Worcester actuation systems – Flowserve DRC-17 User Manual
Page 5
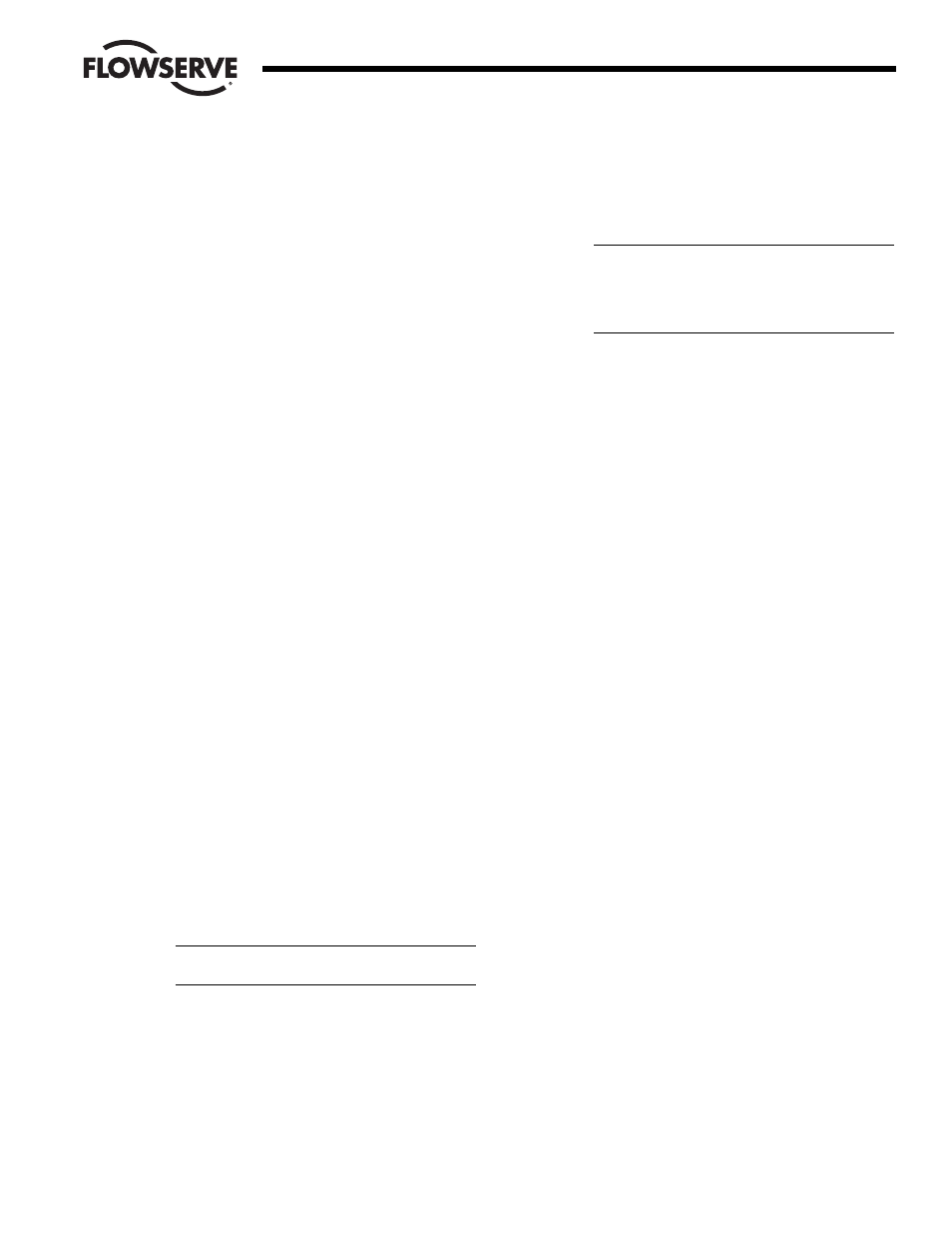
WCAIM2058
DataFlo Digital Electronic Remote Controller DRC17
5
2.2 Mounting Potentiometer:
2.2.1 Mounting Single Potentiometer into Series 75 Actuator
(See Figure 1.)
