9 stopping and shutdown, 10 hydraulic, mechanical and electrical duty – Flowserve ESP3 User Manual
Page 36
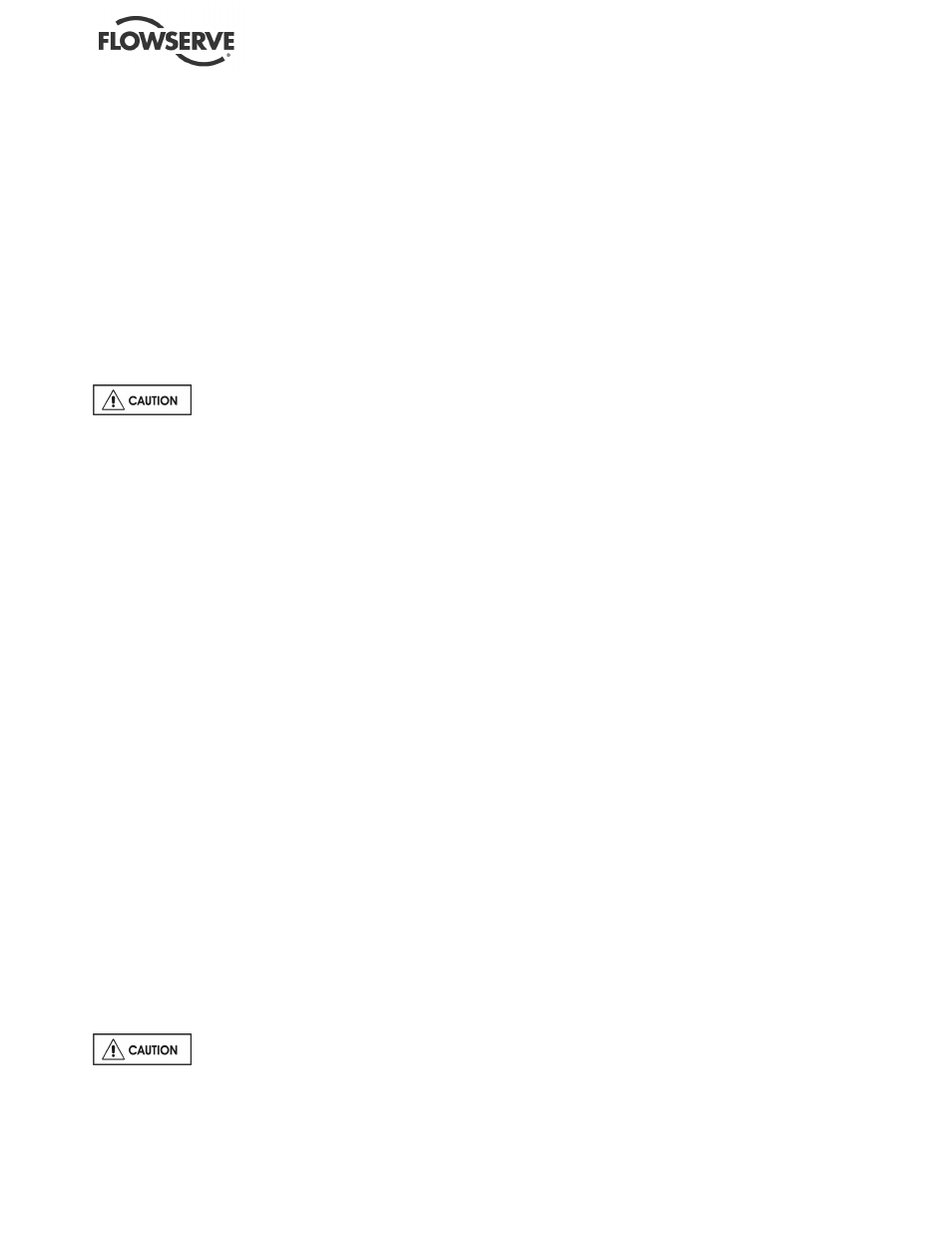
ESP3 USER INSTRUCTIONS ENGLISH 26999943 08-11
Page 36 of 64
Measuring vibration at regular intervals will show any
deterioration in pump or system operating conditions.
