Stem position sensor, Led indicators, Quick-cal button – Flowserve 1000 Series Digitial Positioner User Manual
Page 11
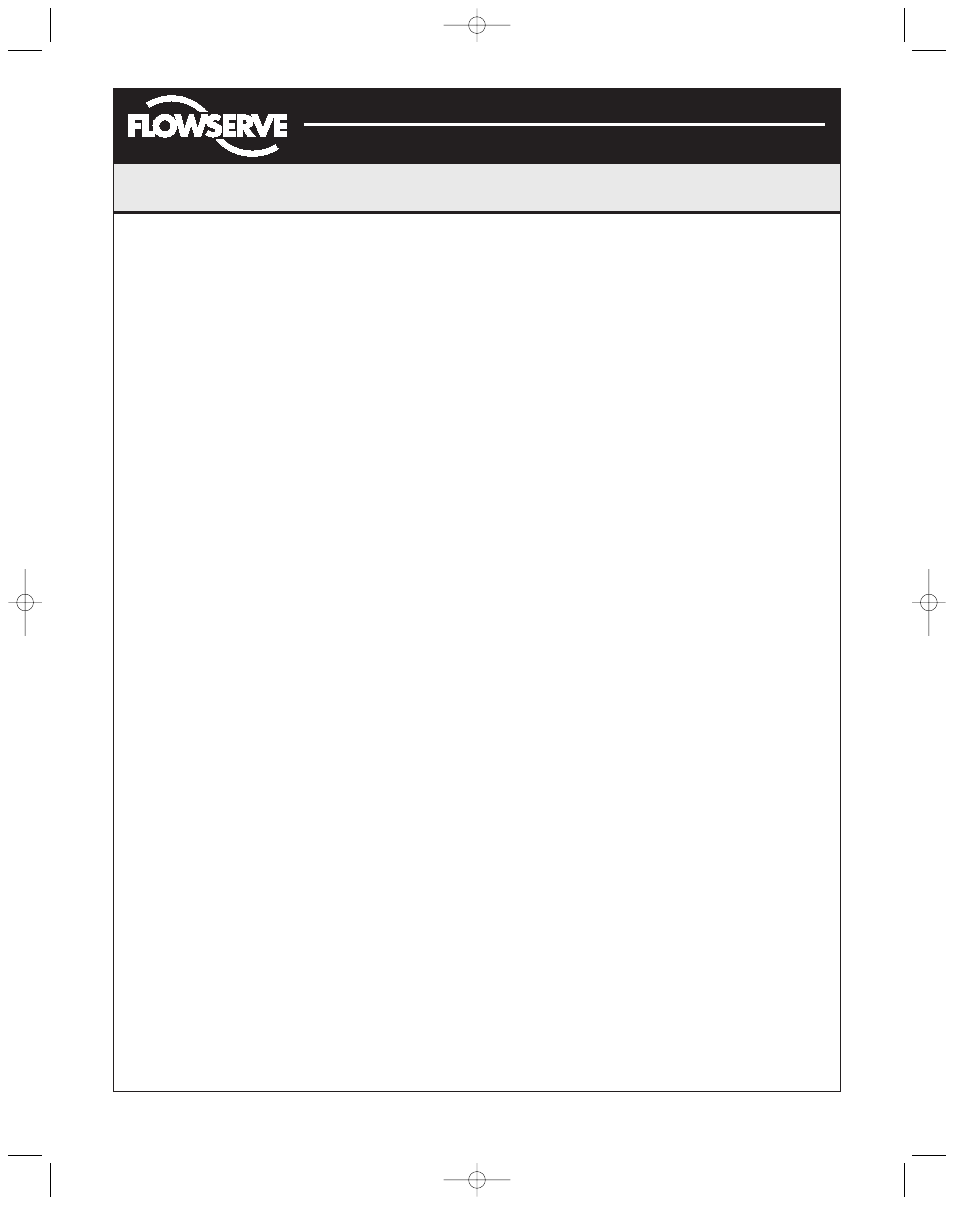
FCD AXAIM0064-00 (AUTO-64) 08/04
Page: 11 of 16
© 2004, Flowserve Corporation, Printed in U.S.A.
