Vectronics VEC-1500K User Manual
Page 8
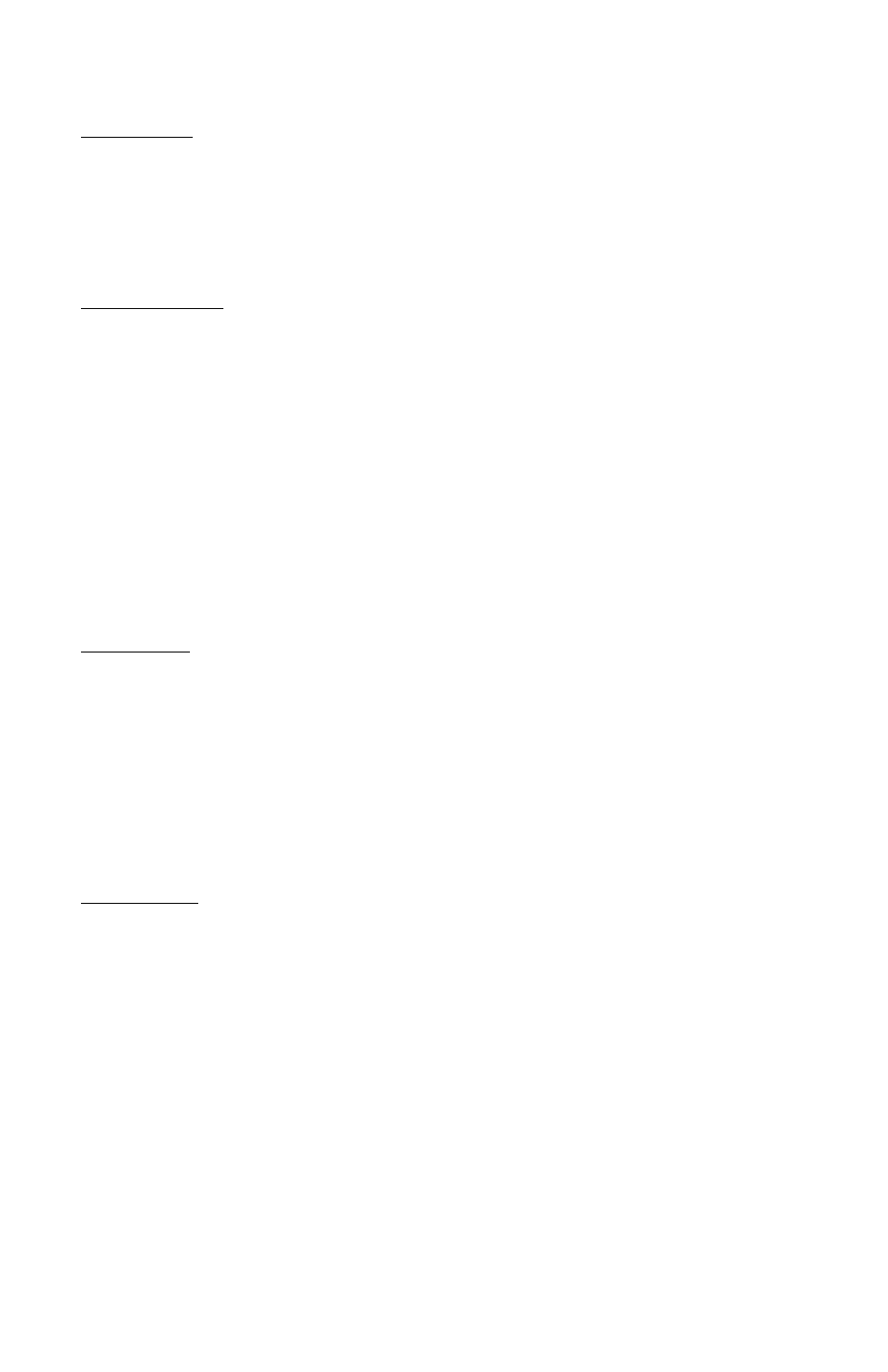
3
Plastic State: As solder begins to "melt", it first changes into a pasty, unstable,
soft material. If a cooling solder joint is vibrated or moved while in the plastic
state, the resulting connection will appear dull, grainy, and the joint may
fracture. To prevent fractures, most electronic solders are specially formulated
to minimize their "plastic-state" temperature range. This makes the transition
from a liquid to a solid more rapid.
Liquidous State: As temperature rises, solder changes from a plastic paste to a
thick, syrupy, molten liquid. This is called the liquidous state. When solder is in
the liquidous state, it can flow, "wet", and adhere to many electrically conductive
metals such a copper, tin, silver, and brass. However, electronic solders don't
adhere to all conductive metals. It won't stick to aluminum, for example. The
metals it adheres to are called solderable metals.
Composition of Solder Alloys:
We've said that most solder alloys consist of
near-equal mixtures of tin and lead.
Normally, pure tin melts at 450-degrees F
and pure lead melts at 621 degrees F. However, when we combine the two into
an alloy, the melting point becomes lower. The actual temperature depends
upon percentage of tin to lead--as measured by weight. The two alloys used
most commonly for electronic solder are:
60/40 Alloy: Solder containing 60% tin and 40% lead begins to melt at around
374 degrees F with a plastic range of 13 degrees F. This mix provides a
relatively low melting point, which helps to limit thermal stress on sensitive
electronic components. The 60/40 alloy also provides superior wetting on
solderable metals. "Wetting" refers to liquidous solder's ability to spread over
the surface of another metal and adhere to it. In addition to superior wetting,
60/40 solder has a moderate ability to bridge short gaps between metal surfaces.
"Gapping" is especially useful for assembly jobs where contact between
conductive surfaces may be loose or incomplete.
63/37 Solder: Solder containing a mixture of 63% tin and 37% lead begins to
melt at around 364 degrees F--slightly lower than the 60/40 alloy. The 63/37
alloy is unique because it has an extremely narrow plastic-state temperature
range--only a degree or two. Because of this characteristic, the transition from a
liquidous state to a solid state is virtually instantaneous. Alloys that "set" this
quickly during cooling are called eutectic (you-tech-tic) solders. The 63/37 alloy
exhibits less gapping and less movement from contraction during cooling.
Both alloys are extremely popular for general-purpose hand soldering. The
60/40 alloy generally works better for single-sided circuit board assembly, hand-
wiring, larger connector installations, and any other application where superior
wetting or moderate gapping is beneficial. The 63/37 alloy works better for
assembling crowded multi-layer PC boards and for making surface-mount
repairs. These are applications where gapping could cause unwanted short-