3 asme valve troubleshooting chart – Flowserve Valtek Mark 200 User Manual
Page 10
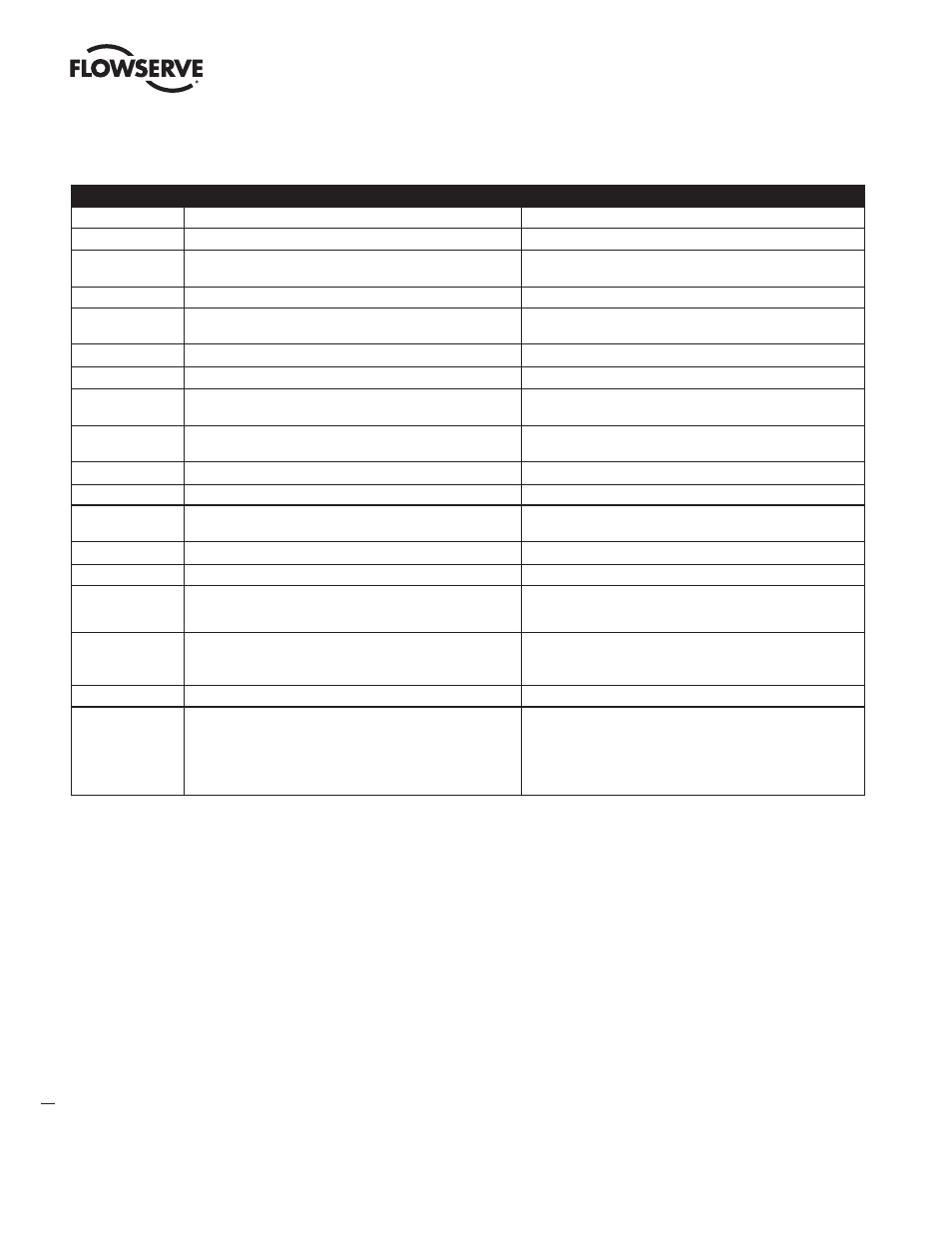
Mark 200 Control Valve FCD VLENIM0200– 12/12
10
6.3 ASME Valve Troubleshooting Chart
Problem
Possible Cause
Corrective Action
Stem motion impeded 1. Overtightened packing.
1. Refer to proper maintenance instructions and readjust.
2. Service temperature is beyond operating limits of trim design.
2. Reconfirm service conditions and contact factory.
3. Inadequate air supply. *
3. Check for leaks in air supply or instrument signal system; tighten
loose connections and replace leaky lines.
4. Malfunctioning positioner. *
4. Refer to positioner maintenance instructions.
Excessive leakage
1. Improperly tightened bonnet flange bolting.
1. Refer to step 11 of “Reassembling the Body” section for
correct tightening procedure.
2. Worn or damaged seat ring.
2. Disassemble valve and replace or repair seat ring.
3. Worn or damaged seat or bonnet gasket.
3. Disassemble and replace gaskets.
4. Inadequate actuator thrust.
4. Check for adequate air supply to actuator; if air supply is
adequate, reconfirm service conditions and contact factory.
5. Incorrectly adjusted plug.
5. Refer to step 9 of “Reassembling the Body” section for correct
plug adjustment.
6. Improper flow direction.
6. Refer to original specifications or contact factory.
7. Improper handwheel adjustment; handwheel acting as a limit-stop. *
7. Adjust handwheel until plug seats properly.
Inadequate flow
1. Improper plug adjustment, limiting stroke.
1. Refer to step 9 of “Reassembling the Body” section for
correct plug adjustment.
2. Malfunctioning positioner. *
2. Refer to positioner maintenance instructions.
3. Service conditions exceed trim design capacity.
3. Verify service conditions and consult factory.
Plug slams
1. Incorrect plug adjustment allowing improper cushion of air between
actuator piston and yoke.*
1. Refer to step 9 of “Reassembling the Body” section for
correct plug adjustment.
2. Inadequate air supply. *
2. Check air supply to actuator; repair leaks and remove any
restrictions in supply line.
3. Trim sized too large for flow rate.
3. Install reduced trim.
Valve does not fail in
correct position
1. Incorrect flow direction.
1. Reconfirm direction and, if necessary, correct flow direction
through valve.
* Pneumatic operated control valves