7 piping, 8 electrical connections, 9 caution – Bronkhorst IN-FLOW User Manual
Page 22
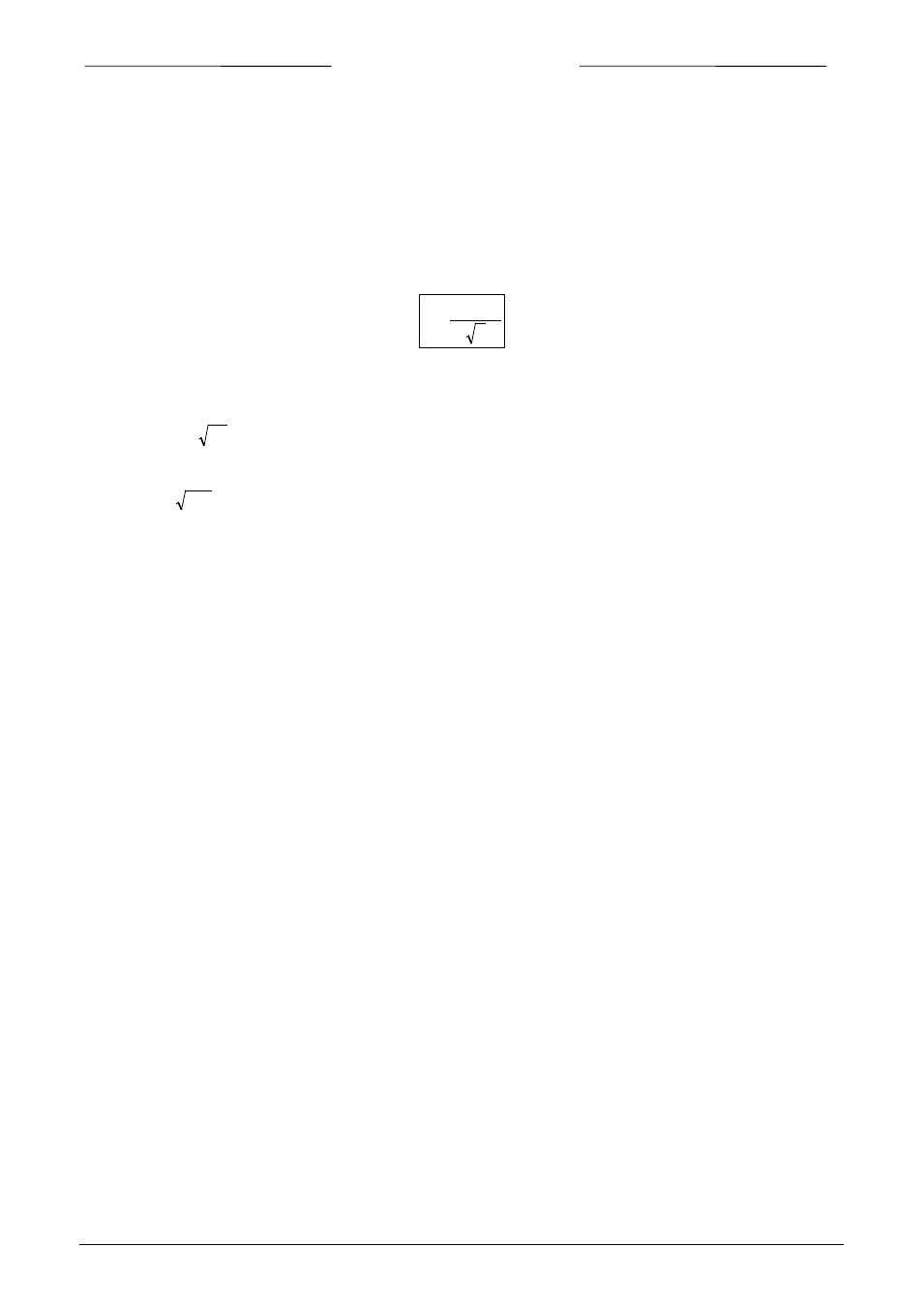
BRONKHORST HIGH-TECH B.V.
page 22
9.17.022
2.7
Piping
BE SURE THAT PIPING IS ABSOLUTELY CLEAN!
DO NOT install small diameter piping on high flowrates, because the inlet jetflow will affect the accuracy.
DO NOT mount abrupt angles direct on in- and outlet, especially not on high flowrates. We recommend at
least 10 pipe diameters distance between the angle and the instrument.
DO NOT mount pressure regulators direct on the inlet of gas flow meters/controllers, but allow some meters
of piping (at least 25 D). Special attention should be taken at high flow rates with flow controllers. An up- and
downstream buffer is needed with a volume calculated according to the following formula:
V
d
≥ 015
2
,
ρ
in which:
V = Volume in litres
d = orifice diameter in mm
ρ
= density at normal conditions
d = 7,6 k
v
Example:
Flow controller at 500 l
n
/min Air and orifice diameter d = 4 mm, needs for stable control a buffer volume of:
V ≥
⋅
=
015 4
129 21
2
,
: ,
,
litres
Also the capacity of the pressure regulator should be at least 2 times the flow controller, so in this case
2 ⋅ 500 = 1,000 l
n
/min.
2.8
Electrical connections
Bronkhorst High-Tech B.V. recommends to use their standard cables. These cables have the right
connectors and if loose ends are used, these will be marked to prevent wrong connection.
Hook-up diagrams are enclosed in the back of this manual.
To comply with the IP classification it is necessary to follow the assemble guidelines of the connector
manufacturer.
2.9
Caution
Each meter/controller is pressure tested to at least 1.5 times the working pressure of the process
conditions stipulated by the customer, with a minimum of 8 bar.
For pressure meter/controllers. The test pressure depends on the range of the pressure transducer.
In general 2 x F.S. value for ranges 1 and 2 bar
1.5 x F.S. value for ranges up to 200 bar
1.25 x F.S. value for ranges up to 400 bar
The tested pressure is stated on the flow meter/controller with a RED COLOURED sticker. Check test
pressure before installing in the line.
If the sticker is
not available or the test pressure is incorrect, the instrument should not be mounted in the
process line and be returned to the factory.
Each instrument is helium leak tested to at least 2⋅10
-9
mbar l/s Helium.