Installation, Location, Part assemblies – Flowserve IDP CPXV User Manual
Page 13: Foundation, Grouting, Piping, Foundation (4.3), Grouting (4.4), Location (4.1), Part assemblies (4.2)
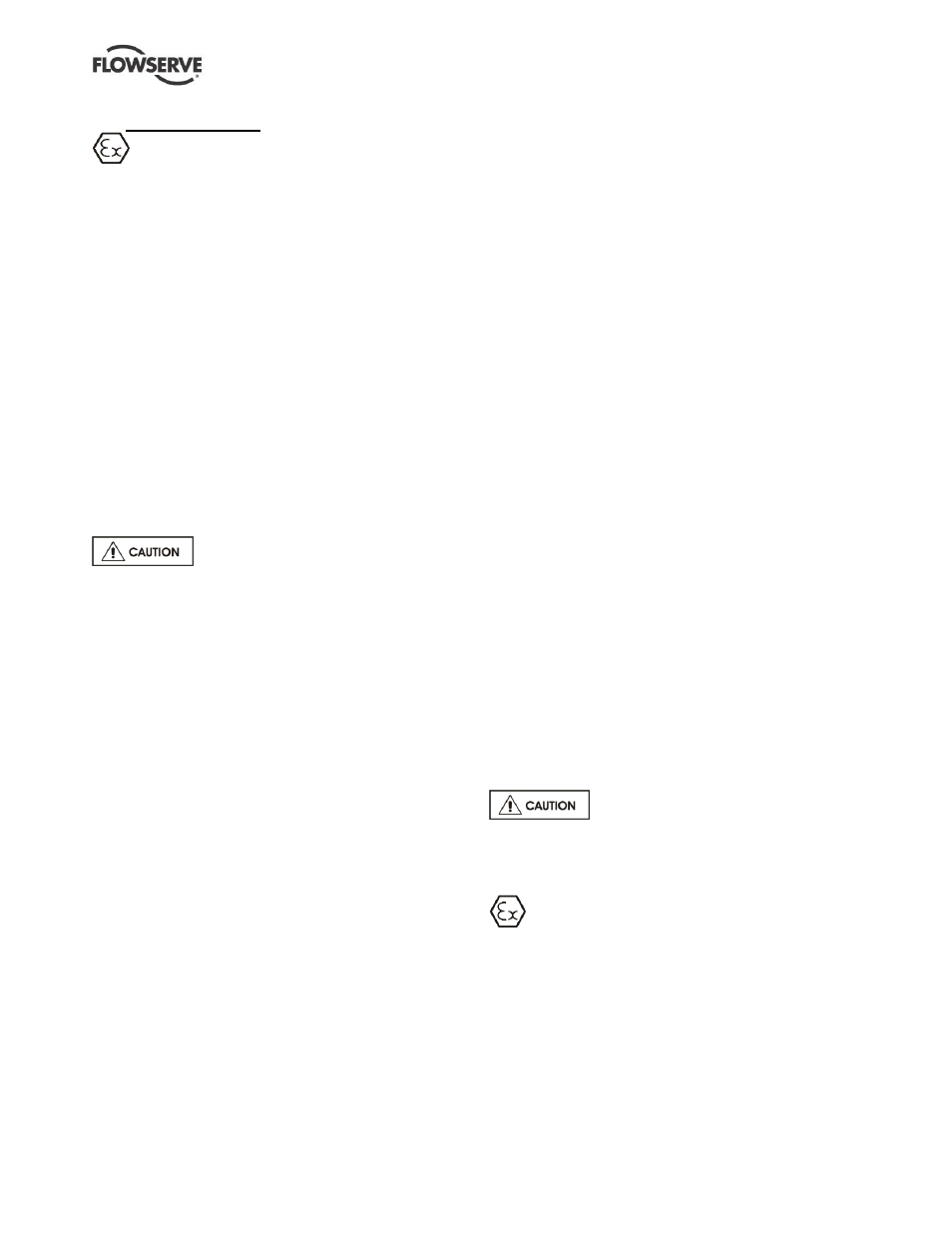
CPXV and CPXRV USER INSTRUCTIONS ENGLISH 71569193 09-14
Page 13 of 48
flowserve.com
4
INSTALLATION
Equipment operated in hazardous locations
must comply with the relevant explosion protection
regulations. See section 1.6.4, Products used in
potentially explosive atmospheres.
4.1 Location
The pump should be located to allow room for
access, ventilation, maintenance and inspection with
ample headroom for lifting and should be as close as
practicable to the supply of liquid to be pumped.
Refer to the general arrangement drawing for the
pump set.
4.2 Part assemblies
On pump sets the coupling elements are supplied
loose. It is the responsibility of the installer to ensure
that the pump set is finally lined up and checked as
detailed in section 4.5.5, Final checks.
4.3 Foundation
There are many methods of installing
pump units to their foundations. The correct method
depends on the size of the pump unit, its location and
noise and vibration limitations. Non-compliance with
the provision of correct foundation and installation
may lead to failure of the pump and, as such, would
be outside the terms of the warranty.
The pump mounting should have concrete or metal to
support it around its edges.
4.3.1
Levelling
The sole plate must be level so that the pump column
hangs vertically; confirmed by inspection. With the
motor removed check the top face of the machined
motor pedestal [3160] is set level to 0.05 mm (0.002 in.)
or 0.2 mm/m (0.0025 in./ft) maximum. The optional
base plate should be levelled and grouted first.
Larger size motors are shipped unfitted. The motor will
need to be fitted after completion of the pump
foundation installation. Turn shaft clockwise by hand to
ensure it is free to turn.
4.3.2
Packing pieces
Where the sole plate and its counter-face do not each
have a machined face, packing pieces (metallic shims)
will need to be placed evenly adjacent to the foundation
(holding down) bolts to avoid “soft-foot” distortion. Turn
shaft clockwise by hand to ensure it is free to turn.
Soft-foot distortion may significantly increase vibration
and damage equipment by causing distortion and
should normally be inspected. If high vibration occurs
when pump is run (see section 5, Commissioning, start-
up, operation and shutdown) place a vibration meter at
the side of the motor as soft-foot is most effectively
reduced when the vibration is reduced to a minimum.
Overall vibration measurement can be used - it is not
necessary to use a vibration spectrum to pick up soft-
foot which occurs at 1x running speed and should be
the first issue to check.
To adjust for soft-foot use a dial gauge on the sole
plate top face near to the holding down bolt, zero it,
record the soft-foot spring in the sole plate and undo
one holding down bolt at a time.
Soft-foot is removed by inserting packing pieces
(metallic shims) equal to or slightly less than the soft-
foot spring amount recorded at the individual holding
down point locations. Re-torque the holding down bolt.
Continue this procedure for each holding down bolt
position in turn, one at a time. The thickness of
packing pieces (metallic shims) adjacent to an
individual holding down bolt should not exceed 3 mm
(0.12 in.); ie soft-foot spring is not to exceed 3 mm
(0.12 in.) at any individual location.
4.4 Grouting
Where applicable, grout in the foundation bolts.
Grouting provides solid contact between the pump unit
and foundation, prevents lateral movement of vibrating
equipment and dampens resonant vibrations.
4.5 Piping
Protective covers are fitted to the pipe
connections to prevent foreign bodies entering during
transportation and installation. Ensure that these
covers are removed from the pump before connecting
any pipes.
If sludge and debris can build up in the sump it
is recommended to use a strainer with a maximum
opening size of 6 mm (0.024 in.) and a free surface
area greater than three times the pump suction area.
Category 1/2 and 1/3 pumps must be fitted with a
strainer.