Flowserve VCT User Manual
Page 9
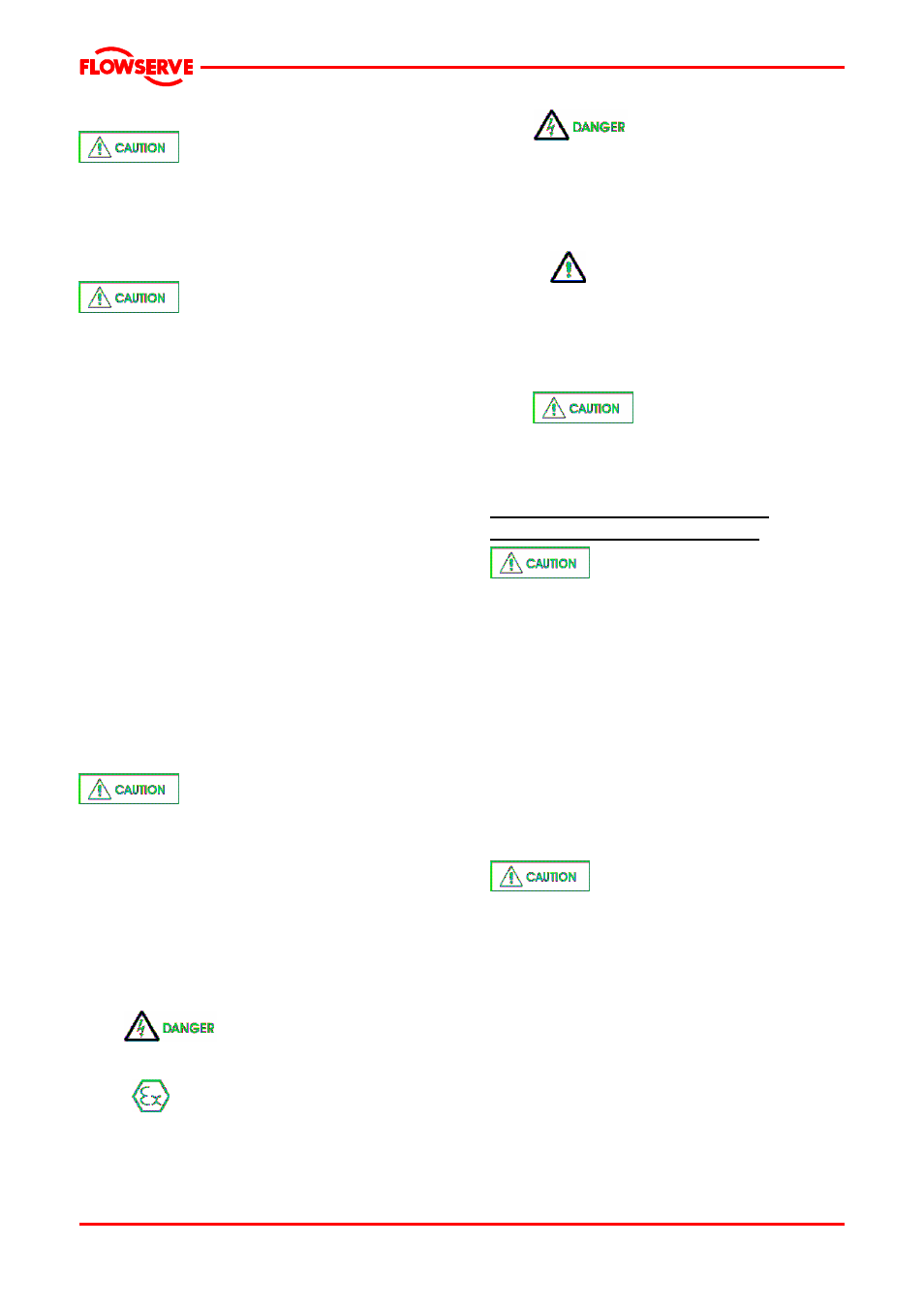
USER INSTRUCTIONS APM, APMA and APH MX0301 - 07/03
Page 9 of 32
®
4.6 Piping
Protective covers are fitted to the
discharge flange, pipe connections and suction
head, to prevent foreign bodies entering during
transportation and installation. Ensure that these
covers and shipping brace are removed from the
pump before connecting any pipes.
Never use the pump as a support
for piping.
Maximum forces and moments allowed on the
pump flanges vary with the pump size and type
(see general arrangement drawing for specific
values). To minimize these forces and moments
that may, if excessive, cause misalignment,
vibration and the possible failure of the pump , the
following points should be strictly followed:
•
Prevent excessive external pipe load, design
piping system to minimize pump nozzle loads.
•
Permit no excessive strain on the pump
discharge flange
•
Never draw piping into place by applying force
to pump flange connections
•
Provide expansion joints with tie rods of
suitable strength ( sized for 1 ½ times shut off
pressure).
•
Discharge valve should be located at least one
pipe diameter from face of pump discharge
flange.
•
Special considerations and provisions must be
made to avoid the chance of water-hammer
during pump operation and start up pump.
Ensure piping is flushed before use.
4.7 Final shaft alignment check
After connecting piping to the pump, rotate the
shaft several times by hand to ensure there is no
binding and all parts are free.
Recheck the coupling alignment, as previously
described, to ensure no pipe strain. If pipe strain
exists, correct piping, see point 4.5.2
4.8 Electrical connections
4.8.1
Electrical connections must be
made by a qualified Electrician in accordance with
relevant local national and international regulations.
4.8.2
It is important to be aware of the
potentially explosive areas where compliance is an
additional
requirement for making
electrical
connections.
4.8.3
The motor must be wired up in
accordance
with
the
motor
manufacturer's
instructions in this user instructions including any
temperature, earth leakage, current and other
protective
devices
as
appropriate.
The
identification nameplate should be checked to
ensure the power supply is appropriate.
4.8.4
A device to provide emergency
stopping must be fitted.
4.8.5 The controller/starter electrical details will
also be supplied within the controller/starter when
applied.
4.8.6
See section 5.3, Direction of
rotation before connecting the motor to the
electrical supply.
5 COMMISSIONING, START-UP,
OPERATION AND SHUTDOWN
These operations must be carried
out by fully qualified personnel.
5.1 Pre-commissioning procedure
5.1.1 Lubrication
Determine the mode of lubrication of the pump-
motor set and supply it.
5.2 Motor lubricants
See Motor’s manual and motor outline in
attachment in these User Instructions for motor
lubrication details before any start up or test.
5.3 Direction of rotation
Ensure the pump motor is given the
same rotation as the pump direction arrow marked
on the pump nameplate and Outline Drawing.
Some vertical motors are required to have non
reverse couplings (non reverse device), to avoid
pump-motor back spinning do to water column flow
back during shutdown.
However the device is designed to support the
forces developed by the pump, when the water is
flowing back, which is increase gradually, the
device is not expected to support the motor torque,
which is suddenly applied as a shock a would
damage the pins or ratchet plate teeth; Base on
this, the motor must never be started against the
ratchet pins, to avoid pins or ratchet plate damage