Flowserve HED Worthington User Manual
Page 15
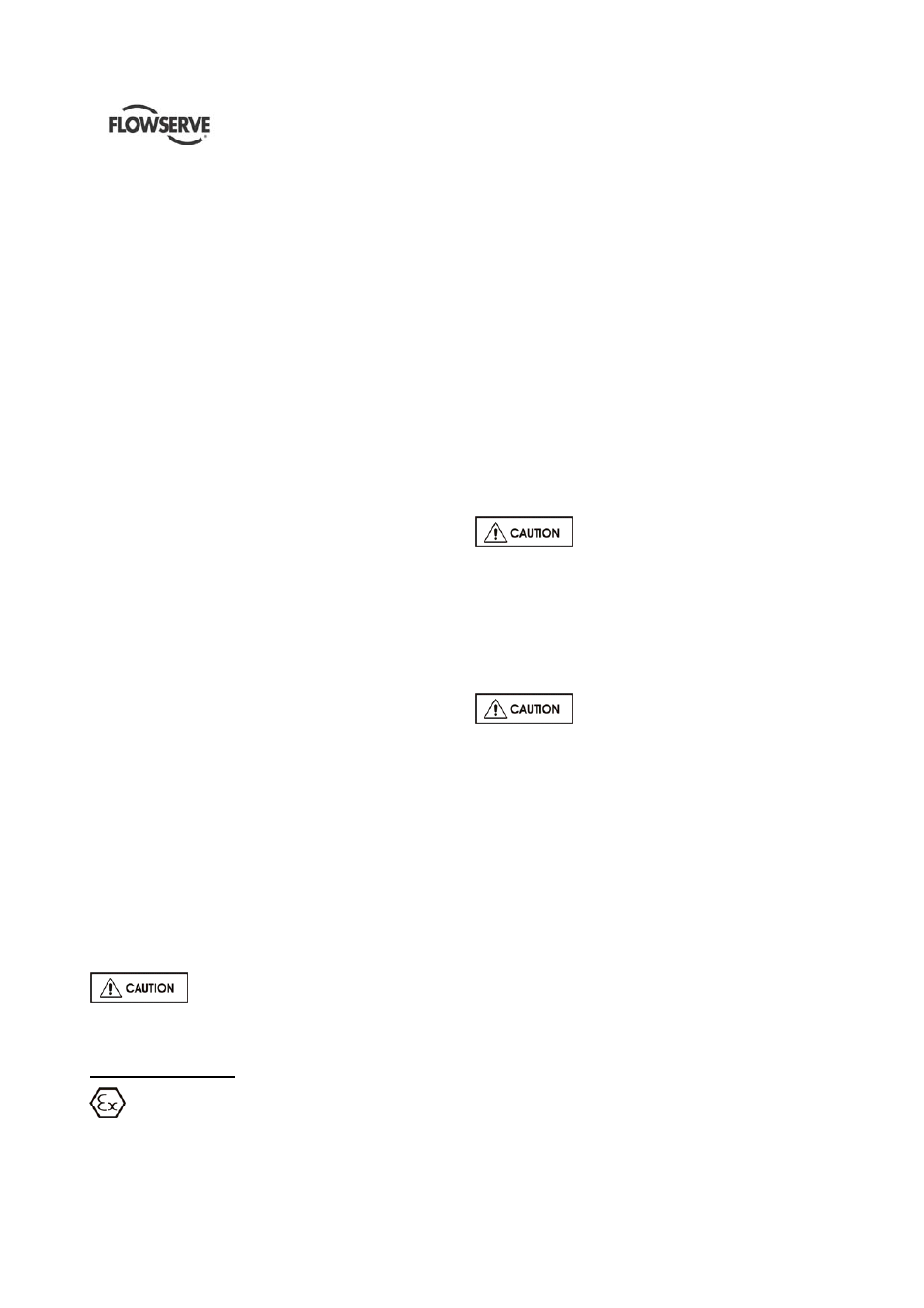
HED/HED-DS USER INSTRUCTIONS ENGLISH 85392695 – 06/14
Page 15 of 64
If any change in NPSH
A
is proposed, ensure its
margin over NPSH
R
is not significantly eroded. Refer
to the pump performance curve to determine exact
requirements particularly if flow has changed. If in
doubt please consult your nearest Flowserve office
for advice and details of the minimum allowable
margin for your application.
3.4.5 Minimum Continuous Stable Flow
The Minimum Continuous Stable Flow for the pump is
stated on the Data sheet.
3.4.6 Minimum flow control
In all cases, it is the customer's responsibility to
supply a system and/or control which assures that
any pump within a system is not operated below its
minimum flow condition.
In many cases, this is not a problem because the
system is operating within its own flow range to
assure product delivery. A simple high pressure
alarm, shut down and/or bypass control can be used.
However, in systems where product demand has high
swings or where more than 100% capacity units are
desired to support a product system, additional care
must be taken.
3.4.7 Thermal control
A thermal control of the unit can be provided by
thermal sensors which read direct or "related to" fluid
temperatures and respond accordingly by opening
additional flow paths until the given unit re-
establishes the acceptable temperature rise, and sets
off alarms if not achieved within reasonable/normal
time periods. (High limit could actually shut down
unit).
3.4.8 Pressure and/or Flow Control
Pressure and/or flow sensors can be used to hold the
unit at higher flows by opening additional flow paths
once a "high pressure limit" or " low flow limit" was
indicated.
Upon system reaching increased flow a "low pressure
limit" or "high flow limit" setting would close the
bypass flow path. Care must be taken to allow for
signal spread to avoid cyclic conditions.
3.4.9 Operating at Reduced Capacity
Damage to pump may result from
prolonged operations at capacities less than MCSF
as stated in Data Sheet.
4 INSTALLATION
Equipment operated in hazardous locations
must comply with the relevant explosion protection
regulations. See section 1.6.4, Products used in
potentially explosive atmospheres.
4.1 Location
The pump should always be located as near as
possible to the suction supply.
Install the unit close to the source of the liquid to be
pumped. It is desired to simplify the suction and
discharge piping layout. When selecting the location,
be sure to allow adequate space for operation as well
as for maintenance operations involving dismantling
and inspections of parts.
Head room is an important consideration as an
overhead lift of some type is required
4.2 Part assemblies
Motors may be supplied loose. It is the responsibility
of the installer to ensure that the motor is assembled
to the pump and lined up as detailed in section 4.5.2.
Prior to grouting, an initial alignment
check in accordance with the alignment section of
this document shall be performed to verify that
coupling spacing and final alignment can be achieved
without modifying the hold down bolts or the machine
feet. This is necessary to ensure that the baseplate
was not damaged during the transportation.
4.3 Foundation
There are many methods of installing
pump units to their foundations. The correct method
depends on the size of the pump unit, its location and
noise vibration limitations. Non-compliance with the
provision of correct foundation and installation may
lead to failure of the pump and, as such, would be
outside the terms of the warranty.
The foundation should be sufficiently rigid and
substantial to prevent any pump vibration and to
permanently support the baseplate at all points.
The most satisfactory foundations are made of
reinforced concrete. These should be poured well in
advance of the installation to allow sufficient time for
drying and curing.
The General Arrangement Drawing (In Job’s User
Instruction) will furnish overall outline of pump
baseplate, anchor bolt locations, size of bolts, etc in
order to provide proper shape to the primary
concrete. Anchor bolts can be positioned or by a
special template (not supplied by FLOWSERVE see
figure 4.1) or by the baseplate itself if proper pockets
have been provided in primary concrete.