Flowserve VCT User Manual
Page 30
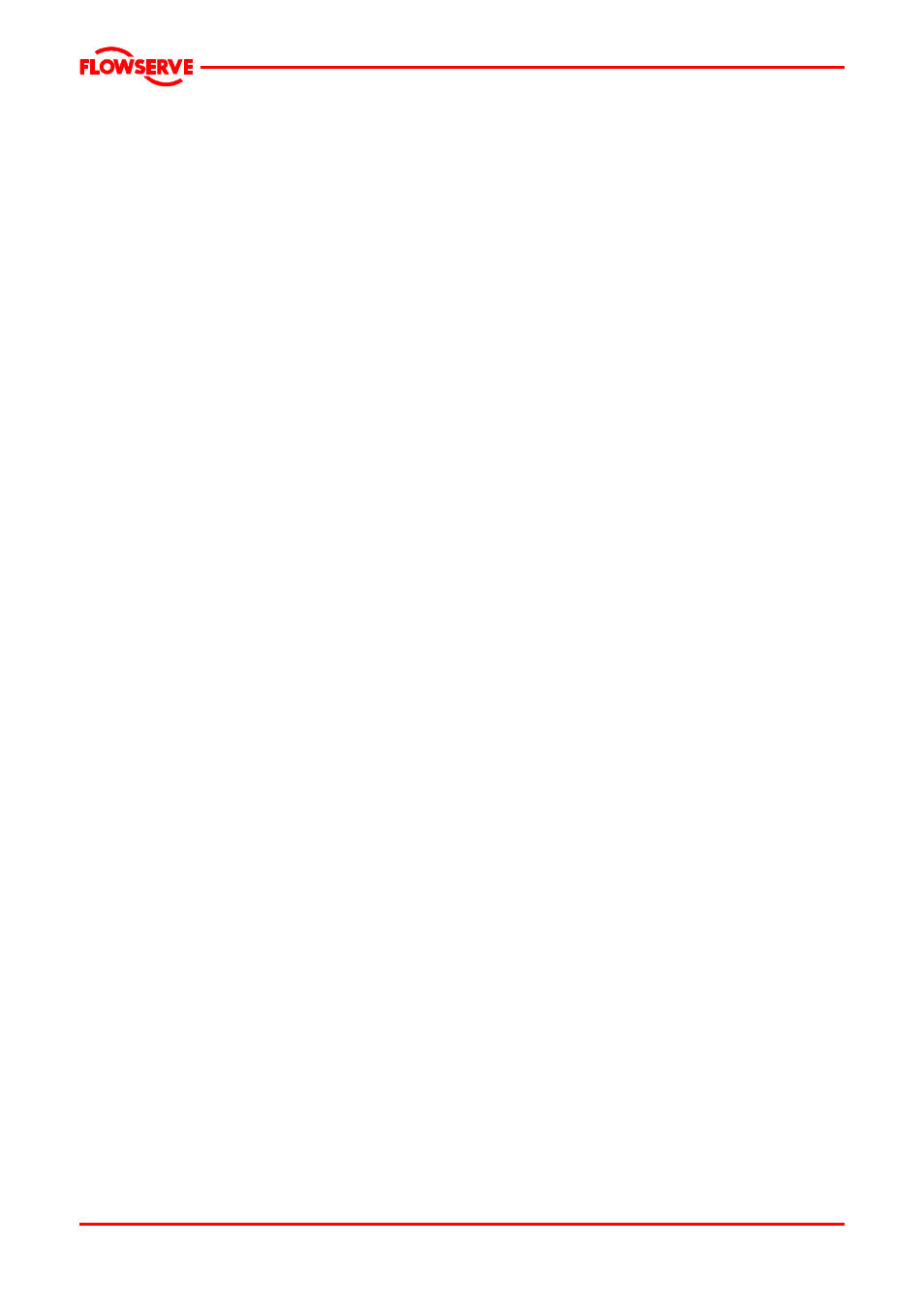
USER INSTRUCTIONS APM, APMA and APH MX0301 - 07/03
Page 30 of 32
®
If pump must be stored in a wet pit, the following inspection and maintenance procedures should
be performed:
1.
Rotor is to be lifted and blocked to dimension shown on rotor plate.
2.
Provide circulation of water in sump (high pressure water nozzles, air hoses,
etc.) and inject air into pump bell to agitate water. Take precautions that sump does not
freeze.
3.
Flush bearings with 18.93 to 37.85 L/Min. (5 to 10 GPM) of clean water for 30
minutes every 3 days. See general arrangement drawing for location of bearing injection
pipe taps. Take precautions that pipes do not freeze.
4.
Install sample metal strips (comparable to material in pump) in sump, and
inspect weekly for marine growth, corrosion, etc. Take necessary action to alleviate
problems.
5.
Check sump for silt build-up, plugging of inlet screens and trash racks within one
week of start-up.
START-UP
Prior to and during start-up, any requirement for the services of a Flowserve
representative will revert to the original contract agreement for the equipment purchased.
DRIVERS
When Motor(s) are to be shipped by the seller, each motor shall be prepared for
shipment in accordance with the Motor Manufacturers’ shipping and/or storage procedures. The
Motor(s) shall be handled with either forklift trucks or slings.
The driver rotor should be blocked to relieve bearing loads. Storage must be indoors and dry.
See the manufacturer’s storage requirements.
10.2
Coupling alignment procedure
An alternative procedure for coupling alignment is as follow:
1.
Determine type of bearings in motor. If motor has roller or ball bearings instead of sleeve
guide bearings skip the next step.
2.
If the motor guide bearings are sleeve types the motor shaft must be centered within the
sleeve bearings and that center must be maintained while completing the coupling alignment
procedure.
A). One method of centering the motor shaft in the sleeve guide bearings is to attach two dial
indicators on magnetic bases from the face of the bearing cap or end bell at 90
O
’s to each other
with the dial stems touching the shaft. Push the motor shaft as far as it will go in one direction, in
line with one of the indicators, while holding the shaft as far as it will go zero the dial and pull the
shaft back as far as it will go. Read the dial and set the shaft at ½ of the total travel. When the
shaft is set, zero the dial and leave it set. Then do the same procedure to the opposite dial
indicator. When that dial is set to zero, then, push the shaft until both dials read zero. At that
point the shaft is centered.
B). To obtain accurate alignment numbers while rotating the motor shaft, set the motor shaft to
the zero number on both dial indicators. Mount a third dial indicator from the motor coupling or
shaft and read the pump shaft or the bore of the stuffing box ext. every 90
O
’s. Stop the motor
shaft at each 90
O
point and recenter the motor shaft to the zero point on the two dials touching
the motor shaft and read the point. Do that at each point to be read on the shaft being aligned to.
3.
Remove the packing gland follower and at least two rings of packing. The motor shaft
must be centered within the stuffing box ext., within .002” using either adjustable parallels or snap