Design of major parts, Performance and operating limits, Design of major parts (3.3) – Flowserve Durco Mark 3 ISO Frame Mounted User Manual
Page 12: Operating limits (3.4.1), Performance (3.4)
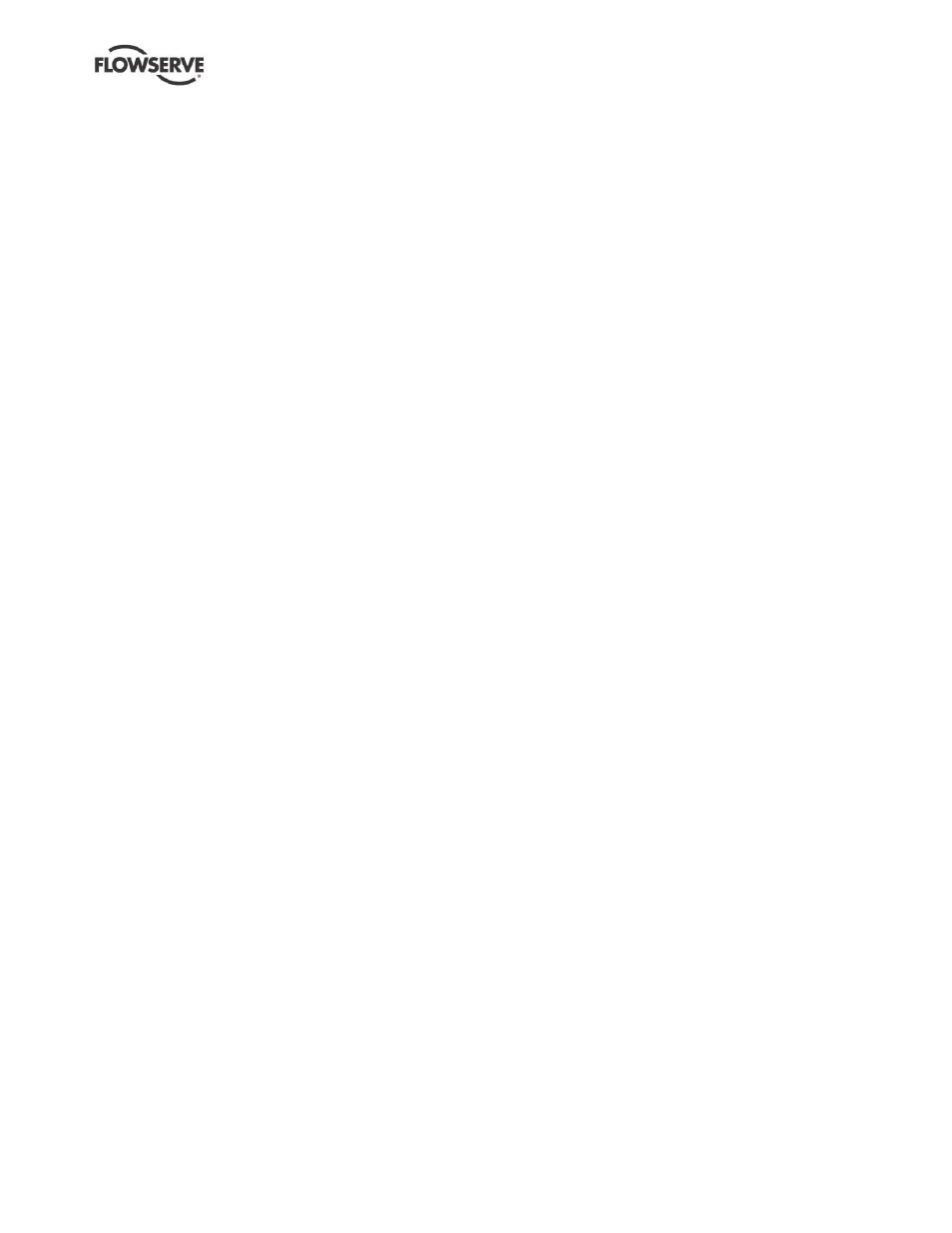
DURCO MARK 3 ISO FRAME MOUNTED ENGLISH 85392719 12-14
Page 12 of 52
flowserve.com
The typical nomenclature above is the general guide
to the Durco Mark 3 ISO configuration description.
Identify the actual pump size and serial number from
the pump nameplate. Check that this agrees with the
applicable certification provided.
3.3
Design of major parts
3.3.1
Pump casing
The pump casing is designed with a horizontal
centerline end inlet and a vertical centerline top outlet
that makes it self-venting.
In addition, the P self-priming pump casing is
designed with a self-priming action which works on
the reflux principle for suction lifts up to 7 m (23 ft).
For ease of maintenance, the pump is constructed so
that pipe connectors do not have to be disturbed
when internal maintenance is required.
Casing feet pads are provided underneath the casing
except on the N casing where they are on the shaft
centerline.
3.3.2
Impeller
Depending on the product, the impeller is either reverse
vane or open. (
On the R impeller it is recessed into
the back of the casing.)
Impeller locking
3.3.2.1
Most A-OP type impellers are available with the
option of key drive impeller. Most RV type impellers
are available with the option of an impeller locking
screw to provide an additional protection from
loosening of the impeller during a reverse run.
3.3.3
Shaft
The large diameter stiff shaft, mounted on bearings,
has a keyed drive end.
3.3.4
Bearing housing
The bearing housing enables adjustment of impeller
face clearance via the bearing carrier micrometer
mechanism.
3.3.5
Pump bearings and lubrication
The pump is fitted with ball and or roller type bearings
which may be configured differently dependent on
use. The bearings may be oil or grease lubricated.
3.3.6
Adaptor
The pump is fitted with an adaptor between bearing
housing and cover for optimum interchangeability.
3.3.7
Cover (seal chamber)
The cover has spigots between the pump casing and
bearing housing for optimum concentricity.
A fully confined gasket forms the seal between the
pump casing and the cover.
The cover designs provide improved performance of
mechanical seals.
The design enables one of a number of sealing
options to be fitted.
3.3.8
Shaft seal
The mechanical seal(s) attached to the drive shaft
seals the pumped liquid from the environment. Gland
packing may be fitted as an option, except on the P
self-primer casing.
3.3.9
Driver
The driver is normally an electric motor. Different drive
configurations may be fitted such as internal combustion
engines, turbines, hydraulic motors, and driving via
couplings, belts, gearboxes, drive shafts etc.
3.3.10
IPS Beacon
The pump is fitted with a temperature and vibration
monitor as standard. For additional information see
the IPS Beacon User Instructions (26999949) which
are supplied separately.
3.3.11
Accessories
Accessories may be fitted when specified by the
customer.
Fan cooling is available for high temperature operation.
(This is a fan fitted within the coupling guard to blow
cooling air over the bearing housing and shaft.)
3.4
Performance and operating limits
This product has been selected to meet the
specifications of the purchase order. See section 1.5.
The following data is included as additional
information to help with your installation. It is typical,
and factors such as temperature, materials, and seal
type may influence this data. If required, a definitive
statement for your particular application can be
obtained from Flowserve.
3.4.1
Operating limits
Normal maximum ambient temperature:
+40 ºC (104 ºF).
Normal minimum ambient temperature:
-20 ºC (-4 ºF).
Maximum pump speed: refer to the nameplate.