Isolated 22 v supply, 15 v igbt gate drive supply, 3 v and 5 v logic supplies – Altera Multiaxis Motor Control Board User Manual
Page 7: 3 v isolator supply, Encoder power supplies, Brake
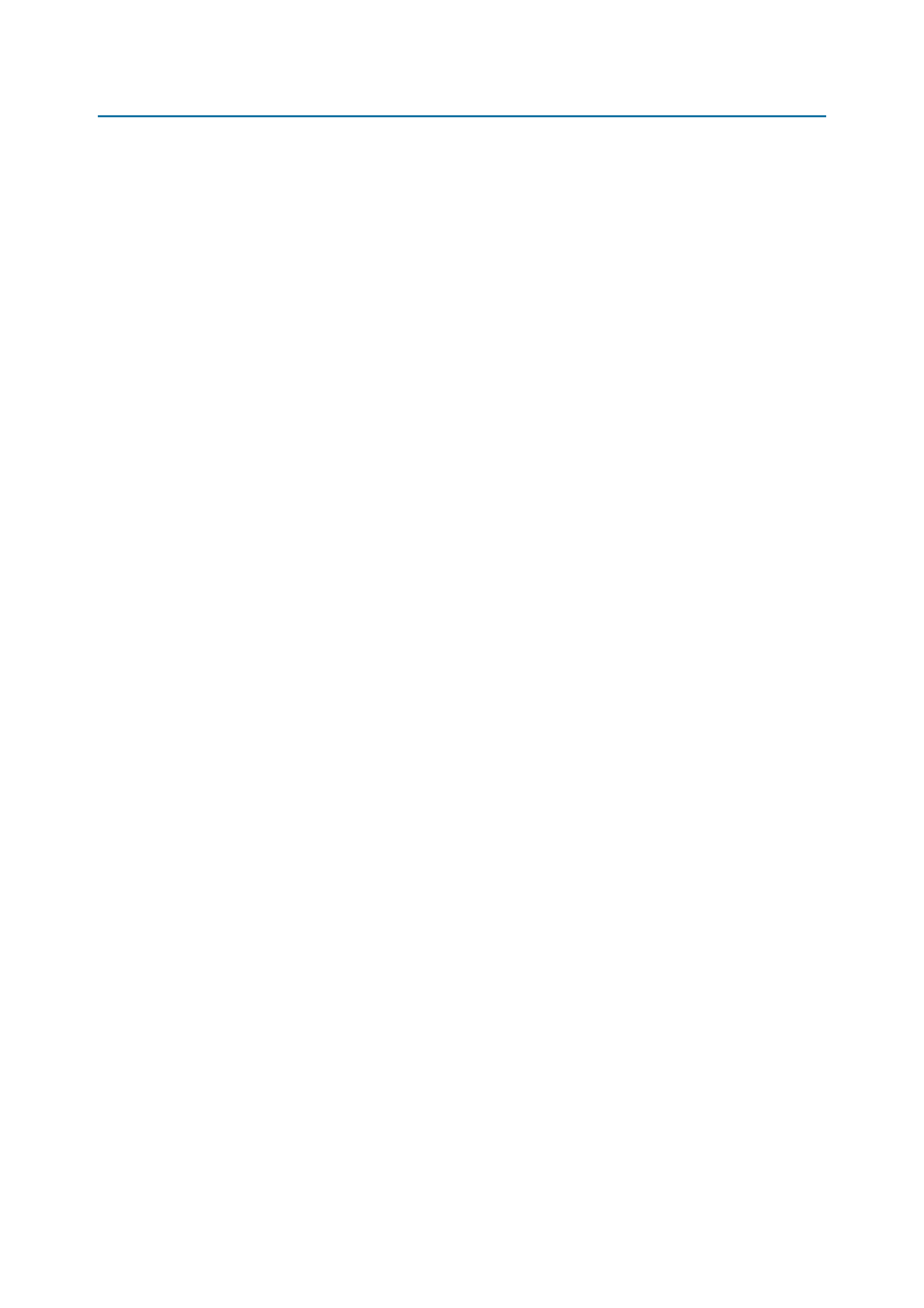
Functional Description
Page 7
Multiaxis Motor Control Board
February 2014
Altera Corporation
The DC link can supply up to 1.5 kW in total, across all four motor channels with a
mains input of 240 V. At lower mains voltages, the Multiaxis Motor Control Board
reduces the maximum power. For example, 1 kW at 110 V input. Isolated sigma-delta
ADCs allow you to monitor the DC link voltage and current.
Isolated 22 V Supply
A Linear Technology LT3798 provides an isolated 22-V supply that feeds further
switch mode regulators to generate all of the required voltages on the Multiaxis Motor
Control Board.
15 V IGBT Gate Drive Supply
Two Linear Technology LTC3631EDD#PBF generate the 15-V supplies that the IGBT
modules require. One LTC361 supplies motor channels 0 and 1; the other one supplies
motor channels 2 and 3.
3.3 V and 5 V Logic Supplies
The 3.3-V and 5-V supplies for logic devices both use Linear Technology LTM8022
DC/DC micromodules.
3.3 V Isolator Supply
The isolators connected to the HSMC connector can receive power directly from the
HSMC 3.3-V pins or from the HSMC 12-V pin via a Linear Technology LTM8022
micromodule switch mode power supply.
Encoder Power Supplies
Each motor channel includes a power supply (LTM8025 micromodule) for the
encoder interface that you can configure for 3.3 V, 5 V, or 12 V as required by the
encoder.
Brake
The Multiaxis Motor Control Board includes incorporates a brake circuit with a
Fairchild FAN3111E gate driver, Fairchild FGP15N60 IGBT, and 100-Ohm brake
resistor.
During braking, the kinetic energy of the motor feeds back into the DC link circuit as
extra stored energy in the DC link capacitor. You can turn on the brake resistor to
dissipate excess energy and prevent the DC link voltage from rising too high.
The peak power dissipation in the brake resistor is:
V
2
/R = V
DCLINK
2
/100 = 1.6 kW
As the brake resistor is rated for only 20 W continuous power dissipation, only use it
for only a few milliseconds. The gate drive to the brake circuit is AC coupled.The
FPGA must drive a square wave on the HSMC_MOTOR_BRAKE signal to activate the brake.
A steady signal, either high or low, results in the Power Supply turning off the brake.
Furthermore, the FPGA should implement some form of time out to prevent you from
activating the brake for too long.