Logix Series 1000 Digital Positioner
Installation, Operation and Maintenance Instructions
Flowserve Corporation
1350 N. Mountain Springs Parkway
1978 Foreman Dr.
Flow Control Division
Springville, Utah 84663-3004
Cookville, TN 38501
www.flowserve.com
Phone: 801 489 2233
Phone: 931 432 4021
© TriCom, Inc., 2004, All Rights Reserved.
Replacing Field Terminations Board (Figure 19)
1. Make sure valve is bypassed or in a safe condition.
2. Disconnect the power and air supply to the unit.
3. Remove the main cover and disconnect the field
termination cable from collector board.
4. Remove the field terminations cover and the three
No. 8-32 screws.
5. Remove field terminations board, carefully pulling
wiring through bore.
6. Verify that the O-ring is in place in the counter bore in
the positioner housing.
7. Feed wiring through passageway into main chamber
of housing.
8. Set the circuit board in place and secure with three
No. 8-32 screws.
9. Connect field termination cable to collector board.
Stem Position Sensor
The position feedback assembly transmits valve position
information to the processor. This is accomplished by
means of a rotary position sensor that connects to the
valve stem through a feedback linkage. To provide
accurate tracking of the pin in the slot, the follower arm
is biased against one side of the slot with a rotary spring.
This spring also automatically moves the position
feedback assembly to its limit in the unlikely event of
failure of any component in the linkage.
Stem Position Sensor Replacement (Figures 15, 19)
1. Make sure valve is bypassed or in a safe condition.
2. Disconnect the power and air supply to the unit.
3. Remove the main cover and disconnect rotary position
sensor wires from collector board.
4. Remove the two screws from rotary position sensor
and remove the sensor from the housing.
5. Turn position sensor shaft until the dot on the slot is
oriented with the wires on the pot (Figure 15).
6. Insert the position sensor into the shaft with the wires
pointing toward the main PCB assembly. Turn the
position sensor clockwise until the bolting slots align
with the housing screw holes and the wires on the
sensor protrude over the main PCB assembly tray.
7. Carefully center position sensor on the shaft bore,
insert and tighten the screws. Do not over tighten.
8. Route wires along the position sensor and reconnect
to sensor board.
LED Indicators
The Logix 1200 positioner has three LED indicators that
are visible through a window in the main cover. Only one
LED will blink at any given time. Each LED has a different
color to convey basic information about the positioner
status. Green indicates that the positioner is operating
normally. Yellow indicates that a ‘customer defined limit’
or ‘alert’ has been reached. Red indicates that an error
condition exists. The HART hand-held communicator or
ValTalk PC software must be used to determine the
specific reason for a yellow or red LED status.
During stroke and actuator calibration, no LED will blink.
After calibration is complete, the green LED indicates that
the calibration was completed successfully. If the yellow
or red LED blinks after a calibration process, a warning or
error was detected and the HART hand-held or ValTalk
must be used to identify the specific calibration error.
NOTE: If the LED indicator changes from green to yellow
after a calibration process, the user may have set a
warning limit (position alert, cycle counter alert, etc.).
Use the HART hand-held communicator or ValTalk to
monitor status.
Quick-Cal Button
If the HART hand-held communicator or ValTalk PC
software is not available, the Logix 1200 positioner has a
Quick-Cal™ feature that performs a stroke calibration and
allows basic operation of the positioner.
NOTE: The Quick-Cal operation retains all previously
configured information. All settings remain unchanged
except stroke calibration parameters. If the device is
being installed for the first time, factory default
parameters are used.
The Quick-Cal button and DIP switch settings are located
on the collector board inside the main housing chamber
as shown in Figure 16.
Caution: Accessing this function requires removal of the
main cover. The user must take all precautions if this
operation is performed in explosion-proof areas or
serious injury can occur.
Make the appropriate configuration settings, using the DIP
switches on the collector board. ATO/ATC selects air-to-
(AXAIM0096-00) Logix 1000 IOM 8/6/04 3:34 PM Page 11