Vectronics VEC-1500K User Manual
Page 15
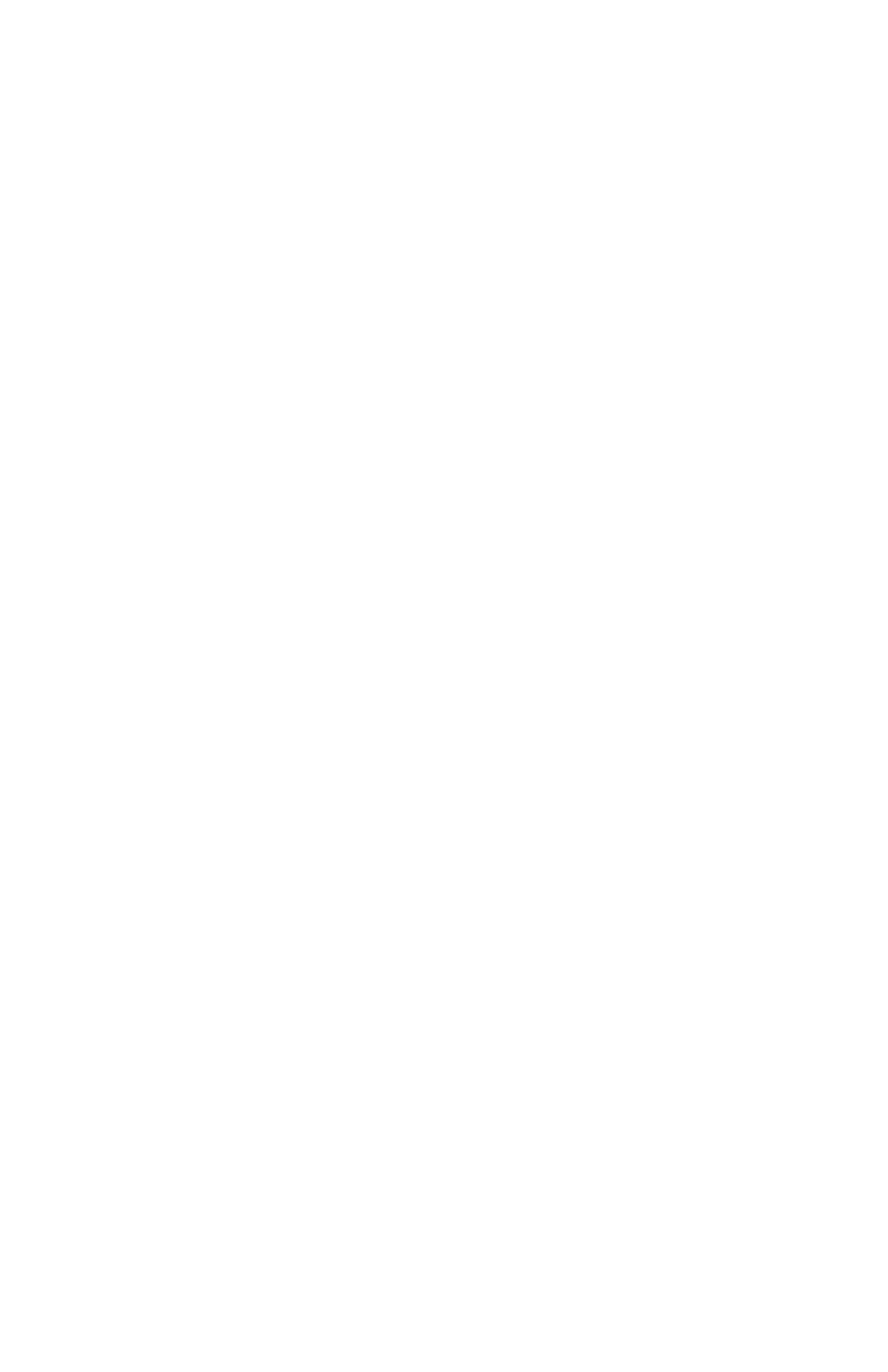
10
Purchasing and Using Solder--A Quick Review
By now, you're probably getting the idea that "grabbing any old roll of solder" to
do a job might not yield the best results! Before you select a product, ask
yourself the following questions:
1. Is the solder alloy right for the job?
2. Is the wire size matched to the task (too small, to big)?
3. Is the core type acceptable (single, multi, or solid?)
4. Is the core size going to deliver the right amount of flux?
5. Is the type of flux right for the application?
6. Is supplemental flux needed?
7. Will the flux residue require removal?
8. If so, what type of cleaning product is best?
You probably won't always be able to find exactly what you want! However, if
you understand solder specification and what they mean, substitution should be
easy. For example, for most routine PC board hand-soldering jobs, a 60/40 alloy
in a .031" or .040" wire size with a 3.3% (regular) RA flux core works well.
From that starting point, you can add other solders to accommodate specific
tasks. For example, a 63/37 alloy in a .020" wire size with 3.3% RA (or "no-
clean") flux works well for surface-mount applications. And, a roll of "fat"
60/40 might come in handy for assembling high-power equipment with large
components.
When forced to use "SE" (or someone else's) solder, always read the label first!
If the flux is unaggressive or the core size "small", use supplemental flux
(usually RA). If the flux is highly-activated RA or water-soluble, remove the
residue afterward. Finally, if it's acid core or the roll's unmarked, put it back and
find something else. It always pays to be an informed consumer!