Flowserve ESP3 User Manual
Page 31
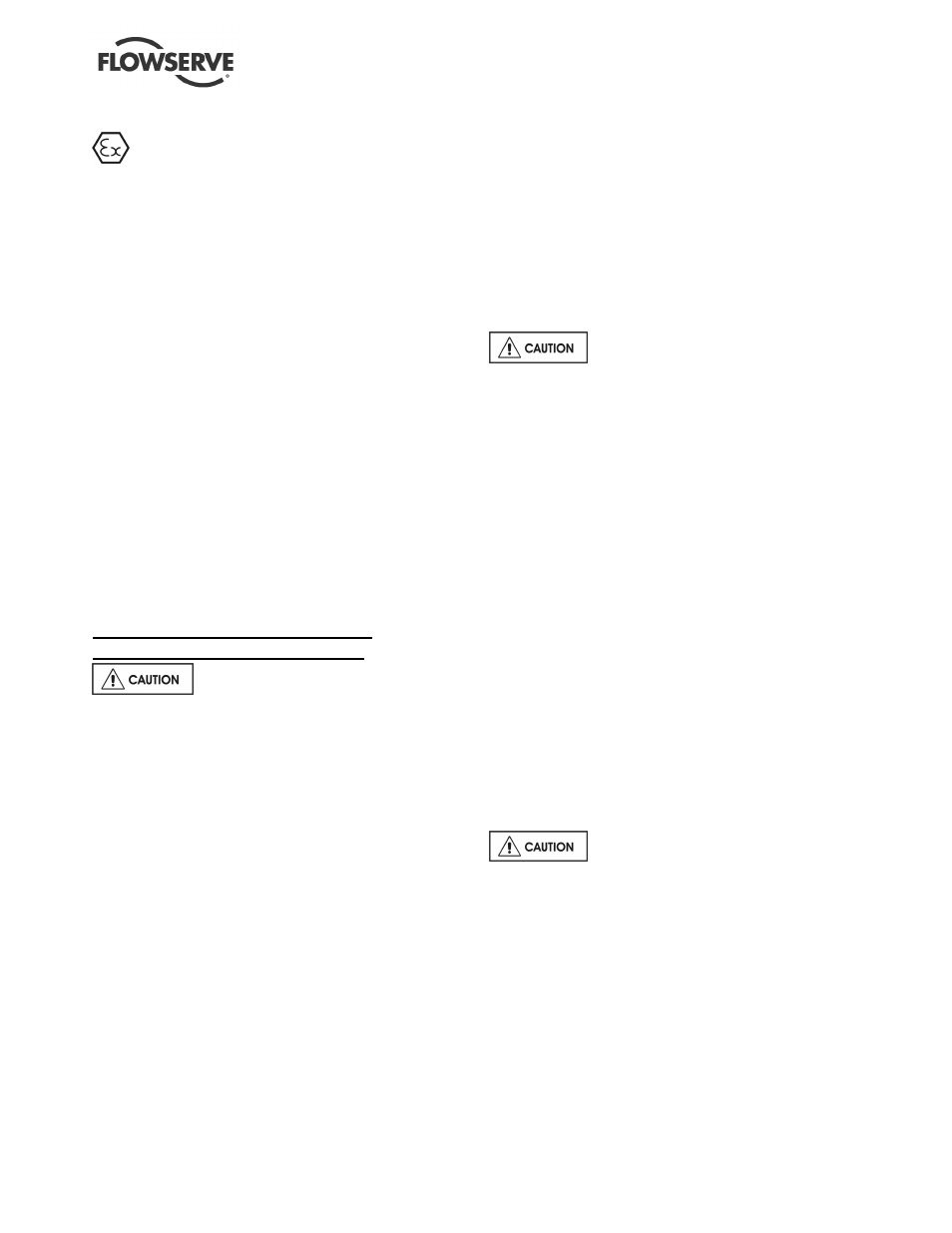
ESP3 USER INSTRUCTIONS ENGLISH 26999943 08-11
Page 31 of 64
4.12 Protection systems
The following protection systems are
recommended particularly if the pump is installed in a
potentially explosive area or is handling a hazardous
liquid. If in doubt consult Flowserve.
If there is any possibility of the system allowing the
pump to run against a closed valve or below
minimum continuous safe flow a protection device
should be installed to ensure the temperature of the
liquid does not rise to an unsafe level.
If there are any circumstances in which the system
can allow the pump to run dry, or start up empty, a
power monitor should be fitted to stop the pump or
prevent it from being started. This is particularly
relevant if the pump is handling a flammable liquid.
If leakage of product from the pump or its associated
sealing system can cause a hazard it is
recommended that an appropriate leakage detection
system is installed.
To prevent excessive surface temperatures at
bearings it is recommended that temperature or
vibration monitoring is carried out.
5 COMMISSIONING, STARTUP,
OPERATION AND SHUTDOWN
These operations must be carried
out by fully qualified personnel.
5.1 Pre-commissioning procedure
5.1.1 Pre start-up checks
Prior to starting the pump it is essential that the
following checks be made. These checks are all
described in detail in the Maintenance section of this
manual.
•
Motor properly secured to the support head
•
All fasteners tightened to the correct torque
•
Coupling guard in place and not rubbing
•
Rotation check, see section 5.4.
This is absolutely essential
•
Impeller clearance setting
•
Shaft seal properly installed
•
Seal support system operational
•
Bearing lubrication
•
Pump instrumentation is operational
•
Rotation of shaft by hand
As a final step in preparation for operation, it is
important to rotate the shaft by hand to be certain that
all rotating parts move freely, and that there are no
foreign objects in the pump casing.
5.2 Bearing Lubrication
Two types of bearings are used in the ESP3. Line
shaft bearings are used to support pump shaft within
the column. These plain bearings are lubricated by
external flush, product lubrication or grease. Duplex
angular contact bearings are used to support the
coupling end of the shaft. These ball bearings
support coupling loads and pump thrust. They are
lubricated by bearing grease. See (5.2.3)
Operation of the unit without proper
lubrication can result in bearing failures, pump
seizures and pump failure.
5.2.1 Line Shaft Bearings
Check to see that no damage has occurred to any
lubrication lines above the mounting plate [6130]
during shipment or installation. For number of
bearings, refer to Figure 5-6. Check to see that
connections are made to lubrication fittings at pump
manifold [3869] on mounting plate [6130].
5.2.1.1 External Flush Lubrication
a)
Clean liquid from an external source must be
used when pumps are furnished with external
flush lubrication connections. Liquid is typically
supplied continuously during operation. Some
bearings (such as carbon) can run without
lubrication for short periods but lubrication is
needed to dissipate heat and abrasives.
b)
Check to see that connections are made to
lubrication fittings on pump manifold [3869] on
mounting plate [6130] and that 1.9 LPM (0.5
gpm) of flushing fluid per bearing, 3.0 LPM (0.8
gpm) for Group 3, (See Figure 5-6) at 1.4 kg/cm
2
to 5.6 kg/cm
2
(20 PSIG to 80 PSIG) above sump
pressure.
It is absolutely necessary that rubber
bearings be wet at all times during operation.
5.2.1.2 Product Lubrication
When conditions warrant, the pump can be furnished
with provisions for pumped product bearing
lubrication. This is accomplished by means of a
lubrication line from the discharge flange of the pump
casing [1100] to the adapter bearing [3020.2], while
the rest of the lines are run from the manifold [3869]
on the pump mounting plate [6130]. In the case of a
pumped-product lubricated pump with separators
furnished, all lube lines will be run from the pump
manifold [3869].