Ks s φ, 3 liquid flow sensors, 1) the µ-flow model for flowrates up to 2 g/h – Bronkhorst IN-FLOW User Manual
Page 12
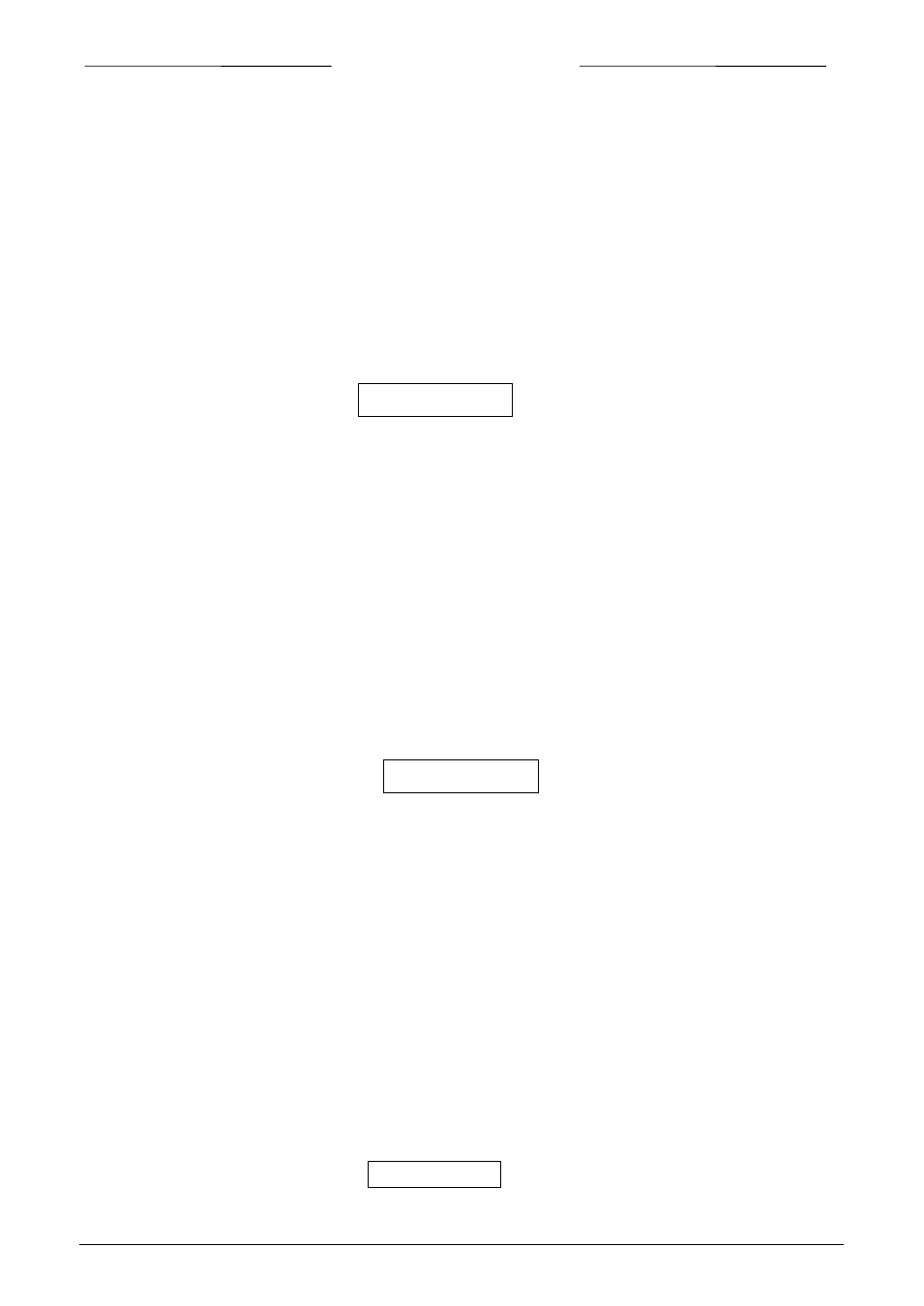
BRONKHORST HIGH-TECH B.V.
page 12
9.17.022
1.2
Sensor principles
1.2.1 Gas flow sensors (by-pass measurement)
The majority of gas flow sensors operate according to the by-pass measurement principle. These types of
instruments operate on a principle of heat transfer by sensing the delta-T along a heated section of a capillary
tube. Part of the total flow is forced through the capillary by means of a laminar flow device in the main
stream generating a delta-p.
The design of the laminar flow device is such that flow conditions in both the capillary and laminar flow device
are comparable, thereby resulting in proportional flow rates through the meter. The delta-T sensed by the
upstream and downstream temperature sensors on the capillary depends on the amount of heat absorbed by
the gas flow.
The transfer function between gas mass flow and signal can be described by the equation:
V
signal
= output signal
c
p
= specific heat
V
K c
signal
p
m
= ⋅
⋅ Φ
K
= constant factor
Φ
m
= mass flow
The temperature sensors are part of a bridge circuit and the inbalance is linearised and amplified to the
desired signal level.
1.2.2 Gas flow sensors (direct mass flow measurement, CTA based)
The IN-FLOW CTA models operate on the principle of direct thermal mass flow measurement. The thru-flow
design sensor consists of a heater resistor and a temperature sensing resistor. Both resistors are made of
temperature sensitive resistive material that is covered with a stainless steel tube. The heating power
required to keep the temperature difference between the heater resistor and the sensing resistor at a
constant level is proportional to the mass flow. A different and unique heater current is produced for each
value of the flow. The measurement principle described is called Constant Temperature Anemometry (CTA).
The transfer function between mass flow and output signal can be described by the equation:
n
m
signal
K
S
S
Φ
⋅
+
≅
0
S
signal
= output signal
S
0
= offset (zero flow) signal
K
= constant factor (includes λ – heat conductivity, C
p
– specific heat, μ – dynamic viscosity and ρ –
density of the gas)
Φ
m
= mass flow
n
= dimensionless constant (typically of order 0.5)
1.2.3 Liquid flow sensors
Two digital-liquid flow measurements and two sensor arrangements can be distinguished. They have in
common that there is no bypass system involved, which means that they are of the type: “thru flow”. The
following sensor arrangements can be distinguished:
1) The µ-FLOW model for flowrates up to 2 g/h.
Basically this is a small capillary tube with two sensing elements placed on the tube. The two elements both
serve as heater as well as temperature sensing elements. The delta-T sensed by the upstream and
downstream temperature sensors on the capillary depends on the amount of heat absorbed by the mass of
the liquid. The temperature sensors are part of a bridge circuit and the unbalance is amplified to the desired
signal level. The transfer function between liquid mass flow and signal can be described by the equation:
V
signal
= output signal
c
p
= specific heat
V
K c
signal
p
m
= ⋅
⋅ Φ
K
= constant factor
Φ
m
= mass flow