Performance and operating limits, Installation (4), Operating limits (3.4.1) – Flowserve IDP CPXV User Manual
Page 12
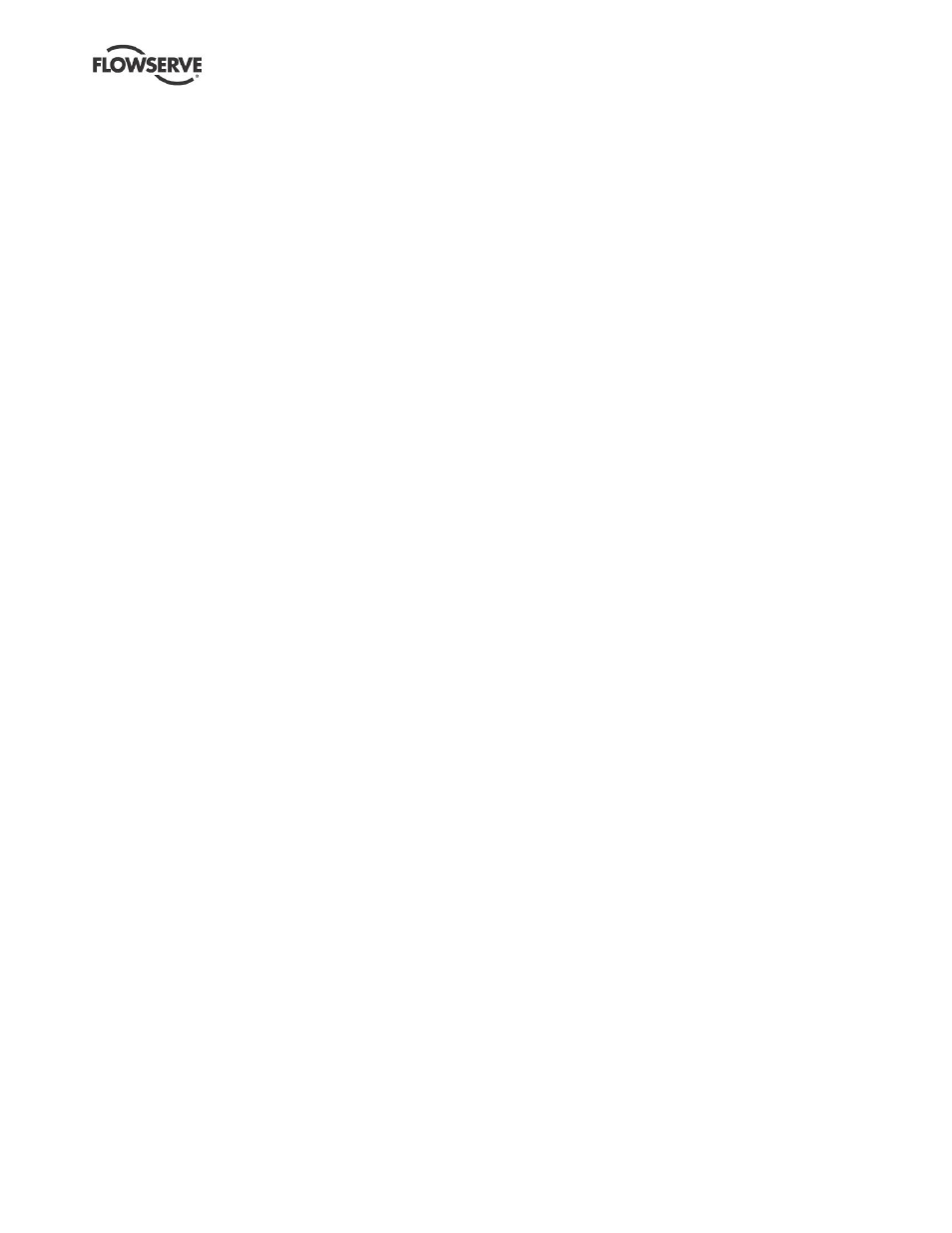
CPXV and CPXRV USER INSTRUCTIONS ENGLISH 71569193 09-14
Page 12 of 48
flowserve.com
High temperature pumps have a cooling fan above the
pump thrust bearing housing and a heat sink disk fan
below the pump thrust bearing but above the sole
plate shaft seal.
3.3.5
Pump bearings and lubrication
The pump is fitted with a thrust type ball bearing that
may be configured differently dependent on use.
The thrust bearing(s) may be grease or oil lubricated
depending upon the application.
The journal (line) bearings may be lubricated by
product or from an external source depending upon
the application.
3.3.6
Sole plate shaft seal
The modular design enables one of a number of
sealing options to be fitted. The option of a rigid
coupling below the thrust bearing and above a
mechanical seal provides back-pull-out servicing of
the mechanical seal; removing the motor extends the
back-pull-out feature to the thrust bearing.
3.3.7
Driver
The pump is normally driven by a flange mounted electric
motor. An air or hydraulic motor may be utilized.
The position of the terminal box can be changed by
rotating the complete motor. To do this, remove the
fasteners from the motor flange, rotate the motor and
re-fit the fasteners.
3.3.8
Accessories
Accessories may be fitted when specified by the
customer.
3.4 Performance and operating limits
This product has been selected to meet the
specifications of the purchase order. See section 1.5.
The following data is included as additional information to
help with your installation. It is typical, and factors such
as temperature, materials, and seal type may influence
this data. If required, a definitive statement for your
particular application can be obtained from Flowserve.
3.4.1
Operating limits
Maximum pump ambient temperature: +55 ºC (131 ºF)
where driver, flexible coupling and thrust bearing is also
rated for this ambient. Check the nameplate.
Maximum pump speed: refer to the nameplate.
3.4.2
Energy efficiency operation of pumps
The pump supplied will have been selected from
Flowserve’s extensive product line to have optimum
efficiency for the application. If supplied with an electric
motor then the motor will meet or exceed current
legislation for motor efficiency. However it is the way
the pump is operated which has the greatest impact on
the amount and cost of energy used during the
operating life of the pump. The following are key points
in achieving minimum operating cost for the equipment:
Design the pipe system for minimum friction losses
Ensure that the control system switches off the
pump when not required
In a multi-pump system run the minimum number
of pumps
Try to avoid systems which by-pass excess flow
As far as possible avoid controlling pump flow by
throttle valves
When commissioned, check that the pump
operates at the duty specified to Flowserve
If it has been found that the pump head and flow
exceed that required, trim the pump impeller
diameter
Ensure that the pump is operating with sufficient
NPSH available
Use variable speed drives for systems that
require variable flow. A VFD for an induction
motor is a particularly effective way of achieving
speed variation and energy/cost reduction
Notes for VFD usage:
o make sure that the motor is compatible with
VFD
o Do not over-speed the pump without
checking the power capability with Flowserve
o On systems with high static head, speed
reduction is limited. Avoid running the pump
at a speed which gives low or zero flow
o Do not run a low speed and flow rate that lets
solids settle out of suspension in the pipework
o Do not use a VFD for a fixed flow
requirement; it will introduce power losses
Select high efficiency motors
If replacing a standard motor with a high
efficiency motor it will run faster and the pump
could take more power. Reduce the impeller
diameter to achieve energy reduction
If the pump system pipework or equipment is
changed or process duty is changed, check that
the pump is still correctly sized
Periodically check that the pipe system has not
become corroded or blocked
Periodically check that the pump is operating at
the flow, head and power expected and that the
efficiency has not reduced with erosion or
corrosion damage