque valve from a stop under load when moving in
the same direction as last commanded [a mechanical
brake does not allow the motor(s) to unwind].
Action to take: If motor(s) cannot start, go to next larger
size actuator.
6.5.15 What to check: Check to see which direction of travel
causes a problem. If the actuator slows down or stops
when coming off either the open limit switch (travelling
CW) or off the closed limit switch (travelling CCW), the
motor driver board is bad.
Action to take: Replace the circuit board.
6.5.16 What to check: Check the deadband and cycle time
parameters. A narrow deadband with a cycle time of 1.0
second and noisy signals can cause the valve to oscillate.
Action to take: Widen the deadband. Making the cycle
interval longer (than 1 second) will cause valve
movement to occur less often, but will not correct the
oscillation.
Notes and cautions: Optionally, the filter time can be
increased to attempt to filter the setpoint and process
signals. Be aware that when the filter time is increased,
the controller will respond more slowly to process and
setpoint changes.
Flow Control
Worcester Actuation Systems
Flowserve Corporation has established industry leadership in the design and manufacture of its products. When properly selected, this Flowserve product is designed to perform its intended function
safely during its useful life. However, the purchaser or user of Flowserve products should be aware that Flowserve products might be used in numerous applications under a wide variety of industrial
service conditions. Although Flowserve can (and often does) provide general guidelines, it cannot provide specific data and warnings for all possible applications. The purchaser/user must therefore
assume the ultimate responsibility for the proper sizing and selection, installation, operation, and maintenance of Flowserve products. The purchaser/user should read and understand the Installation
Operation Maintenance (IOM) instructions included with the product, and train its employees and contractors in the safe use of Flowserve products in connection with the specific application.
While the information and specifications contained in this literature are believed to be accurate, they are supplied for informative purposes only and should not be considered certified or as a guarantee of
satisfactory results by reliance thereon. Nothing contained herein is to be construed as a warranty or guarantee, express or implied, regarding any matter with respect to this product. Because Flowserve
is continually improving and upgrading its product design, the specifications, dimensions and information contained herein are subject to change without notice. Should any question arise concerning
these provisions, the purchaser/user should contact Flowserve Corporation at any one of its worldwide operations or offices.
For more information about Flowserve Corporation, visit www.flowserve.com or call USA 1-800-225-6989.
FLOWSERVE CORPORATION
FLOW CONTROL
Worcester Actuation Systems
5114 Woodall Road
P.O. Box 11318
Lynchburg, VA 24506-1318 USA
Phone:434 528 4400
Facsimile: 434 845 9736
www.flowserve.com
© 2005 Flowserve Corporation, Irving, Texas, USA. Flowserve and Worcester Controls are registered trademarks of Flowserve Corporation.
FCD WCAIM2058-01 5/05 Printed in USA.