Vibration velocity –
unfiltered
mm/s (in./s)
r.m.s.
mm/s (in./s)
Peak value
Normal N
5.6 (0.22)
8.0 (0.31)
Alarm N x 1.25
7.0 (0.28)
9.9 (0.39)
Shutdown N x 2.0
11.3 (0.45)
16.0 (0.63)
5.9 Stopping and shutdown
5.9.1 Shutdown considerations
When the pump is being shutdown, the procedure
should be the reverse of the start-up procedure.
First, slowly close the discharge valve and shut down
the driver.
The pump should be brought to zero
speed rapidly, especially on pumps equipped with
product-lubricated bearings.
Pumps driven by electric motors do not require any
special shutdown procedure. If turbine drive is used,
the operator must manually trip the over speed trip to
obtain rapid shutdown
5.10 Hydraulic, mechanical and electrical
duty
5.10.1 Net positive suction head (NPSH)
Net positive suction head - available (NPSH
A
) is the
measure of the energy in a liquid above the vapor
pressure. It is used to determine the likelihood that a
fluid will vaporize in the pump. It is critical because a
centrifugal pump is designed to pump a liquid, not a
vapor. Vaporization in a pump will result in damage to
the pump, deterioration of the Total differential head
(TDH), and possibly a complete stopping of pumping.
Net positive suction head - required (NPSH
R
) is the
decrease of fluid energy between the inlet of the
pump, and the point of lowest pressure in the pump.
This decrease occurs because of friction losses and
fluid accelerations in the inlet region of the pump and
particularly accelerations as the fluid enters the
impeller vanes. The value for NPSH
R
for the specific
pump purchased is given in the pump data sheet,
and on the pump performance curve.
For a pump to operate properly the NPSH
A
must be
greater than the NPSH
R
. Good practice dictates that
this margin should be at least 1.5 m (5 ft) or 20%,
whichever is greater.
Ensuring that NPSH
A
is larger than
NPSH
R
by the suggested margin will greatly enhance
pump performance and reliability. It will also reduce
the likelihood of cavitation, which can severely
damage the pump.
5.10.2 Specific gravity (SG)
Pump capacity and total head in meters (feet) of
liquid do not change with SG; however pressure
displayed on a pressure gauge is directly proportional
to SG. Power absorbed is also directly proportional
to SG. It is therefore important to check that any
change in SG will not overload the pump driver or
over pressurize the pump.
5.10.3 Viscosity
For a given flow rate the total head reduces with
increased viscosity and increases with reduced
viscosity. Also for a given flow rate the power
absorbed increases with the increased viscosity, and
reduces with reduced viscosity. Product lubricated
bearings require a minimum of viscosity of 0.4 cP;
>0.6 cP is recommended for extended bearing life.
Failure to maintain sufficient viscosity will result in a
damaged shaft and bearings, and possibly a complete
stopping of pumping. It is important that checks are
made with your nearest Flowserve office if changes
in viscosity are planned.
5.10.4 Pump speed
Changing the pump speed affects flow, total head,
power absorbed, NPSH
R
, noise and vibration levels.
Flow varies in direct proportion to pump speed. Head
varies as speed ratio squared. Power varies as speed
ratio cubed. If increasing speed it is important to ensure
the maximum pump working pressure is not exceeded,
the driver is not overloaded, NPSH
A
> NPSH
R
and that
noise and vibration are within local requirements and
regulations.
The number of line shaft bearings (bearing spans) has
been selected based upon the motor speed. These
spans impact the stability of the shaft and determine it
natural frequencies. The number of line shaft bearings
can be found in Figure 5-6. The bearing spans and
critical speeds can be found in Figure 3-8. The pump
should not be operated above it designed operating
speed as this may result in severe and damaging
vibration.
The minimum speed for pump with product lube
bearings is dictated by the ability of the discharge
pressure to deliver lube to the bearings. Pumps with
product lube line shaft bearings should not be operated
at speeds that deliver less than 20 PSIG at the
mounting plate or 25 PSIG if equipped with
separator(s).