65 apm – Flowserve VCT User Manual
Page 7
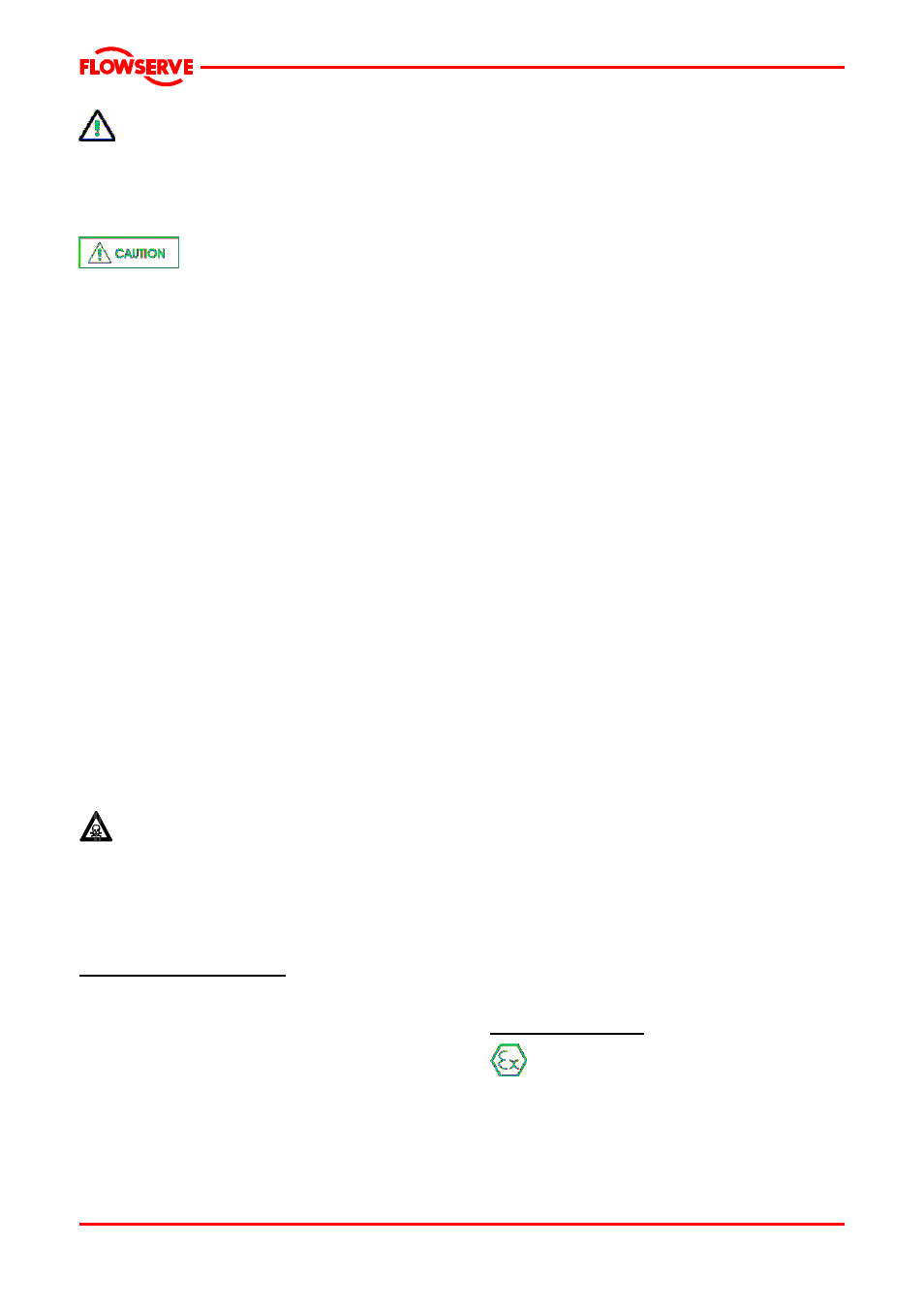
USER INSTRUCTIONS APM, APMA and APH MX0301 - 07/03
Page 7 of 32
®
Fully trained personnel must carry out lifting,
in accordance with local regulations. The driver
and pump weights are recorded on their respective
General Arrangement Drawing.
2.4 Storage
Store the pump in a clean, dry
location away from vibration. Equipment stored in
horizontal position must be placed upon enough
skids or wood blocks to prevent contact with
ground and surface contaminants. Leave piping
connection covers in place to keep dirt and other
foreign material out of pump casing.
Renew the preservative coating in areas where it
has been rubbed off or scraped including internal
areas and replace covers on openings.
Touch up the areas has been chipped or scraped.
Twice a month 180° rotation of pump is needed in
order to decrease shaft distortion due to horizontal
storage.
Longer storage periods (more than 5 months), it is
required to create and store the pump fully
disassembled when it has rubber bearings in order
to prevent rubber bearings deformation. Contact
Flowserve´s representative when longer than 5
months storage will be done ( See section 10 )
2.5 Recycling and end of product life
At the end of the service life of the product or its
parts, the relevant materials and parts should be
recycled or disposed of using an environmentally
acceptable method and in accordance with local
regulations. If the product contains substances that
are harmful to the environment, these should be
removed and disposed of in accordance with
current local regulations.
Make sure that hazardous substances are
disposed of safely and that the correct personal
protective equipment is used. The safety
specifications must be in accordance with the
current local regulations at all times.
3 PUMP DESCRIPTION
3.1 Name nomenclature
The pump size will be engraved on the nameplate
as exemplar below:
65 APM
Where:
Nominal size: 65
Pump type: APM
The typical nomenclature above is the general
guide. Identify the actual pump size and serial
number from the pump nameplate. Check that this
agrees with the applicable certification provided.
3.2 Design of major parts
3.2.1 Bowl.
The pump has its main part in the bowl which
conducts liquid from impeller to column pipe and
converts to pressure the velocity added by the
impeller.
3.2.2 Impeller
The impeller is semi-open type and it is dynamically
balanced
3.2.3 Shaft
The large diameter stiff shaft, supported by
bearings is accurately machined.
3.2.4 Bearings and lubrication
Bearings are fitted as standard and are lubricated
by pumped liquid.
3.2.5 Suction bell
This piece approaches liquid to impeller eye in
optimum way.
3.2.6 Stuffing box housing
The stuffing box contains packing which controls
leakage thru pump shaft passage.
3.2.7 Driver
The driver is normally an electric motor. Different
drive configurations may be fitted such as internal
combustion engines, turbines, hydraulic motors etc.
driving via couplings, belts, gearboxes, drive shafts
etc.
3.2.8 Accessories
Accessories may be fitted when specified by the
customer on data sheet or purchase order.
3.3 Performance and operating limits
This pump has been selected to meet the
specifications of your purchase order for more
details see attachment in this User Instructions.
4 INSTALLATION
Equipment operated in hazardous locations
must comply with the relevant explosion protection
regulations.
4.1 Location
The pump should be located to allow room for
access, ventilation, maintenance and inspection