A. With the potentiometer mounted to the potentiometer
bracket and the spur gear loosely fitted to the
potentiometer shaft, mount the potentiometer bracket
(if not already mounted) as follows:
10-23 75 Actuator: Remove the motor module
mounting screws on the side of the module furthest
away from the actuator shaft. Position potentiometer
assembly bracket holes over screw holes and line up
potentiometer shaft with center of actuator shaft,
replace and tighten screws.
25/30 75 Actuator: Attach potentiometer bracket to
motor support plate between the terminal strip and
actuator shaft with mounting screws as shown in
Figure 1.
2.2.2 Mounting Optional Dual Potentiometer Into Series 75
Electric Actuator
A dual potentiometer is also available when external
resistance indication is also desired. A dual pot consists
of an “A” & “B” pot. The “A” pot is at the front, closest to
the bracket. The “B” pot is at the rear, away from the
bracket. Each pot can serve only one function.
Note: Voltage limit of “B” pot is 30 volts maximum.
Mount potentiometer per paragraph A of 2.2.1.
2.2.3 Potentiometer Wiring
Connect the single or “A” potentiometer leads to the
terminal strip per wiring diagram. For dual pot, “B” pot
must be wired directly to external device.
2.2.4 Adjusting Potentiometer
A. Reference part 6.1 for moving the actuator shaft
electrically.
B. 10-30 75 Actuator
Place the large face gear (12) over the actuator shaft
with the gear teeth down and secure with snap ring
(16) provided.
NOTE: The face gear utilizes a friction fit to the shaft.
For best results, wipe off any lubricant that may be on
the shaft before sliding on the face gear.
CAUTION: Do not overstretch the snap ring; use the
minimum opening to allow it to slip over the gear.
C. Adjust the potentiometer spur gear until there is
approximately
¹⁄₁₆" engagement with the large face
gear. Ensure there is minimum backlash between the
gears. Tighten the spur gear set screw.
D. Rotate the face gear back and forth to ensure smooth
and easy operation of the potentiometer.
E. IMPORTANT: For 90° Valves:
See paragraph 4.9.2 for feedback potentiometer
calibration procedure.
F.
The feedback potentiometer is now adjusted for use
in the 75 actuator. Add the potentiometer caution
label to the outside of the actuator cover.
CAUTION: If the actuator shaft is manually rotated a
multiple of 360° from its original position, the
feedback potentiometer will no longer be in
calibration. It must be recalibrated per paragraph
4.9.2, in order for the DRC to operate properly.
2.2.5 IMPORTANT
The feedback potentiometer is calibrated for only one 90
degree quadrant of valve operation.
If the valve and actuator output shaft is repositioned to
another 90 degree quadrant the feedback potentiometer
must be recalibrated as per paragraph 2.2.4.
The Series 75 actuators offer a manual override feature.
Whenever repositioning the valve using this manual
override capability on these actuators, move the valve
only within the 90 degrees for which the feedback
potentiometer has been calibrated.
2.3 Mounting Circuit Board
2.3.1 For 120/240 VAC 10-23 Size Electric Actuators
(See Figure 2.)
A. Mount the brackets to the actuator motors or spacers
as provided. The longer bracket is mounted to the
right side of the actuator (when facing the terminal
strip using the motor mounting screws).
B. Remove and replace motor screws carefully to avoid
stripping the threads of these self-tapping screws.
C. Once these motor screws and brackets are firmly
secured, firmly tap the motor stator to force
realignment of the top motor bearing.
D. Loosen all actuator terminal strip screws necessary to
connect the circuit board’s wiring to the terminal strip.
See manual section 3.0 for proper wiring of circuit
board to the actuator’s terminal strip. Wire routing is
important. Ensure that the wiring is not pinched and is
not near cams or mechanical brake (if installed).
E. Assemble circuit board into actuator. Slide rubber
grommets onto insulating board. Put nylon washer
under heads of self-tapping screws. (Four screws will
be used to install the circuit board onto the brackets).
F.
Place circuit board over brackets. See Figure 2.
Loosely fasten board to brackets using mounting
screws.
G. The circuit board is wired to the terminal strip as
shown in section 3.0.
H. Snug down the circuit board and secure mounting
screws such that grommets are about half
compressed.
Flow Control
Worcester Actuation Systems