Worcester actuation systems – Flowserve DRC-17 User Manual
Page 20
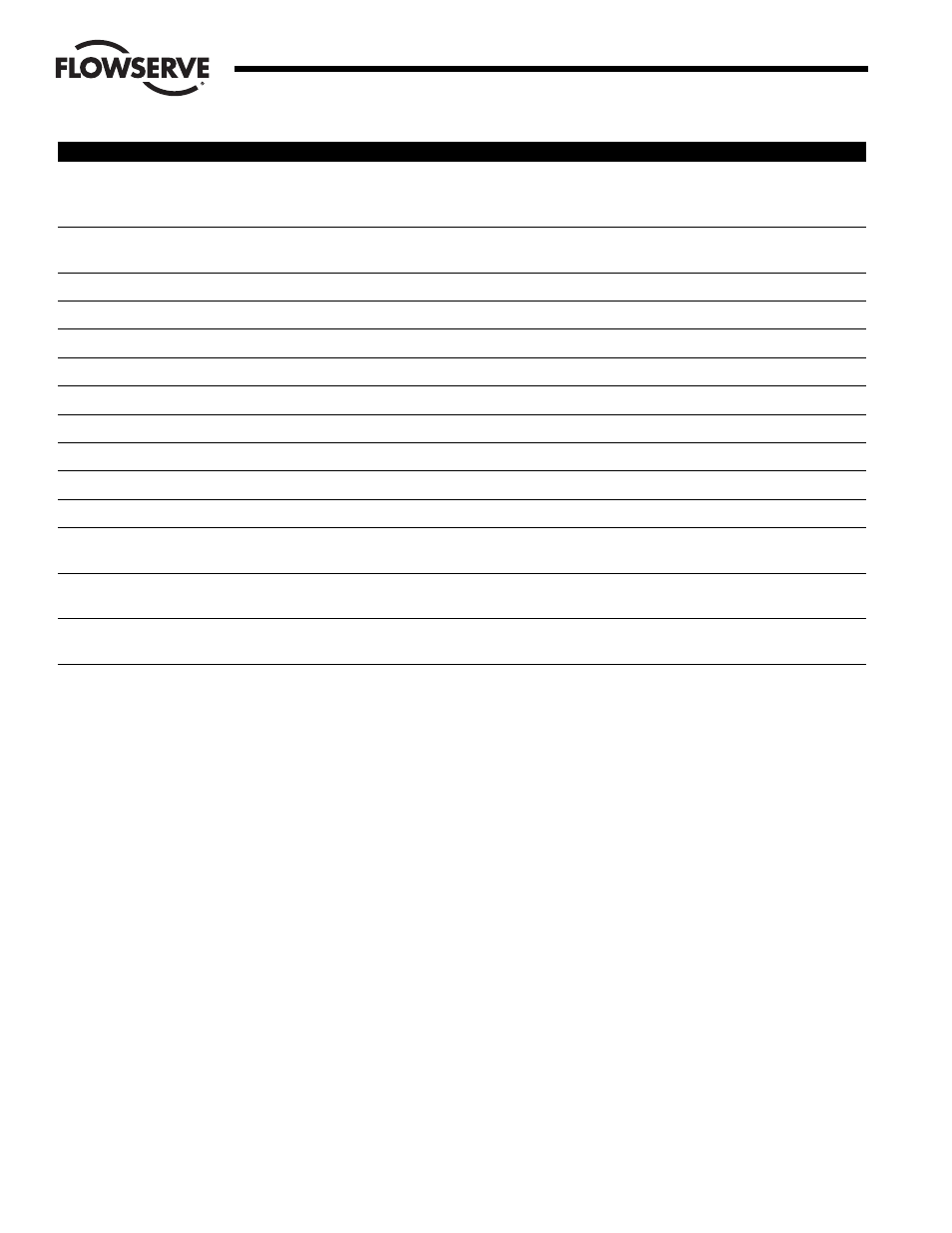
20
DataFlo Digital Electronic Remote Controller DRC17
WCAIM2058
Parameter
Display
Definition
Power-On Position
Pon Posn
Position the shaft will be driven to when power is first applied. A value of NONE will
hold the current shaft position. The position specified will be held for the time
specified in the Pon Time parameter.
Power-On Position Time
Pon Time
Time to hold the valve position specified by the Pon Posn parameter. A time value of
0 will bypass the power-on position feature.
Lower Shaft Limit
LoPosLim
Lowest position percentage the shaft can move to while controlling.
Upper Shaft Limit
HiPosLim
Highest position percentage the shaft can move to while controlling.
Brake Time
Brk Time
Amount of time the brake is applied to stop motor movement.
Cycle Count
Cy Count
The count of the number of complete valve cycles.
Upper Shaft Alarm Limit
HiPosAlr
Shaft position above which an alarm condition will be issued.
Lower Shaft Alarm Limit
LoPosAlr
Shaft position below which an alarm condition will be issued.
DRC Communications Rate
Com Rate
The serial communications rate on the DRC bus
Process Lower Engineering Units
PrLo Eng
Lower range value for the process transducer being used.
Process Upper Engineering Units
PrHi Eng
Upper range value for the process transducer being used.
Setpoint Lower Engineering Units
SpLo Eng
This is the lowest setpoint value. It must be within the limits of the process range.
Setpoint Upper Engineering Units
SpHi Eng
This is the highest setpoint value. It must be within the limits of the process range.
Default Parameters
Dflt Val
This variable allows the operator to set all parameters to their factory default values.
See paragraph 4.6.3 for more details.
Flow Control
Worcester Actuation Systems
4.7 Manual Setpoint Mode
Manual Setpoint Mode is used to override the electrical setpoint
input signal and establish a new setpoint. The mode is useful in
testing the controller at various setpoints without having external
equipment generate them. When the manual setpoint is set, it
will remain in effect until disabled or changed by an operator.
The setpoint state will be preserved even if power is removed.
So if the DRC is operating with a manual setpoint and power is
removed and reapplied, it will continue to control using the
manual setpoint.
4.7.1 Entering the Manual Setpoint Mode
In the Run Mode, press either the
key or the
key
until the mode display appears.
Press ENT to edit the value. It will start blinking the
current mode.
Press either
or
until MSET is visible.
With MSET blinking, press the ENT key to change to the
Manual Setpoint Mode.
If the security code is zero, no security code is needed to
enter the mode.
Otherwise, when prompted for the security code, press
ENT.
Press
and
to enter the correct security code then
press ENT to enter the mode.
If the incorrect security code is entered, the Manual
Setpoint Mode cannot be entered.
The Manual Setpoint Mode is exited by pressing the
key to return to the Run Mode.
4.7.2 Enabling, Disabling, and Changing the Setpoint
When the mode is entered, the display will alternate
between Man Setp and the setpoint value. If the manual
setpoint is disabled, the display will show Disabled as the
value.
To disable manual setpoint, simultaneously press both the
and
keys while the display is alternating Man Setp
and the setpoint value. The display will then indicate
Disabled as a value.
To enable manual setpoint or to change the value, press
ENT while the display is alternating Man Setp and the
setpoint value. The current setpoint value will begin
blinking. Press the
and
keys to change the setpoint
to the desired value. Note that the setpoint can only be
set in the range of the lower and upper setpoint values